Interval technické diagnostiky při měření čerpadel
Spolehlivá dodávka médií je závislá na provozuschopném výrobním zařízení, které je ovlivněno správně a včas prováděnou údržbou včetně kontroly provozních parametrů. Ke kontrole provozních parametrů lze využít vibrodiagnostiku, tribodiagnostiku, termodiagnostiku, metody nedestruktivní defektoskopie a další. V příspěvku je uvedena možnost stanovení pružného intervalu technické diagnostiky aplikované na vibrodiagnostiku čerpadel. Tímto způsobem lze docílit ekonomických úspor, proti údržbám prováděných v pevně plánovaných termínech.
1. Úvod
Poruchy a jimi vyvolaná přerušení provozu strojů jsou působeny celou řadou vnějších a vnitřních vlivů a procesů, které působí a probíhají přímo ve strojích. Tyto vlivy mají za následek změny vlastností strojních součástí. Tyto změny jsou prvotními technickými příčinami poruch. Souhrn těchto procesů se nazývá mechanismus poruch. Podle různé kombinace faktorů, které mají vliv na poškozování funkčních ploch, se rozlišují tyty kategorie: opotřebení, koroze, otlačení, deformace, trhliny a lomy, ostatní poškození. [4]
Snahou technické diagnostiky je tato poškození funkčních ploch nalézt, identifikovat a predikovat dobu životnosti součásti nebo strojního celku [8]. K tomu slouží technické diagnostice řada metod, které mohou být založeny na vyhodnocování teploty objektu (termodiagnostika), na vyhodnocování chvění a hluku objektu (vibrodiagnostika) [2] nebo na rozboru vzorku oleje (tribodiagnostika) [1, 7].
Neméně důležité je také odhalovat skryté trhliny, které se v materiálu součástí mohou šířit a mohou tak být příčinou zvýšené teploty nebo chvění stroje. Každopádně existence trhliny má vliv také na těsnost i mechanickou pevnost součásti. K odhalení trhliny slouží celá řada metod, přičemž jsou preferovány metody nedestruktivní defektoskopie [3, 6]. Mezi nejznámější a nejužívanější metody nedestruktivní defektoskopie patří magnetická metoda prášková (zachycení prášku na trhlině zmagnetizované součásti) [15, 16, 17, 18, 19, 20], kapilární metoda (vzlínání vhodného penetrantu do trhliny) [9, 10, 11, 12, 13, 14] a ultrazvuková metoda (využívá k odhalení trhliny mechanické vlnění) [21, 22, 23].
Aby bylo možné včas odhalit začínající poruchu nebo výrazné opotřebení funkčních ploch je potřeba nastavit správný interval prováděných diagnostických měření [5]. Tento interval by měl respektovat naměřenou hodnotu zvoleného parametru a při jeho zhoršování interval vhodně zkracovat tak, aby nedošlo k havarijní poruše, ale současně bylo co nejvíce využito životnosti součásti.
Příspěvek popisuje možnost stanovení intervalu měření a výsledky aplikuje na vibrodiagnostické měření čerpadel v nepřetržitém provozu. Počáteční interval měření byl 30 dní a v závislosti na měřených hodnotách klesl až na 5 dní, kdy byla provedena údržba.
2. Metodika měření
V systému řízení diagnostiky nebyla dosud stanovena zásadní pravidla pro stanovení intervalu měření. Během celé dosavadní praxe v oblasti technické diagnostiky nebyla v této oblasti nalezena podpora v existujících publikacích a odpověď na otázku „jak stanovit interval měření“ nebyla detailně zodpovězena ani na odborné konferenci. Proto je v počátcích práce s diagnostickým systémem kladen důraz na stanovení intervalu měření pro provádění periodického sběru dat, který doposud převažuje nad on-line diagnostickými systémy u sekundárních výrobních technologií a technologií s paralelním zajištěním.
Návrh definice výpočtu intervalu měření vychází z předpokladu, že výpočet musí kopírovat vývoj měřené veličiny a dynamicky reagovat na změny v trendu vývoje poškození. Před samotnou formulací výpočtu je nutné zdůraznit některé zásadní skutečnosti.
