Vliv různých abrazivních materiálů na povrch skla
Sklo jako součást stavby se na moderních i historických budovách vyskytuje v různých formách, ať už jako výplň otvorů nebo jako aplikace na povrchu stavby. Jeho přítomnost je proto nutné zohlednit při sanačních zásazích. Mechanické metody čištění skla, konkrétně pomocí abrazivních materiálů, nejsou v restaurátorské praxi příliš běžné. Přesto byly využity při posledním zásahu na mozaice Posledního soudu na katedrále Sv. Víta v Praze. V příspěvku je diskutováno, zda je vhodné opakovaně používat techniku otryskávání povrchu skla za účelem jeho čištění/odstranění korozních vrstev z povrchu skla.
1. Úvod
Praktická aplikace skel ve stavební konstrukci vyžaduje znalost chování skla v pevném stavu a za podmínek využívání stavby [1]. Mezi základní vlastnosti skla patří tvrdost, pevnost a chemická odolnost.S poslední zmiňovanou vlastností souvisí vznik korozních vrstev. U historických skel se často vyskytuje, a to jak korozní dealkalizovaná vrstva skla (na bázi gelu SiO2), tak vrstva vzniklá sekundárně precipitací korozních produktů (často se jedná o sírany a uhličitany) [2]. Zásadním faktorem ovlivňujícím stupeň poškození a proces koroze je chemické složení skla. Tloušťka korozních vrstev však může záviset jak na složení skla, tak na jeho stáří a intenzitě vlivů okolního prostředí [3, 4].
Čištění povrchu skla je nevratný sanační proces. Cílem čištění je obvykle odstranění vrstvy korozních produktů se současným zachováním dealkalizované vrstvy skla. Metody čištění mohou být rozděleny do tří skupin, a to na metody na bázi rozpouštědel, chemické metody a mechanické metody, kam patří mimo jiné i abrazivní čištění. Primární znalostí pro úspěšnou sanaci je znalost chemické povahy a struktury korozních produktů/nánosů, které mají být odstraněny [5, 6]. Důležité je si uvědomit, že čištění znamená odstranění usazenin a korozních vrstev tak, aby byl zachován původní materiál a nedošlo k jeho poškození [5].
V experimentální studii, která je předmětem tohoto článku, byla sledována kvalita povrchu skla po aplikaci mechanického čištění při použití různých abrazivních materiálů. Nerovnoměrně ošetřený povrch totiž může činit problém při nanášení ochranných laků, které mají za úkol chránit mozaiku Posledního soudu umístěnou na Zlaté bráně na katedrále Sv. Víta v Praze před poškozením a korozí.
2. Experimentální část
Abraziva
Pro otryskávání byly použity dva typy materiálu. Prvním typem bylo abrazivum, tzv. crushed glass (dále také jako CG s rozměrem 64 µm a 115 µm), neboli drcené sklo (dodavatel Crystal Mark, Inc.) [7] a druhým typem abraziva byla balotina (dále také jako BAL s rozměrem částic do 50 µm, 70–110 µm a 200–300 µm) od firmy Krampe Harex [8]. Na základě analýzy rentgenové fluorescenční analýzy (dále také jako XRF) lze všechna abraziva hodnotit jako sodno-vápenatá skla s obsahem SiO2 70 hm. % bez výraznějších rozdílů ve složení.
Vzorky skla
Byly testovány dva typy skel – (a) skla, která se používají dnes pro výrobu vitráží, lišící se stářím (A, B) a (b) laboratorně utavená skla (C, D). Skla C a D byla utavena cíleně podle zjištěného složení skla z mozaiky Posledního soudu na katedrále Svatého Víta. Složení testovaných skel je uvedeno v Tab. 1.
