Zplyňování – principy a reaktory
Článek popisuje principy a reaktory používané při zplyňování. Jednoduše řečeno jedná se o proces, ve kterém z tuhých paliv (uhlí, odpady a biomasa) získáme plyn. Plyn můžeme využít v kogenerační jednotce (pístový motor nebo spalovací turbína) k výrobě elektrické a tepelné energie s vyšší účinnosti, než klasickým spálením v kotlích. Všechny procesy probíhají v reaktoru za kontrolovaného přívodu zplyňovacího media (vzduch, kyslík nebo pára) a potřebného reakčního tepla.
1. Co je to zplyňování
Zplyňování je průběh několika procesů, při kterých postupně dochází k oxidaci uhlovodíků s vodní párou z paliva (nebo zplyňovacího media) a následně dochází k redukci na hořlavé plyny, destilační produkty a minerální zbytek.
Z chemického hlediska je proces zplyňování biomasy složitý a zahrnuje mnoho kroků, mezi něž patří:
- tepelný rozklad paliva na plyn, kondenzující páry a dřevěné uhlí tzv. pyrolýza,
- následné tepelné štěpení par na plyn a pevný uhlík,
- zplyňování pevného uhlíku vodní parou nebo oxidem uhličitým,
- částečná oxidace hořlavých plynů, vedlejších složek a pevného uhlíku.
Při srovnání spalovacího procesu, kdy se chemická energie obsažena v palivu transformuje na tlakovou energii páry nebo vody, dochází při zplyňování k transformaci na jiný druh chemické energie, která se váže na plynnou fázi. Dochází k tepelné rovnováze mezi reakcemi spotřebovávajícími teplo (endotermickými) a reakcemi produkujícími teplo (exotermickými).
2. Historie zplyňování
Nejdůležitější zmínkou v historii zplyňování bylo objevení uvolňování plynu při suché destilaci uhlí a dřeva v 17. století.
První patent na technologii zplyňování získal Robert Gardner v roce 1788. K prvnímu praktickému využití získaného plynu došlo až v roce 1792 Wiliamem Murdochem, který jeho spalováním zajistil osvětlení svého domu.
Za první úspěšnou konstrukci zplyňovacího reaktoru lze považovat reaktor bratří Siemensů, patentovanou v roce 1861. V roce 1876 sestrojil Nicolas August Otto první čtyřtaktní motor poháněný plynem generovaným z uhlí. Díky toho se zachoval pojem „plynový pedál“.
V roce 1922 vyvinul německý výzkumník Winkler fluidní zplyňovací generátor na uhelný prach a v roce 1923 si francouzský inženýr Imbert patentoval souproudý zplyňovací reaktor. Další typy reaktorů na sebe nenechaly čekat. Firma Lurgi představila tlakový reaktor s pohyblivým ložem v roce 1931 a následně v roce 1941 pánové Koppers – Totzek reaktor s unášivým proudem. V průběhu 2. světové války, kdy byl nedostatek benzínu a došlo k rozšíření zplyňovacích jednotek převážně ve formě mobilních zplyňovacích reaktorů. Tyto reaktory vyráběly plyn pro pohon dopravních prostředků. Německo bylo během 2. světové války donuceno využívat syntézy dle Fishera – Tropsche a Bergiuse k získání pohonných hmot a chemických látek z plynu získaného zplyňováním uhlí nebo dřeva.
Po ukončení 2. světové války se kvůli dobře dostupné ropě význam zplyňování snížil. Během ropných krizí nenastal výrazný vývoj ani uplatnění technologie zplyňovaní. Výjimkou byly rozvojové země, ve kterých fungovaly jednotky původně vyvinuté ve vyspělých zemích.