- Na základě obecně přijímaných postupů byl pro interval měření volen řád dnů a to především s ohledem na praktické provedení měření a jeho plánování v rámci pracovního týdne, kdy provedení s denním předstihem nebo zpožděním nehraje v naprosté většině případů zásadní roli.
- Před provedením výpočtu je nutné zvolit „faktor dynamiky“ α. Což je parametr rychlosti změny intervalu, počet předchozích intervalů ze kterých se vypočítává interval následující. Čím je vyšší, tím ten výpočet reaguje pomaleji, protože bere v úvahu více předchozích měření. Faktor dynamiky tak určuje s jakou citlivostí bude samotný výpočet kopírovat změny měřené veličiny a zároveň je základem pro definování počtu referenčních měření n.
- Při stanovení intervalu mezi referenčními měřeními se dále vychází z předpokladu, že normami a směrnicemi definované referenční hodnoty poruchových signálů určují stupeň poškození zařízení a způsob dalšího provozu a tím i do jisté míry časový horizont případného servisního zásahu.
Výpočet délky n-tého intervalu mezi měřeními INTn je dán součtem předchozího intervalu INTn−1 a redukčního faktoru toho intervalu RINT. Výpočet je obecný a uvedenou jednotku xy lze nahradit jakoukoliv jednotkou měřené provozní veličiny stroje.

- INTn
- n-tý interval mezi měřeními [den]
- INTn−1
- předchozí interval [den]
- RINT
- redukční faktor intervalu [den]
Redukční faktor RINT je doba, o kterou se původní interval prodlouží nebo zkrátí v souvislosti s vývojem měřené veličiny a je dán rovnicí:
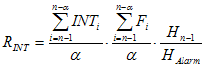
- RINT
- redukční faktor intervalu [den]
- INTi
- i-tý interval mezi měřeními [den]
- FINT
- velikost faktoru změny měřené veličiny mezi intervaly [-]
- α
- faktor dynamiky [-]
- Hn−1
- předchozí hodnota měřené veličiny [xy]
- HAlarm
- alarmní hodnota měřené veličiny [xy]
Faktor změny Fi je podíl změny mezi příslušnými měřeními ΔH a intervalem mezi příslušnými měřeními INT.
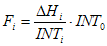
- Fi
- faktor změny i-tého intervalu [-]
- ΔH
- změna mezi příslušnými měřeními [-]
- INTi
- i-tý interval mezi měřeními [den]
- INT0
- počáteční interval diagnostických měření [den]
Hodnota podílu změny mezi měřeními ΔHn je potom:
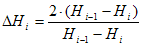
- ΔHi
- změna mezi měřeními [-]
- Hi−1
- poslední měřená hodnota [xy]
- Hi
- aktuální hodnota měřené veličiny [xy]
n-tý interval měření je po dosazení dán vztahem:
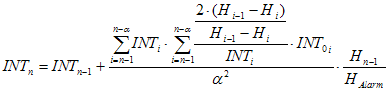
- INTn
- hledaný interval [den]
- INTi‧
- interval mezi příslušnými měřeními [den]
- INTn−1
- předchozí interval [den]
- Hi−1
- poslední měřená hodnota [xy]
- Hi
- aktuální hodnota měřené veličiny [xy]
3. Výsledky měření
Pro ověření zda je model výpočtu dynamického intervalu měření využitelný v technické praxi a lze na jeho základě účinně řídit a plánovat zásah údržby, byla vybrána technologie s dostatečnou historií provozu a údržby. Jedná se o 5 čerpadel se 3 paralelními zálohami v nepřetržitém provozu (obr. č. 1), která jsou sledována pomocí vibrodiagnostiky. Čerpadla mají doporučenou dobu provozu do generální opravy 25 000 motohodin.