Použité vzorky skla | ||||
---|---|---|---|---|
Typ A | Typ B | Typ C | Typ D | |
SiO2 | 67,21 | 68,57 | 20,36 | 42,91 |
Na2O | 17,53 | 15,73 | – | 1,51 |
CaO | 12,63 | 10,03 | 0,61 | 23,66 |
MgO | 0,96 | 3,78 | 0,86 | 2,23 |
SO3 | 0,79 | 1,03 | – | – |
Al2O3 | 0,55 | 0,41 | 3,82 | 1,54 |
K2O | 0,09 | 0,25 | 0,17 | 25,62 |
Fe2O3 | 0,07 | 0,11 | 0,11 | 0,04 |
Cl | 0,05 | 0,02 | – | – |
TiO2 | 0,04 | 0,02 | 0,02 | 0,04 |
As2O3 | 0,03 | 0,02 | 0,05 | – |
P2O5 | 0,01 | 0,01 | 0,31 | 0,92 |
PbO | – | – | 72,78 | 1,21 |
CuO | – | – | 0,57 | – |
ZnO | – | – | 0,24 | 0,21 |
Otryskávání vzorků skla a zjišťování úbytků hmotnosti
Vzorky skel o velikosti 3×3 cm byly otryskávány po dobu 30 a 60 sekund pod tlakem 269 kPa. Od každého typu skla byly tryskány vždy 3 vzorky jedním abrazivním materiálem o určité velikosti. Po provedení otryskávání následovalo mechanické očištění a odmaštění acetonem, vážení a výpočet hmotnostního úbytku jednotlivých vzorků.
Optická mikroskopie a skenovací elektronová mikroskopie (dále jako SEM)
Vzorky skla i abrazivní materiály byly zdokumentovány optickým mikroskopem Olympus BX51. Pro studium morfologie povrchu byl použit skenovací elektronový mikroskop Hitachi S-4700.
Měření drsnosti povrchu vzorků a mikrotvrdosti
Drsnost byla měřena na přístroji Hommel tester T1000. Měřená dráha činila 1,8 mm a byla měřena střední aritmetická odchylka drsnosti (Ra) a největší hloubka drsnosti (Rt). Byly proměřeny pouze vzorky, které byly tryskány po dobu 60 sekund z důvodu rovnoměrnějšího otryskání povrchu skla.
Mikrotvrdost byla měřena na metalografickém světelném mikroskopu Carl Zeiss Neophot 2 se zatížením 100 g. Vzorky skla byly následně snímány pomocí SEM při použití přístroje Hitachi S-4700 a byly odečteny délky úhlopříček vrypů, podle nichž byla stanovena tvrdost jednotlivých vzorků.
3. Výsledky a diskuse
Otryskávání a hmotnostní úbytky
Úbytky hmotnosti vzorků po otryskávání vzrůstaly dle očekávání s délkou otryskávání. Je-li brán v potaz typ abrazivního materiálu, patří vyšší úbytky hmotnosti abrazivnímu materiálu crushed glass. Jsou-li porovnávána jednotlivá abraziva zvlášť, pak v případě crushed glass dochází k největším hmotnostním úbytkům při otryskávání průměrnou velikostí částic 115 µm po dobu 60 s (max. 0,69 %) a v případě abrazivního materiálu balotiny náleží největší hmotnostní úbytky vzorkům skla otryskaným balotinou o velikosti částic 200–300 µm po dobu 60 s (max. 0,66 %).
S ohledem na výsledky otryskávání skel typu A a B byla modelová skla otryskávána pouze pomocí crushed glass o průměrné velikosti částic 64 µm po dobu šedesáti sekund (obdobný typ materiálu byl použit i na mozaice Posledního soudu). U skel typu A a B došlo v porovnání se skly C a D k několikanásobně nižším úbytkům hmotnosti, přičemž nejmenší hmotnostní úbytky byly pozorovány u skla typu B. Průměrné úbytky hmotnosti laboratorně utavených skel jsou zaznamenány níže v tabulce (Tab. 2).
Průměrný úbytek hmotnosti [%] | Srovnání oproti typu A | Srovnání oproti typu B | |
---|---|---|---|
C/olovnaté | 5,09 | 24× více | 61× více |
D/draselno-vápenaté | 1,99 | 9× více | 24× více |
Důvodem několikanásobně vyšších úbytků hmotnosti u laboratorně utavených skel je jejich výrazně odlišné chemické složení a s tím související tvrdost skla. Data tabulky výše (Tab. 2) dobře korespondují s výsledky uvedenými v Tab. 3, kdy nejnižší hodnota mikrotvrdosti podle Vickerse byla stanovena u olovnatého skla (Tab. 3, vzorek C), u kterého byl stanoven současně nejvyšší úbytek hmotnosti během otryskávání (Tab. 2). Obdobný problém může nastat u vzorků historického skla, které má často odlišné složení než dnešní skla, resp. použitý abrazivní materiál na bázi skla.
