Výzkumná zplyňovací technologie s autotermním generátorem
Článek seznamuje čtenáře se stručnou historií zplyňování a zplyňovacích zařízení umístěných v prostorách Výzkumného energetického centra na Vysoké škole báňské – Technické univerzitě Ostrava. Zplyňování má na Výzkumném energetickém centru již desetiletou tradici. Počátky se datují do roku 2006, kdy byla zahájena spolupráce s ostravskou firmou TEMEX, spol. s r.o. na výstavbě první verze zplyňovacího zařízení s autotermním generátorem.
Hlavní částí technologie byl zplyňovací generátor s pevným ložem a maximálním tepelným výkonem 100 kW. Doprava paliva ze zásobníku do reaktoru byla zajišťována vodorovným šnekem, který ústil pod rošt. Následně bylo palivo pomocí pravoúhlého kolena směrováno do vrstvy nad pevný rošt (viz Obr. 1.).
Za zplynovačem byly dva cyklony pro odloučení tuhých znečišťujících látek (TZL) a dva vodní chladiče pro chlazení vyrobeného plynu. Následně byl umístěn ventilátor, který zabezpečoval v předchozích aparátech mírný podtlak. Tím bylo zajištěno nasávání zplyňovacího média (vzduchu) do vrstvy paliva v generátoru. Posledním technologickým prvkem byla dopalovací komora, v níž byl vyrobený plyn spálen. Schéma technologie je na Obr. 2.
Na Obr. 3. je pohled na technologii z druhé strany (vlevo je před zásobníkem paliva umístěn elektrický rozváděč).
Vstupním palivem byla dřevní štěpka, složení vyrobeného plynu je v Tab. 1.
Tab. 1. Složení plynu
z dřevní štěpky
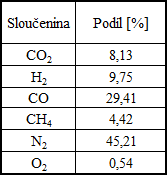
Nejpodstatnější úpravou reaktoru zplyňovací technologie v roce 2008 byla změna dopravy paliva, která zasáhla zejména spodní část reaktoru. Došlo k náhradě jednoho šnekového dopravníku dvěma. První vedl ze zásobníku paliva do spodní části generátoru do prostoru popelníku, od něhož byl oddělen ocelovou příčkou. Druhý šnek byl svislý a dopravoval palivo od konce prvního šneku nad rošt, jehož středem procházel (viz Obr. 4.). Zároveň byla vyměněna vyzdívka reaktoru.
Během následujících let byly do zplyňovací technologie včleňovány další aparáty, které řešily zejména zvýšení kvality plynu (odstranění nežádoucích látek).
Jako první byl sestrojen a testován dolomitový reaktor (viz Obr. 5.). Tento nahradil druhý cyklon a pracoval při teplotách 850 až 900 °C. Při nich dochází ke katalytickému rozkladu organických sloučenin tvořících dehty. Výhodou oproti ostatním katalyzátorům je nízká citlivost na přítomnost sloučenin síry a halogenů v čištěném plynu. Výsledná účinnost odstraňování dehtů byla po několika testech stanovena na 96,6 %, přičemž vstupní koncentrace dehtů do reaktoru se pohybovala kolem 2 900 mg/mN3 a výstupní kolem 100 mg/mN3. Při provozu zařízení byl vnitřní prostor elektricky otápěn. Dolomit byl průběžně odváděn a doplňován novým.
V roce 2011 byl na zplyňovací technologii testován vysokoteplotní odlučovač tuhých znečišťujících látek (horký filtr) viz Obr. 6. Aparát byl umístěn do technologie místo obou cyklonů i dolomitového reaktoru. Filtr odstraňuje pevné částice z vyráběného plynu suchou metodou pomocí filtračních svíček vyrobených z keramických vláken. Pro bezproblémový provoz filtru je nejdůležitější udržovat teplotu v aparátu vyšší než 450 °C, aby dehtovité látky obsažené v plynu zůstaly v plynném stavu a prošly filtračními svíčkami. Při nižších teplotách existuje riziko kondenzace dehtů na filtračních elementech a jejich destrukce.
Nádoba vlastního odlučovače je rozdělena na dvě části pomocí přepážky s otvory, ve kterých jsou upevněny filtrační elementy. Nad touto přepážkou vzniká tzv. čistý prostor, kde se nachází plyn zbavený tuhých znečišťujících látek. Pod přepážkou je tzv. nečistý prostor, v němž se nachází znečištěný plyn. Ten vstupuje do filtru tangenciálně do dolní třetiny odlučovače. Následně prochází přes filtrační elementy do čistého prostoru, z něhož odchází do dalších aparátů technologie. Během odlučování částic vzniká na vnějším povrchu filtračních elementů filtrační koláč. Ten je nutno pravidelně odstraňovat, neboť zvyšuje tlakovou ztrátu a postupně snižuje průtok plynu. K odstraňování odloučených částic z filtračních svíček slouží pulse-jet systém, tedy proplach znečištěných filtračních elementů tlakovým rázem ze shora (z čistého prostoru). Pro stlačování regeneračního média (vyčištěný plyn) je využíván kompresor na CNG. Odloučené částice následně padají vlivem gravitace do dolní části nádoby, z níž jsou odstraňovány během odstávek zařízení.