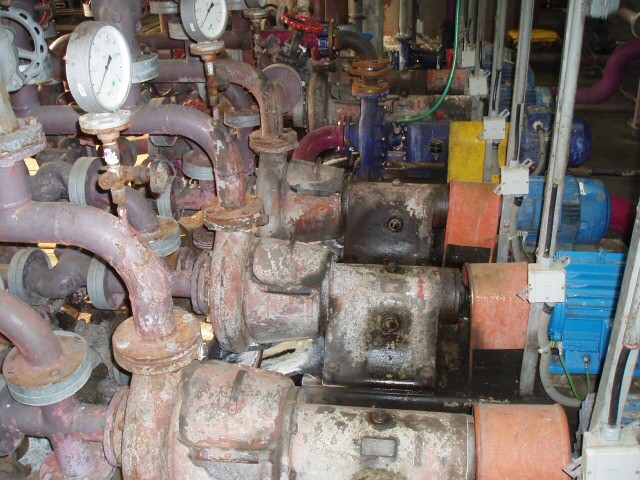
Obr. č. 1 – čerpadla
Na základě skutečnosti, že již všechna čerpadla v době nasazení této metody stanovení intervalu měření byla po uvedené době repasována, referenční interval měření byl zvolen na 30 dní s faktorem dynamiky α = 3.
Stanovení referenčního intervalu:
- První 3 referenční měření prokázala, že dochází jen k minimálním změnám v celkové hodnotě rychlosti vibrací ve všech měřených rovinách. Naměřené hodnoty se pohybovaly nad hranicí 1. alarmu dle ČSN ISO 10 816-3 a od termínu poslední repase uběhlo u každého stroje jen několik týdnů. Do následující repase zbývalo v době nasazení metody cca 14 000 motohodin, což představuje ½ životnosti. Pro získání relevantního vzorku dat je potřeba provést minimálně 10 měření plus takový počet měření, ve kterém bude prostor na reakci diagnostiky. Interval 30 dní tedy představuje cca 20 měření do ukončení životnosti strojů. Takový vzorek je dostatečný pro provedení analýz a predikce.
- Důležitou skutečností pro stanovení intervalu v délce 30 dní byla i skutečnost, že dodací termín pro ložiska byla v tomto případě ½ této doby, tedy 14 dní, což je předpokládaná hranice zkrácení měřícího intervalu, kdy se již musí uvažovat o servisním zásahu.
- Faktor dynamiky α = 3 představuje minimum pro dané podmínky. Pokud by se jednalo o technologii v záběhu, nebo těsně po repasi, uvažované α, by bylo 10 % z předpokládaného počtu měření do další repase (v tomto případě 6).
Měření s dynamickým intervalem bylo prováděno ve 4 měřících rovinách. 2 měřící roviny na motoru a 2 na ložiskovém kozlíku čerpadla. Na obr. č. 2 je znázorněn průběh měřené veličiny [mm/s] v úloze celkových vibrací a vývoj délky měřícího intervalu nastaveného na výše uvedené parametry u jednoho z uvedené skupiny strojů.
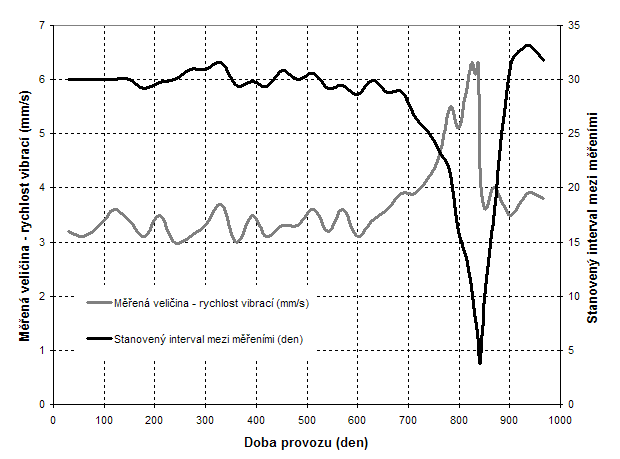
Obr. č. 2 – vývoj měřené veličiny a intervalu měření v závislosti na době provozu
Data byla zpracována na základě zápisu měření do tabulky (tabulka č. 1), která obsahuje v jednotlivých buňkách příslušné výpočty a po dosazení měřené hodnoty je vypočítán následný interval měření. Šedě označené pole označuje původní plánovaný termín a šedě oznančené pole s tučným písmem skutečný termín repase (generální opravy).