3. Procesy probíhající při zplyňování
Zplyňování využívá termochemických procesů, které se skládají z několika procesů navazujících na sebe. Probíhající fáze každého procesu se prostorově i časově rozdělují do jednotlivých fází. Toto rozdělení lze realizovat pouze u reaktoru s pevným ložem viz Obr. 1. U reaktoru pracujícího se zplyňováním ve vznosu (tzv. fluidní reaktor) se jednotlivé fáze nedají rozdělit, ale všechny fáze probíhají v celém reaktoru současně.
Procesy se rozdělují na pásma:
- sušení paliva – ohřev paliva s odpařením vázané vody,
- pyrolýza – tepelný rozklad paliva na plynné složky, kondenzující páry, polokoks, následné tepelné štěpení par na plyn a pevný uhlík,
- oxidace – částečná oxidace hořlavých plynů, složek a pevného uhlíku,
- redukce – zplyňování pevného uhlíku párou nebo oxidem uhličitým.
Procesy jsou ovlivňovány zejména:
- provozní teplotou a teplotním profilem v reaktoru,
- provozním tlakem v reaktoru,
- obsahem vlhkosti v palivu a zplyňovacím mediem,
- reakčním povrchem,
- dobou setrvání složek v reaktoru.
3.1. Sušení
Palivo se vysušuje při teplotě do 200 °C, při tom dochází k odpařování vody vázané v palivu. Sušení potřebuje velké množství tepla pro zajištění optimální vlhkosti paliva 15 %. Uvolněná voda vypařováním může reagovat v redukčním pásmu (souproudý reaktor) nebo odchází ve vyrobeném plynu (protiproudý reaktor).
3.2. Pyrolýza
Pyrolýza je tepelný rozklad paliva bez přístupu oxidačního media (kyslíku, vzduchu). Vznikají pevné, kapalné a plynné produkty, jejichž vznik je ovlivněn chemickým složením paliva (biomasa, odpady) a podmínkami pyrolýzy. Pyrolytický proces je velmi důležitý, jelikož zahrnuje reakce v pevné i plynné fázi, které ovlivňují kvalitu vyrobených produktů.
V teplotním pásmu 300-500 °C dochází k suché destilaci, při které dojde ke štěpení řetězců z vysokomolekulárních organických látek a přeměně na plynné a kapalné organické produkty a polokoks. Po zvýšení teploty na 500–700 °C jsou produkty suché destilace dále štěpeny a transformovány z kapalných organických látek i z pevného uhlíku na plynné látky – vodík H2, oxid uhelnatý CO, oxid uhličitý CO2 a metan CH4.
Produkty pyrolýzy rozdělujeme podle skupenství na tuhé, kapalné a plynné.
Tuhý pyrolýzní zbytek získaný pomalou pyrolýzou se skládá z 80–85 % tuhého uhlíku (polokoks), 15–20 % prchavých látek a 0–2 % popela. Popel je závislý na obsahu popeloviny v palivu.
Pyrolýzní kapalinou je myšlen pyrolýzní olej, který je dobře znám jako produkt pomalých pyrolýzních procesů. Pyrolýzní olej z biomasy je směsí tmavě hnědých, viskózních, kyselých produktů s různými vlastnostmi a může být kontaminován tuhými látkami a vodou (obsah vody 20 % podle vlhkosti paliv).
Plynné produkty vzniklé při rychlé pyrolýze představují přibližně 5 % obsahu energie biomasy a v případě pomalé pyrolýzy 25–30 %. Při teplotách nad 500 °C je vyprodukováno 75–90 % prchavé hořlaviny. Mezi hlavní složky (až 95 %) patří oxid uhelnatý CO, oxid uhličitý CO2, metan CH4, vodík H2, vodní pára H2O. Výhřevnost vyrobeného plynu se pohybuje v rozmezí 3,5 až 8,9 MJ/m3.
3.3 Oxidace
Pásmo oxidace se nachází v oblasti přívodu zplyňovacího média. Spalovací exotermická reakce v této oblasti dodává potřebné teplo pro endotermickou reakci zplyňovacího procesu.
