Heating pumps in Environmental Building of the Year after 10 years
Using heat pumps for cooling technology and industrial waste heat recovery
Historical industrial buildings are heated and supplied with hot water. Heat pump, accumulation vessels and adiabatic cooling was used throughout the reconstruction. Special attention was paid to noise emissions due to the immediate neighbourhood of residential buildings.
The decision regarding the modernization and expansion of the manufacturing compound of HVM Plasma in Prague district of Jinonice was made in 2007. The project was completed in 2009 and in 2010 the compound was declared the Czech Energy and Environmental Building of the Year by the Ministry of Industry and Commerce of the Czech Republic. It means this year the installed equipment, managing the energy flow within the compound, celebrates the 10 anniversary.
The HVM Plasma compound includes two administrative and production facilities. The older one is a refurbished former building of Tresoria, company established in 1879, which manufactured vaults and other safety elements. Its traditional design with barrel roof was maintained during the refurbishment. In essence, this building is the only witness of the former worldwide fame of the engineering production in the Walter compound in Jinonice. The second building was built as new and is connected with the original building. The HVM Plasma Company applies special thin coats on metallic parts and components (e.g. for automotive industry). In this regard the Company operates one of the largest production capacities in Central Europe and the results are incorporated in millions of engine injection units and even space satellites.
The coating technology, i.e. the application of thin coats, uses vacuum and high temperatures. The coating and the vacuum production has large heat surplus, which needs to be removed. At the same time the interior areas must be heated for a large part of the year and the hot water supply is required throughout the year. The compound refurbishment project dealt with it using heat pumps, accumulation vessels and adiabatic cooling. The adiabatic cooling, reducing the demand on the fans capacity, allowed to meet the basic requirement to increase the immitted noise situation in the vicinity of the apartment and residential buildings.
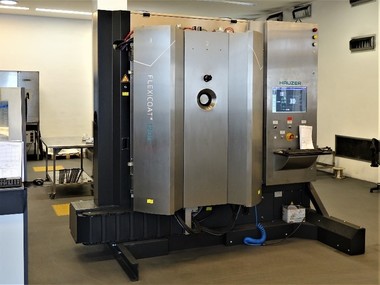
The HWM Plasma production facility is located in Jinonice district of Prague and its line of business continues in the excellent worldwide reputation of Czech engineering of the former Walter factory. The residential buildings in the vicinity required a great attention to the noise emissions. (View across the railroad tracks, Prague Simmering, Jinonice station)
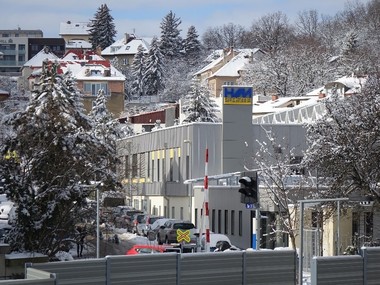
One of several coating devices, reliable operation of which relies on the operation of a set of Master Therm heat pumps
Project description
The foundation of the heat management is the vacuum coating equipment, cooled by circulating water with 400kW thermal energy potential. The cold, or thermal energy with low temperature, is produced in a set of water-water heat pumps. The heat with higher temperature, taken from the internal cooling cycle of the heat pump, is, if possible, used to heat the building, provide hot water and, if no other use is found, it is disposed of in the adiabatic cooling tower. The cooling side of the heat pumps is used to produce the cold for all devices, which form especially the production vacuum coating equipment, ventilation units and air-condition units (fan coils) in the rooms. The cold is distributed through the water circulation. The production technology cooling operates with a temperature gradient 20/30°C.
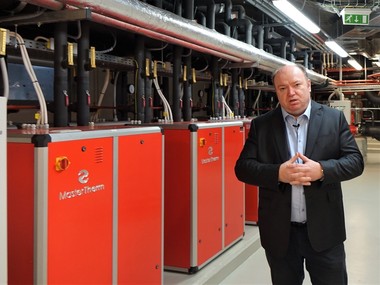
Our cooperation with HVM Plasma was not finished after the supply of heat pumps. We are in touch and we guarantee its operation. We are pleased to say, that in the 10 years of operation we needn’t replace virtually anything,” says Ing. Jiří Svoboda, the general manager of Master Therm tepelná čerpadla s.r.o., the manufacturer and supplier of heat pumps.