Číslo měření | H – měřená hodnota [xy] | INT – interval měření [den] | ΔH – změna hodnot [-] | F – faktor změny [-] | RINT – redukční faktor času [den] |
---|---|---|---|---|---|
1 | 3,2 | 30,00 | |||
2 | 3,1 | 30,00 | 0,03 | 0,03 | |
3 | 3,3 | 30,00 | −0,06 | −0,06 | |
4 | 3,6 | 30,00 | −0,09 | −0,09 | −1,15 |
5 | 3,4 | 30,00 | 0,06 | 0,06 | −0,85 |
6 | 3,1 | 29,15 | 0,09 | 0,09 | 0,54 |
7 | 3,5 | 29,69 | −0,12 | −0,12 | 0,28 |
8 | 3,0 | 29,97 | 0,15 | 0,15 | 1,01 |
9 | 3,1 | 30,98 | −0,03 | −0,03 | 0,00 |
10 | 3,3 | 30,98 | −0,06 | −0,06 | 0,56 |
11 | 3,7 | 31,54 | −0,11 | −0,11 | −2,09 |
12 | 3,0 | 29,45 | 0,21 | 0,21 | 0,36 |
13 | 3,5 | 29,82 | −0,15 | −0,15 | −0,48 |
14 | 3,1 | 29,33 | 0,12 | 0,12 | 1,50 |
15 | 3,3 | 30,83 | −0,06 | −0,06 | −0,82 |
16 | 3,3 | 30,02 | 0,00 | 0,00 | 0,56 |
17 | 3,6 | 30,58 | −0,09 | −0,09 | −1,44 |
18 | 3,2 | 29,14 | 0,12 | 0,12 | 0,31 |
19 | 3,6 | 29,45 | −0,12 | −0,12 | −0,81 |
20 | 3,1 | 28,64 | 0,15 | 0,16 | 1,28 |
21 | 3,4 | 29,92 | −0,09 | −0,09 | −0,50 |
22 | 3,6 | 28,85 | −0,06 | −0,06 | 0,04 |
23 | 3,9 | 28,90 | −0,08 | −0,08 | −2,41 |
24 | 3,9 | 26,48 | 0,00 | 0,00 | −1,41 |
25 | 4,2 | 25,08 | −0,07 | −0,09 | −1,74 |
26 | 4,6 | 23,34 | −0,09 | −0,12 | −2,13 |
27 | 5,5 | 21,21 | −0,18 | −0,25 | −5,26 |
28 | 5,1 | 15,95 | 0,08 | 0,14 | −2,10 |
29 | 5,7 | 13,84 | −0,11 | −0,24 | −3,06 |
30 | 6,3 | 10,78 | −0,10 | −0,28 | −2,89 |
31 | 6,1 | 7,89 | 0,03 | 0,12 | −2,36 |
32 | 6,3 | 5,53 | −0,03 | −0,18 | −1,51 |
33 | 4,1 | 4,01 | 0,42 | 3,16 | 6,67 |
34 | 3,6 | 10,69 | 0,13 | 0,36 | 7,33 |
35 | 4,0 | 18,02 | −0,11 | −0,18 | 13,17 |
36 | 3,5 | 31,19 | 0,13 | 0,13 | 2,00 |
37 | 3,9 | 33,19 | −0,11 | −0,10 | −1,40 |
4. Závěr
Zásadním poznatkem z uvedených výsledků, je skutečnost, že v režimu dynamického intervalu bylo provedeno pouze o 4 měření více, než kdyby byla měření prováděna v pravidelných intervalech. Z toho právě poslední 4 měření (29.–32.) před odstavením stroje byla provedena v rozmezí 31 dnů, což by za normálních okolností odpovídalo jednomu intervalu měření. Na druhou stranu je potřeba v režimu pravidelného intervalu ověřovat skokovou změnu měřené veličiny, zda se nejedná o chybu měření. Tím je rozdíl v počtu měření smazáván a v praxi je obvykle roven počtu měření v režimu dynamického intervalu.