Při použití zplyňovacího media kyslíku nebo vzduchu (stechiometrický koeficient mezi 0,3 až 0,5) se vytváří v oblasti vstupu tohoto media oxidační vrstva s teplotou mezi 800–1500 °C. Oxidace uhlíku a plynných produktů pyrolýzy probíhá podle následujících rovnic:
Částečná oxidace pevného uhlíku:
C + ½ O2 → CO ∆H = −111 kJ/mol
Úplná oxidace pevného uhlíku:
C + O2 → CO2 ∆H = −394 kJ/mol
Oxidace oxidu uhelnatého CO:
CO + ½ O2 → CO2 ∆H = −283 kJ/mol
Oxidace vodíku H2:
H2 + ½ O2 → H2O ∆H = −242 kJ/mol
Oxidace metanu CH4:
CH4 + 2 O2 → CO2 + 2 H2O ∆H = −802 kJ/mol
3.4. Redukce
Spalitelné látky ve vyráběném plynu vznikají redukcí oxidu uhličitého CO2 na oxid uhelnatý CO (Boudouardova reakce) a vodní páry H2O na vodík H2 (heterogenní reakce vodního plynu). Současně může uhlík reagovat s vodíkem za vzniku metanu CH4. Všechny tyto reakce přispívají k výrobě plynného paliva. Reakce probíhají bez přítomností kyslíku, díky tomu se teplota plynu snižuje a většina uhlíku je spálena nebo zredukována na oxid uhelnatý CO, případně odchází z reaktoru v popelu ve formě nedopalu:
Boudouardova reakce:
C + CO2 ↔ 2 CO ∆H = 173 kJ/mol
Heterogenní reakce vzniku vodního plynu:
C + H2O ↔ CO + H2 ∆H = 131 kJ/mol
Heterogenní vznik metanu:
C + 2 H2 ↔ CH4 ∆H = −87 kJ/mol
Současně s těmito reakcemi probíhají i další reakce:
Homogenní reakce vodního plynu:
CO + H2O ↔ CO2 + H2 ∆H = −41 kJ/mol
Homogenní vznik metanu:
2 CO + 2 H2 ↔ CH4 + CO2 ∆H = −247 kJ/mol
CO2 + 4 H2 ↔ CH4 + 2 H2O ∆H = −41 kJ/mol
Homogenní redukce oxidu uhličitého:
CO2 + H2 ↔ CO + H2O ∆H = 41 kJ/mol
Konečný plyn se skládá z oxidu uhelnatého, vodíku a metanu, dále plyn obsahuje vodní páru, oxid uhličitý a dusík.
4. Druhy zplyňovacích reaktorů
V průběhu vývoje zplyňovacích technologií byly navrženy, zkonstruovány a testovány reaktory v různých provedeních. Postupem času byly tyto reaktory inovovány pro zajištění zvýšení jejich výkonu, provozního tlaku a pro zlepšení využití.
Reaktory můžeme rozdělit podle různých hledisek.
Podle konstrukce reaktoru:
- s pevným ložem (moving bed) – souproudé, protiproudé, s křížovým tokem,
- s fluidním ložem (fluidized bed),
- s unášivým proudem (entrained flow).
Podle zplyňovacího media:
- parní,
- parokyslíková směs,
- kyslíkové,
- vzduchové.
Podle zdroje tepla pro zplyňování:
- autotermní neboli přímý zplyňovací reaktor – teplo dodáváno spalováním části biomasy,
- kyslíkové,
- alotermní neboli nepřímý zplyňovací reaktor – teplo je dodáváno nepřímým ohřevem (oddělení zplyňovací a spalovací zóny) nebo z externího zdroje přes výměník tepla.
Podle tlaku v reaktoru:
- atmosférické,
- tlakové.