The disposal of unused energy gains from the circuit takes place in the adiabatic cooling towers by removing heat into the surrounding air. The reduction of noise pollution of the surroundings is based on the fact, that the tower allows cooling in the free cooling mode by spraying the input cooling air with water and additional cooling of the heat-bearing substance to the wet-bulb temperature to the temperature of the ambient air = 23.4°C, i.e. at least for 2/3 of the year. Most of the water used for spraying comes from a large-volume tank, used for precipitation water. Due to the need of year-round operation the tower has dedicated circuit with anti-freeze liquid. For cooling outside the free cooling period the heat pumps operate in the temperature gradient of the cooling water 34/20°C.
Heat pumps are installed in the cooling machine room for the cooling mode 14/8° C as well, which is required for the operation of the air-condition equipment.
All heat pumps on the condenser side are connected to the stratification tank with three basic temperature ranges, which operates concurrently as a hydraulic separator as well. The condensers of the heat pumps operate in the same mode 35/45°C. In case of heating they operate with temperature gradient 45/55°C.
Heat pumps
The modification of parameters of the thermal energy for cooling or the heat for heating is provided by a set of 8 heat pumps with constant output and one with modulated output. The heat pumps are connected so, for a certain time, in case of outage even of several pumps the capacity can be provided by the remaining pumps, e.g. by reducing heating, to preserve the production. “Since we use standard design elements, including compressors, we can provide the Operator with a guarantee of a very swift repair. However, in the 10 years of operation we needn’t have to replace virtually anything,” says Ing. Jiří Svoboda, the general manager of Master Therm tepelná čerpadla s.r.o. (the manufacturer and supplier of heat pumps).
The Czech manufacturer Master Therm collaborated on the project from its initial design stage. In total 8 AQ 180.2Z type units were installed with total cooling capacity of 660kW. These are twin-compressor heat pumps water-water, fitted with the electronic expansion valve (EEV) and fully hermetically sealed scroll compressor. In order to ensure precise cold production for air-condition the set is fitted with a AQ 90 Inverter heat pump with variable speed of the compressor and cooling capacity of 50kW.
The selection of the Master Therm products was decided by the capacity to tailor them for a specific application, with optional optimization of the efficiency of the equipment in a specified temperature mode, by intervention into the control algorithm of the expansion valve or by modification of the evaporator connection. These facts had a substantial impact on the overall high efficiency of the cold production. At the same time the heat pumps utilize standard components, i.e. components with attractive price on the market, which are readily available in case its replacement is needed. This fact is key for the stability of the production, because fault removal on a specialized cooling machine would require even weeks of outage and production interruption.
Basic project parameters
Building cooling output max. | 370 kW |
Technology cooling output max. | 490 kW |
Rated input power of the cooling and air condition | 430 kW |
Calculated heat loss | 80 kW |
Estimate of energy consumption for heating and hot water production | 100 MWh/rok |
Estimate of annual consumption of energy for the operation of technology and lighting | 700 MWh/rok |
Estimate of energy consumption for cold production for technology and building | 550 MWh/rok |
Overall cold consumption for technology and building cooling | 3 530 MWh/rok |
Overall annual average efficiency of cold production | 6,4 |
Calculated energy savings
Energy savings are generated the the following main factors: | |
use of state-of-the-art of cooling aggregates with optimized function | 240 MWh/rok |
use of adiabatic tower with free cooling and frequency control | 480 MWh/rok |
recovery of technology heat for heating and hot water production | 220 MWh/rok |
Project repeating
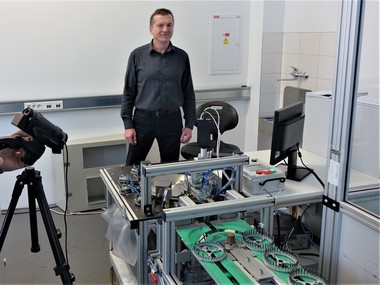
Fig. Having certain automated work stations designed and manufactured externally would require a lot of time and money. So we designed it from modular components produced industrially for automation ourselves, said Ing. Jiří Vyskočil, CSc., the general manager of HVM PLASMA, spol. s r.o. This means insertion of hundreds of thousands of engine injection semi-finished needles into holders per year, where it will be plasma-coated by a highly resistant metallic layer.
Ing. Jiří Vyskočil, CSc., general manager of HVM PLASMA, spol. s r.o., i.e. the investor and operator at the same time, is very satisfied with the reliability of operation and energy efficiency of the set of heat pumps. The designed cold production and heat management system with connection to the production technology proved in the last 10 years excellent reliability and economical parameters. Ing. Vyskočil in not only an excellent manager, but also an engineer. He works in the industry for thirty years. HVM PLASMA purchase the first Swiss coating equipment Hauser app. thirty years ago. They very quickly realized, that the purchased equipment can be improved. So they started to improve based on their production experience and the know-how is a significant part of the design for other customers as well. Knowledge-based and strictly technical approach shows in the energy management concept. The proof of the quality and economical success of the selected solution is the intention of the company to use the concept again in its coating facility in Brno.