Vyrobený plyn na vstupu do odlučovače obsahoval přibližně 4170 mg/mN3 tuhých znečišťujících částic, koncentrace TZL na výstupu z odlučovače byla nižší než 25 mg/mN3, z čehož vyplývá účinnost odlučování vyšší než 99,4 %.
Tomuto typu odlučovače byl v roce 2015 udělen užitný vzor č. 28954.
Zplyňovacímu generátoru byl udělen národní patent č. 304091 v r. 2013.
V průběhu provozu popisované technologie bylo provedeno přibližně 70 testů v trvání od 10 do 12 hodin. Náročnost testů se významně projevila na stavu vnitřních částí generátoru. Zejména testování pelet z agromateriálů, které se díky nízkým teplotám tavitelnosti (nižším než teploty zplyňovací) natavily na vnitřní část vyzdívky a bylo je nutno mechanicky odstranit. Z tohoto důvodu bylo přistoupeno k zatím poslední úpravě, která byla provedena v roce 2016. Jednalo se o výrobu nové vnitřní vyzdívky reaktoru a úpravě spodní části reaktoru. Technický stav vyzdívky byl identifikován po rozebrání reaktoru. Porušení je patrno z Obr. 7 a 8.
Úprava reaktoru spočívala v upevnění jeho horní části na tři nosníky opírající se o zem. Dolní část byla doplněna o konstrukci se zvedáky a kolečky a uložena na kolejnice. Také zásobník paliva s vodorovným dopravníkem paliva je uložen na kolejnicích, které umožňují po demontáži spojovacích šroubů na přírubě jeho odvoz mimo dolní část reaktoru. Poté je možno povolit dělící přírubu na generátoru a pomocí čtyř mechanických zvedáků oddělit dolní část generátoru od horní. Kolejnice umožňují dolní část vysunout mimo horní. Díky tomu je možno provádět servisní zásahy nebo čištění výrazně snadněji (viz Obr. 9.). Vyměněna byla též celá elektroinstalace, trubní připojení k dalším aparátům, vnitřní vyzdívka reaktoru a byl osazen nový oscilační rošt.
Pohyblivý rošt (viz Obr. 10.) byl navržen tak, aby umožnil pohyb ve dvou osách. Ve vodorovné ose osciluje pomocí táhel a pohonu. Současně se pohybuje horizontálně. Tímto je zajištěno, že případné spékající se popeloviny z paliva budou snáze propadávat roštem a následně budou z generátoru vynášeny šnekovým vynašečem (viz Obr. 11.). Úprava umožní testovat paliva, která vykazují problematické vlastnosti v generátorech s pevným ložem. Roštu byl udělen užitný vzor č. 29866.
Po dokončení úprav (viz Obr. 12.) byla technologie nejprve podrobena několika studeným testům funkčnosti jednotlivých částí včetně řízení a ovládání. Následně byl proveden ověřovací zplyňovací test, kde palivem byly dřevěné pelety, a zplyňovacím mediem byl vzduch. Test probíhal při teplotách 750, 870 a 950 °C. V tabulce 2 je uveden příklad složení plynu při 750 °C s výhřevností 4,47 MJ/mN3.
Tab. 2. Složení
vyrobeného plynu
při testu
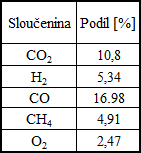
Shrnutí
Technologie byla navržena a vyrobena s cílem umožnit provádění zplyňovacích testů v kontinuálním provozu a takovém rozsahu, abychom byli schopni je správně kvantitativně charakterizovat. Velikost jednotky umožňuje na jedné straně provádět odběry dostatečných množství vzorků pro analýzy nezbytných parametrů (kvalita plynu, množství nečistot) při přijatelné spotřebě paliva a stabilitě procesu. Výhodou je také možnost včleňovat či měnit jednotlivé aparáty technologie tak, aby bylo možno ověřit jejich funkčnost, účinnost a spolehlivost v kontinuálním provozu. Od doby výstavby byla otestována řada technických řešení různých problémů spojených se zplyňovacím procesem.
Poděkování
Tato publikace byla vypracována v rámci projektu „Inovace pro efektivitu a životní prostředí – Growth“, identifikační kód LO1403 za finanční podpory MŠMT v rámci programu NPU I.
Literatura
- Zplyňování biomasy: VŠB-TUO, Výzkumné energetické centrum, Ostrava, 2014, ISBN 978-80-248-3302-6
- CHŁOND, Rafał Adam. Zvyšování výhřevnosti a kvality plynu ze zplyňování biomasy: disertační práce. Ostrava: VŠB-TUO, Fakulta strojní, 2012. Vedoucí disertační práce prof. Ing. Pavel Noskievič, CSc.
- NAJSER, Jan. Zplyňování dřeva pro kogeneraci: disertační práce. Ostrava: VŠB – TUO, Fakulta strojní, 2008. Vedoucí disertační práce prof. Ing. Pavel Noskievič, CSc.
- Výzkumné zprávy. VŠB-TU Ostrava, Výzkumné energetické centrum
The article introduces a brief history of gasification and gasification equipment located at the premises of Energy Research Center at VSB - Technical University of Ostrava. Gasification at the Energy Research Center has a ten-year tradition. The beginnings date back to 2006, when cooperation was initiated with the Ostrava company TEMEX, spol. s.r.o. by the construction of the first version of the gasifier with autothermal generator.