Pro posouzení relevantnosti měření v trendu, musí být k dispozici 3 nebo více měření, na základě nichž lze vyřadit měření jako chybové nebo ho považovat za standardní. V takovém případě by se měření v pravidelném intervalu odpovídající časově 26. měření v dynamickém intervalu muselo opakovat pro ověření správnosti a vyloučení možnosti chyby měření. Pokud by opravné měření ukázalo, že se o chybu měření nejedná, následovalo by jako další logický krok zkrácení intervalu dle zvážení diagnostika (obecně asi na ½ intervalu). Proces by se opakoval, až do překročení únosné hodnoty. V uvedeném případě bylo v kritické fázi provozu v oblasti prudkého nárůstu měřené veličiny provedeno v dynamickém intervalu 7 měření v rozmezí 12 týdnů oproti 4 měřením, která by odpovídala pravidelnému intervalu (tabulka č. 2) a min. 3 ověřovacím měření. Diagnostik tak dostal přesnější informace o chování stroje nejen v celkových hodnotách, ale také pro analýzy spekter, tedy tam kde sledoval konkrétní poruchu způsobující zvýšení celkových hodnot trendu.
měření | datum měření v dynamickém intervalu (DI) | datum měření v pravidelném intervalu (PI) | měřená hodnota v DI (H) |
---|---|---|---|
26 | 8.3.2008 | 2.3.2008 | 4,6 |
27 | 1.4.2008 | 1.4.2008 | 5,5 |
28 | 22.4.2008 | 5,1 | |
29 | 8.5.2008 | 1.5.2008 | 5,7 |
30 | 22.5.2008 | 6,3 | |
31 | 1.6.2008 | 6,1 | |
32 | 9.6.2008 | 31.5.2008 | 6,3 |
Výsledky u ostatních strojů, na kterých byl testován systém výpočtu dynamického intervalu, jsou analogické k uvedenému příkladu a z praktického hlediska zcela naplnily očekávání přesnějšího určení času odstavení v kritické fázi provozu.
Oproti všeobecně užívanému systému provádění pravidelných měření v řádu týdnů je u této metody výpočtu nezbytně nutné zajistit stoprocentní technický support pro pracovníka provádějícího měření. Vysoké nároky jsou kladeny zejména na důsledné dodržování měřicího intervalu, kdy je sestaven kalendář měření. Technik, který provádí jednotlivé analýzy a pracuje s dynamickým intervalem měření vždy označí do kalendáře den, kdy se má následující měření provést. Pracovník provádějící měření pak provede měření na základě tohoto kalendáře.
Zavedením této metody se zásadně změnil postoj k přípravě a provedení potřebného servisního zásahu. Všechna čerpadla byla odstavována do údržby nejen ve správný čas, ale v době kdy již všichni pracovníci údržby provádějící servisní zásah dopředu byli informováni o rozsahu poškození. Tímto způsobem nebylo nezbytné na servisní zásah čerpat přesčasové hodiny a především byly náhradní díly objednány „just in time“, žádný díl nebyl ve skladě déle než 1 týden.
Vychází-li se z předpokladu, že počet měření v režimu dynamického intervalu je shodný jako u pravidelného intervalu a nasazení této metody v tomto směru „nic nestojí“, zásadní přínos je především v úspoře nákladů na skladované náhradní díly a snížení pravděpodobnosti vzniku vícenákladů spojených s přesčasovými hodinami až o 60 % oproti měření prováděnému v pravidelném intervalu.
Pro jedno čerpadlo to představuje náklady ve výši cca 2 000,–. Ve sledovaném provozu kde se nachází více než 1 500 zařízení, z nichž více než 1/3 je pod dozorem vibrodiagnostiky prováděné v pravidelných intervalech, představuje úspora v případě výpočtu dynamického intervalu 1 000 000,– Kč.
Nesporným přínosem pro údržbu je také fakt, že provedením servisního zásahu s nasazením dynamického intervalu měření, je možné se ještě více přiblížit k reálné době životnosti ložiska a tím využít maximální možný výrobní potenciál zařízení. Tento benefit je o to více ceněn u technologií zaměřených na úspory a efektivní využití energií, kterými jsou moderní tepelná čerpadla a systémy inteligentního řízení budov. Dále pak v průmyslových podnicích, které kladou důraz na optimální systém řízení údržby v souladu s principy TPM, kde má technická diagnostika a údržba řízená na základě provozního stavu zařízení své nezastupitelné místo. A v neposlední řadě také ve společnostech využívajících nejmodernější technologie, jejichž životnost má významný podíl na ekonomických výsledcích.