4.1. Zplyňovací reaktor s pevným ložem
Reaktor s pevným ložem patří mezi nejrozšířenější typ reaktoru využívaný na zplyňování biomasy. Na obrázku 2. je vidět zplyňovací proces a proudění tepla dílčími procesy zplyňování. Teplo potřebné pro proces zplyňování může být přiváděno přímo s palivem (autotermní) nebo nepřímým předáním tepla přes výměník tepla (alotermní). Můžeme je dělit podle směru toku pevných částic a proudu plynu na souproudé, protiproudé a s křížovým prouděním. Dále podle směru proudění plynu reaktorem na updraft (vzestupné proudění), downdraft (klesající proudění). Nejčastěji se používá dělení podle prvního členění, protože má na procesy zplyňovaní vliv směr proudu paliva a proud plynu, reaktor typu downdraft je považován za souproudý a reaktor updraft za protiproudý.
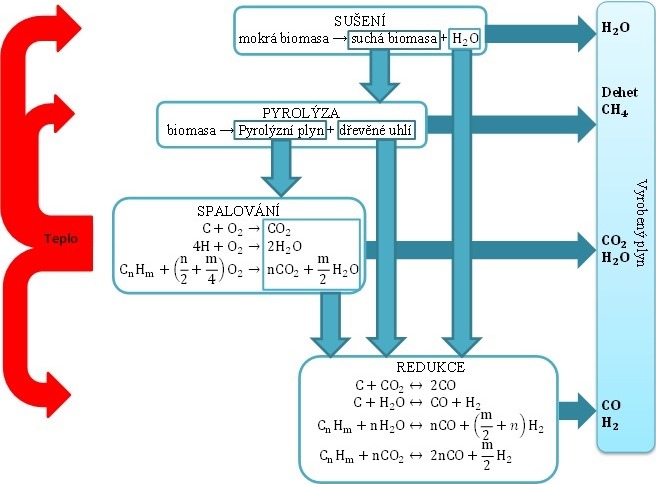
Obr. 2. Průběh zplyňovacích procesů
Dnešní moderní reaktory jsou vyvíjeny pro snížení tvorby dehtů. Tyto reaktory pracují ve vícestupňovém zplyňování a nepřímém zplyňování. Snaží se oddělit jednotlivé procesy, aby byly dehty spáleny v plynném stavu a bez přítomnosti pevných paliv. Tím by se zlepšily podmínky pro smíchání se vzduchem.
4.2. Protiproudý reaktor „UPDRAFT“
Tento typ reaktoru patří mezi nejrozšířenější, protože je technicky nejjednodušší viz Obr. 3. Přívod paliva je v horní části reaktoru a palivo se pohybuje směrem dolů, protože dochází ke zplyňování a odvodu popela. Zplyňovací medium (vzduch, pára) je přivedeno ve spodní části reaktoru. Vzniklý plyn proudí v proti směru přívodu paliva a prochází zplyňovacími pásmy redukčním, pyrolýzním a sušicím. Ve všech pásmech předává své teplo a tím se ochlazuje pod 250 °C a pohlcuje pyrolýzní produkty a vodní páru. Výhodou tohoto typu reaktoru je možnost použití různých druhů paliva a také umožnuje zplyňovat paliva s vyšším obsahem vlhkosti (do 30 %). Vnitřní výměna tepla nám umožnuje dosahovat maximálních účinnosti a co největšího využití tepla. Díky těmto možnostem má vnikající plyn výhřevnost 6 MJ/mN3 a nízkou teplotu. Nevýhodou je vyšší obsah dehtových látek a pyrolýzních produktů v plynu a vznik nízkovýhřevného plynu při náběhu zařízení.
4.3. Souproudý reaktor „DOWNDRAFT“
Souproudý reaktor nejčastěji používá dopravu paliva do horní častí reaktoru a přívod zplyňovacího media je shora nebo z boku. Vyrobený plyn proudí stejným směrem jako palivo.
Nejpoužívanější konstrukce souproudového reaktoru je od francouzského inženýra Imbertena, který navrhl hrdlo ve tvaru „V“. Konstrukce vychází z patentu podtlakového reaktoru z roku 1923.