According to Ing. Petar Srbljanovič, specialized designer of industrial applications, SF Engineers Consulting, the success is primarily based on PWM Plasma requirement for a system with excellent technical parameters, while taking long-term cost of energy and regular maintenance, speed and the possibility to solve eventual emergencies into account. And also the fact, that all interested parties collaborated from the beginning with common interest. Work for a customer, who is not only an investor, but also the future operator, gave him great satisfaction, because he was able to apply the best technical solution from the perspective of long.term operation, including automatic balancing fittings for regulation of the flow of heat-bearing substances.
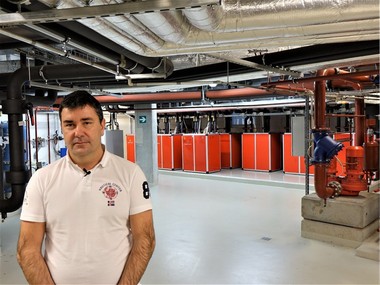
The project of the heat energy flow, modification of its parameters by heat pumps, heating, cooling, air replacement, hot water production etc. was prepared by Ing. Petar Srbljanovič, SF Engineers Consulting.
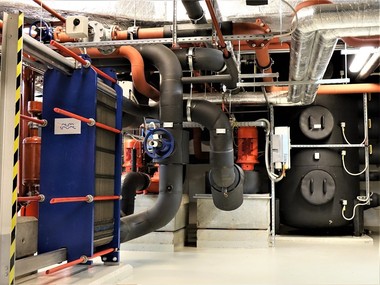
On the left, assembled plate heat exchanger separates the circuit of water bearing the excess heat and the water.anti-freeze mixture, which leads to the adiabatic cooling tower. On the right, the large-volume accumulation vessel is clearly shown, with 3 distinctly different temperature layers. The maintenance of temperature stratification is supported by horizontal separators, which allow the vessel to fulfil the function of the equalizer of dynamic pressures (HVDT, anchor ring).
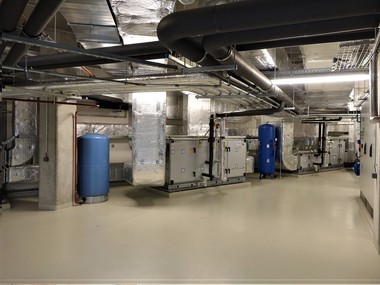
Fig. Master Therm heat pumps are the source of cold for the air.condition, providing the air replacement in the entire compound and the maintenance of comfortable temperature. Some production technologies require even super-clean work environment.
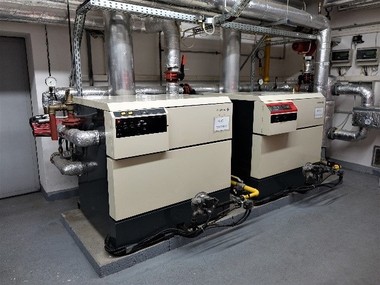
Hot water production requires higher output temperature from the heat pump. Therefore it is solved by a separate Master Therm heat pump, also water-water type with primary source of heat from the cooling of production technologies. Hot water is produced in two accumulation vessels (not shown)
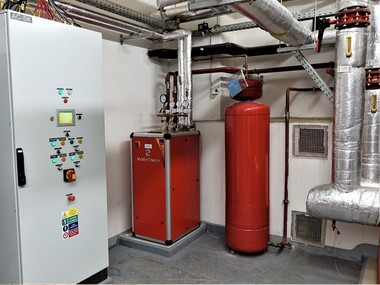
The gas-burning boilers, originally used for heating and hot water production, became, regardless of their excellent condition, only a fixed back-up.
Conclusion
The presentation of the recognized technical projects after its commissioning is a welcome support to generate the interest of the public. When the project can be presented after ten years of operation and we can declare, that the promised goals were met, it is a clear sign of the project’s success and that the recognition is earned. The project is significant in the perspective of the current goal of the Czech Republic to reduce the energy demand by more than 30% until 2030. Especially, since, as the operator’s representative declared, it will be most likely repeated not only to support the energy efficiency of HVM Plasma, but also to meet the Czech Republic’s commitment.
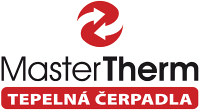
Master Therm je český výrobce tepelných čerpadel vzduch-voda, země-voda, voda-voda s certifikací EHPA a registrací pro dotace. Tepelná čerpadla s tradicí od roku 1994 pro rodinné i bytové domy a průmyslové objekty všech velikostí. Výroba, projekt, ...