5. Poděkování
V souvislosti se vznikem tohoto článku, bych rád poděkoval především kolegům diagnostikům Jiřímu Horákovi a Ing. Tomáši Vackovi, kteří svým pozitivním přístupem zásadně ovlivnili hladký průběh sběru dat a četnými věcnými připomínkami napomohli dotvořit konečnou podobu výpočtu až do fáze provozní použitelnosti.
Příspěvek byl vytvořen s grantovou podporou projektu ČZU 31190/1312/3128 (Česká zemědělská univerzita v Praze) – „Vliv biopaliva na úplné charakteristiky motoru“.
Literatura
- [1] Aleš, Z., Pexa, M., 2010: Diagnostika maziv s využitím laserového analyzátoru LASERNET FINES®-C, Časopis – Strojírenská technologie, Ročník XIV, zvláštní vydání, Univerzita Jana Evangelisty Purkyně, FVTM, Ústí nad labem, 2010, s. 8-11. ISSN 1211-4162
- [2] Juzenas, E., Jonušas, R., Juzenas, K., 2008: Defects diagnostics of rolling bearings of low speed machines, VIBROENGINEERING 2008 - Proceedings of 7th International Conference 2008, s. 59-62.
- [3] Li G, Huang P, Chen P, Hou D, Zhang G, Zhou Z. Quantitative nondestructive estimation of deep defects in conductive structures. Časopis - International Journal of Applied Electromagnetics and Mechanics, Ročník 33, Číslo 3-4, 2010, s. 1273-1278. ISSN 1383-5416
- [4] Pošta, J.: Provozuschopnost strojů. Česká zemědělská univerzita v Praze, 2. vydání, Praha, 2006. ISBN 80-213-0966-0
- [5] Savic, B.M., Jovanovic, V: Determining the optima interval for the technical diagnostics of bearings. Proceedings – ASME international manufacturing science and engineering conference, s. 41-46, 2009. ISBN 978-0-7918-4362-8
- [6] Shah AA, Ribakov Y. Non-destructive evaluation of concrete in damaged and undamaged states. Časopis - Materials and Design. 2009;Ročník 30, číslo 9, 2009,s. 3504-3511. ISSN: 0261-3069
- [7] Stodola J, Stodola P. Mechanical system wear and degradation process modelling. Časopis – Transactions of Famena. Ročník 34, číslo 4, 2010, s19-32. ISSN: 1333-1124
- [8] Žižka, J., Linhart, T., 2009: Určování stavu opotřebení soustružnického nože pomocí poměru složek řezné síly, Časopis - Strojírenská technologie, Ročník XIV, číslo 1, Univerzita Jana Evangelisty Purkyně, FVTM, Ústí nad labem, 2010, s. 23-28. ISSN 1211-4162
- [9] ČSN EN 571-1 01 5017. Nedestruktivní zkoušení – Kapilární zkouška – Část 1: Obecné zásady. Praha: Český normalizační institut, 1998.
- [10] ČSN EN ISO 3452-2 01 5018. Nedestruktivní zkoušení – Zkoušení kapilární metodou – Část 2: Zkoušení kapilárních prostředků. Praha: Český normalizační institut, 2007.
- [11] ČSN EN ISO 3452-3 01 5018. Nedestruktivní zkoušení – Kapilární zkouška – Část 3: Kontrolní měrky. Praha: Český normalizační institut, 1999.
- [12] ČSN EN ISO 3452-4 01 5019. Nedestruktivní zkoušení – Kapilární zkouška – Část 4: Vybavení. Praha: Český normalizační institut, 1999.
- [13] ČSN EN 473 01 5004. Nedestruktivní zkoušení – Kvalifikace a certifikace pracovníků NDT – Všeobecné zásady. Praha: Úřad pro technickou normalizaci, metrologii a státní zkušebnictví, 2009.
- [14] ČSN EN 1289 05 1176. Nedestruktivní zkoušení svarů – Zkoušení svarů kapilární metodou – Stupně přípustnosti. Praha: Český normalizační institut, 1999.
- [15] ČSN EN ISO 9934-1. Nedestruktivní zkoušení – Zkoušení magnetickou metodou práškovou – Část 1: Všeobecné zásady. Praha: Český normalizační úřad, 2002.