U tohoto reaktoru jsou stejné procesní zóny jako u protiproudého reaktoru, ale v jiném pořadí viz Obr. 4. V pyrolýzně-oxidačním pásmu vznikají pyrolýzní produkty, které se štěpí na rozžhaveném uhlí v redukčním pásmu a z tohoto důvodu jejich celkové množství klesá. V nejužším místě reaktoru se nachází oxidační pásmo, do kterého se přivádí zplyňovací medium. Výhřevnost vyrobeného plynu je až 5 MJ/mN3. Nevýhodami této koncepce je vyšší teplota vyrobeného plynu, protože prochází přes redukční pásmo a také vyšší obsah prachových částic v plynu. Citlivost na velikost vstupního paliva (zrnitost 4–10 cm) a obsahu vlhkosti v palivu.
4.4. Reaktor s křížovým tokem
Reaktor s křížovým tokem (Obr. 5.) byl navržen pro zplyňování dřevěného uhlí. Proces zplyňování se vyznačuje vysokými teplotami (až 1500 °C), tato teplota může vést k problémům s odolností konstrukčního materiálu reaktoru. Reaktor pracuje v malém rozsahu pracovního výkonu. Výhodou takto vyrobeného plynu je jednoduchost čištění, kdy postačuje cyklon a filtr. Nevýhodou je zanedbatelný rozklad dehtu a vysoké nároky na kvalitu dřevěného uhlí.
4.5. Zplyňovací reaktor s fluidním ložem
Reaktor s fluidním ložem byl vyvinut firmou Winkler v roce 1926 a měl se používat pro zplyňování uhlí. V pozdějších letech se reaktory začaly používat pro zplyňování biomasy, a tím se předcházelo provozním problémům zplyňovacích reaktorů s pevnou vrstvou. Mezi problémy patří:
- zplyňovaní paliva s vysokým obsahem popela,
- problém s malými částicemi kvůli ucpávání (zvyšovaní tlakových ztrát),
- klenbování paliva a tvorba kanálů,
- nerovnoměrné rozložení teplot v procesních pásmech.
U reaktoru s fluidním ložem (viz Obr. 6.) se palivo (piliny, štěpka, pelety s velikosti 2–20 mm) zplyňuje ve vznosu. Před začátkem zplyňování leží palivo s inertním materiálem (písek, keramika, popel) na porézním dně. Zespodu je přiváděno zplyňovací medium (vzduch, kyslík, pára) pro zajištění překonání prahové rychlosti fluidace (překonaní tíhové síly působící na materiál). Tehdy začne palivo a inertní materiál vířit a chovat se jako tekutina. Za zvyšující se rychlosti se vrstva paliva začne nejprve rozpínat a snižovat svou hustotu. Po dosažení rychlosti úletu začnou jednotlivé částečky ulétávat.
U reaktoru s fluidním ložem probíhají stejné procesy jako u reaktoru s pevným ložem, ale u fluidního lože probíhají procesy najednou v celém reaktoru. Pouze místo přívodu zplyňovacího media (těsně nad roštem) můžeme označit jako oblast převažující oxidační reakce nad redukční. Pro nahřátí inertního materiálu se používá uhlí, po nahřátí a spálení uhlí se začne přivádět biomasa pro zplyňování. Při zplyňování ve fluidní vrstvě dojde ke spálení kolem 25 % biomasy a zbytek se zplyní. Teplota fluidní vrstvy se pohybuje v rozmezí 700–900 °C.
Porovnání reaktoru s fluidním ložem vůči reaktoru s pevným ložem:
Výhody:
- kompaktní konstrukce z důvodu vysoké výměny tepla a reakčních rychlosti v důsledku intenzivního míchání v loži,
- rovnoměrné rozložení teplotního profilu,
- možnost využití více druhů paliva (vlhkost, obsah popela, zrnitosti paliva),
- relativně nízká provozní teplota
Nevýhody:
- vysoký obsah dehtu a prachu ve vyrobeném plynu,
- vysoká teplota vyrobeného plynu s obsahem alkalických kovů ve formě páry,
- nevyhořelý uhlík,
- složitější provoz v důsledku kontroly přívodu media a paliva,
- spotřeba energie pro kompresi plynu.