- [16] ČSN EN ISO 9934-2. Nedestruktivní zkoušení – Zkoušení magnetickou metodou práškovou – Část 2: Zkušební prostředky. Praha: Český normalizační úřad, 2003.
- [17] ČSN EN ISO 9934-3. Nedestruktivní zkoušení – Zkoušení magnetickou metodou práškovou – Část 3: Přístroje. Praha: Český normalizační úřad, 2003.
- [18] ČSN EN ISO 3059. Nedestruktivní zkoušení – Zkoušení kapilární a magnetickou práškovou metodou – Podmínky prohlížení. Praha: Český normalizační úřad, 2002.
- [19] ČSN EN 1290. Nedestruktivní zkoušení svarů – Zkoušení svarů magnetickou metodou práškovou. Praha: Český normalizační úřad, 2000.
- [20] ČSN EN 1291. Zkoušení svarů magnetickou metodou práškovou – Stupně přípustnosti. Praha: Český normalizační úřad, 2000.
- [21] ČSN EN 1714. Nedestruktivní zkoušení svarů – Zkoušení svarových spojů ultrazvukem. Praha: Český normalizační úřad, 1999.
- [22] ČSN EN 1712. Nedestruktivní zkoušení svarů – Zkoušení svarových spojů ultrazvukem - Stupně přípustnosti. Praha: Český normalizační úřad, 1999.
- [23] ČSN EN ISO 23279. Nedestruktivní zkoušení svarů – Zkoušení ultrazvukem – Posouzení charakteru indikací ve svarech. Praha: Český normalizační úřad, 2010.
Zaměření článku: Cílem článku je vytyčit nové možnosti při stanovení intervalu údržby a měření provozních parametrů strojů. V provozu je prováděna řada měření (vibrodiagnostika, tribodiagnostika, tennodiagnostika atd.), kdy je třeba vhodně řídit diagnostický interval tak, aby technická diagnostika objektu odrážela jeho skutečný technický stav, ale současně aby nebyla prováděna v příliš krátkých intervalech, a tím zvyšovala náklady diagnostických měření. V článku navržená metodika stanovení délky intervalů je univerzální a lze ji využít v rámci všech diagnostických metod. Závěr: Článek odpovídá po odborné, jazykové i stylistické stránce obvyklým normám a doporučuji jej k publikování v odborném tisku.
Recenzent:
Ing. Dian, Ph.D.
Univerzita Jana Evangelisty Purkyně
v Ústí nad Labem
Quality product is dependent on reliable and serviceable manufacturing facility, which is influenced by effective and timely performed maintenance. In order to check the operating parameters it is possible to use vibrodiagnostics, tribodiagnostics, termodiagnostics, non-destructive testing methods and others. It's difficult to choose the right moment to implement maintenance inspection in order to exploit the whole equipment life time and reduced risk of breakdown failure. The fundamental rules for determining the maintenance measurement interval in the diagnostic management system has not been established. Therefore, the emphasis is on determining the interval for measuring of the implementation of periodic data collection, which is more often used than the on-line diagnostic systems for secondary production techniques and technologies with a parallel backup. Proposal for a definition of the calculation of interval measurement is based on the assumption that the calculation must reproduce the behavior of the measured variables and dynamically respond to changes in the trend of damage. Technology has been chosen with a sufficient history of operations and maintenance, to check whether the model of the calculation of the dynamic range of measurement is usable in engineering practice and if it is sufficient enough be to manage and plan the maintenance action. To verify the model five pumps with three parallel backups were used. A major finding from these results is the fact that under the dynamic interval only four more measurements were made than if the measurements were carried out at regular intervals. Just the last four measurements before the outage was made within 31 days, which would normally correspond to one measurement interval. On the other hand, it is necessary under the regular intervals to verify the step change of measured values. This difference in the number of measurements compensated in practice is usually equal to the number of measurements in dynamic mode interval. If based on the premise that the number of measurements under the dynamic range is the same as at regular intervals and use this method in this direction "zero cost" essential contribution is primarily the cost savings on storage of spare parts and reduce the likelihood of other costs with overtime up to 60% compared with measurements carried out at regular intervals. Undeniable contribution to maintenance is also a fact that by making a service action with the deployment of dynamic range measurements, it can even closer determine real life time of bearing and it is possible to use of the maximum potential production of equipment.