4.6. Reaktor se stacionární fluidní vrstvou (BFB – bubbling fluidises bed)
Reaktor se stacionární fluidní vrstvou je dobře znám a využívá se pro své dobré vlastnosti. Stacionární vrstva má viditelné rozhraní mezi vrstvou a prostorem nad vrstvou (fluidní vrstva má viditelnou hladinu. Obsah dehtu v plynu se pohybuje kolem 1–2 %.
4.7. Reaktor s cirkulující fluidní vrstvou (CFB – circulating fluidised bed)
Tento typ reaktoru nemá zřetelnou hladinu vrstvy, vrstva je ohraničena stropem reaktoru. Vrstva má rozdílnou hustotu ve svislém směru, u dna reaktoru je nevyšší a u stropu nejnižší. Unášené částice jsou zachycovány v cyklonu a vráceny zpět do spodní části fluidní vrstvy. Díky této funkci je vyšší využití paliva a množství zreagovaného uhlíku je mnohem větší než u reaktoru BFB.
4.8. Reaktor s unášivým proudem
Technologie používá jemně rozemleté palivo, které je foukáno velkou rychlostí zplyňovacím mediem do reaktoru, kde se zplyňuje při teplotách 1200–2000 °C. Při takto vysokých teplotách se popel taví a ve formě strusky odtéká z reaktoru. Palivo se přivádí v suché formě (ve směsi s dusíkem) nebo mokré formě (uhelný kal v kašovité formě). Velkou výhodou této výroby plynu je velmi nízký obsah dehtů.
Poděkování
Tato publikace (práce, článek) byla vypracována v rámci projektu „Inovace pro efektivitu a životní prostředí – Growth“, identifikační kód LO1403 za finanční podpory MŠMT v rámci programu NPU I.
Literatura
- [1] Zplyňování biomasy: VŠB-TUO, Výzkumné energetické centrum, Ostrava, 2014, ISBN 978-80-248-3302-6
- [2] KLASS D. L.: Biomass for renewable energy fuels and chemicals, Academis Press, USA, 1998
- [3] GRØNLI M.: Theoretical and experimental study of the thermal degratation of biomass. Doctoral Thesis, NTNU, Trodheim, Norway, 1996
- [4] KNOEF H. A. M.: Handbook biomass gasification. BTG biomass technology group BV, Nehterlands, 2005
- [5] VAN SWAAIJ W. P. M., VAN DEN AARSEN F. G., BRIDGEWATER A. B., HEESINK A. B. M.: Review of Biomass Gasification, A Report to the European Communiti DGXII Joule Programme, April 1994
- [6] KUBÍČEK J.: Vlastnosti biopaliv ve vztahu k jejich spalování a zplyňování, seminář Energie z biomasy, VUT Brno 2003
- [7] ALAUDDIN Z. A. B. Z., LAHIJANI P., MOHAMMADI M., MOHAMED A. R.: Gasification of lignocellulosic biomass in fluidized beds for renewable energy development: A review, Renewable and Sustainable Energy Reviews, Vol. 14, Issue 9, 2010
- [8] HOFBAUER H.: Biomass gasification – a promising rout efor tha future, 16th International Congress of Chemical and Process Engineering, CHISA 2004, I5.1 (1207) 22–26 August 2004, Prague, Czech Republic
Article is dealing with gasification principles and gasifiers. Gasification is process for gas producing from solid fuels (coal, wastes, biomass). Producer gas can be used in cogeneration unit (piston engine or combustion turbine) for generating of heat and electricity with higher efficiency in comparison with combustion in boiler. All processes in gasifier taking place with regulated supply of gasification media (air, oxygen or steam) and reaction heat.