Optická mikroskopie a SEM
Z důvodů porovnání kvality otryskávání byl nejprve pořízen snímek vzorku skla před otryskem (Obr. 1). Ze snímku (Obr. 1) je patrné, že povrch skla před otryskáním byl hladký, bez výrazných nerovností. Po otryskání došlo ke zdrsnění původně hladkého povrchu všech skel.
Morfologie povrchu otryskaných vzorků závisela pouze na použitém abrazivu, vliv odlišného složení skla nebyl zaznamenán. Velikost částic v případě abraziva crushed glass neměla téměř žádný vliv na rovnoměrnost otryskaného povrchu. V případě balotiny pak s rostoucí velikostí částic použitého abraziva došlo ke zvýšení nerovnoměrnosti otryskaného povrchu (Obr. 2).
Obrázek 2 Příklad povrchu skla po otryskání abrazivem typu crushed glass (do 64 µm). Sklo typu A (a). Příklad povrchu skla po otryskání balotinou (200–300 µm). Sklo typu A (b)
Při použití balotiny bylo na některých místech zřetelně viditelné poškození skla do hloubky. Důvodem, proč bylo u materiálu crushed glass dosaženo rovnoměrnějšího otryskání než v případě použití balotiny, je zřejmě tvar částic abrazivního materiálu. V případě crushed glass se jednalo o drť skla a částice se mohly dostat lépe do kontaktu s povrchem vzorku a odstranit tak i více hmoty materiálu. Na základě těchto poznatků lze říci, že jako vhodnější otryskávací materiál se jeví abrazivo Crushed glass. Tento materiál o velikosti částic 64 µm byl pak použit pro oba typy modelových skel.
Na snímcích ze skenovací elektronové mikroskopie bylo možné u všech otryskaných skel velmi dobře rozeznat praskliny v povrchu vzorků (Obr. 3). Nelze tedy vyloučit, že při použití této techniky při čištění historického skla nebudou na povrchu skla vznikat nové praskliny. Vzniklé praskliny zvětšují povrch skla a vytváří místa, kde může docházet k intenzivnějšímu působení okolního prostředí (problém kondenzace vlhkosti a vysychání hůře dostupných míst). V neposlední řadě může členitost povrchu také komplikovat ošetření povrchu skla ochrannými přípravky.
Měření drsnosti
Nejprve bylo pro srovnání provedeno měření neotryskaných vzorků skel typu A (Rt = 1,607 ± 0,202 µm) i B (Rt = 1,044 ± 0,402 µm).
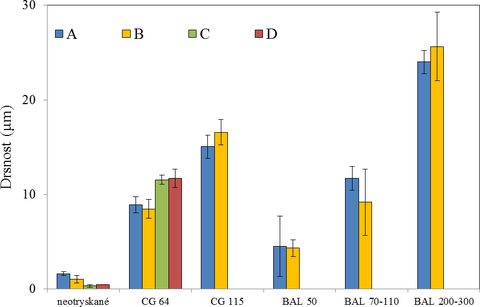
Obrázek 4 Drsnost skla (parametr Rt) po otryskání abrazivy po dobu 60 sekund. A – sodno-vápenaté, cca 60 let staré sklo, B – novodobé sodno-vápenaté, C – olovnaté a D – draselno-vápenaté sklo.
Výsledky měření drsnosti skel po otryskání jsou zaznamenány v grafu (Obr. 4). Z měření je zřejmé, že po otryskání se hodnoty Rt výrazně zvýšily, a to po použití všech typů abraziv. Hodnoty Rt vzrůstaly s velikostí částic abraziva. Při srovnání drsnosti povrchů po otryskání abrazivy o přibližně stejné velikosti částic, tzn. například Crushed glass 64 µm a balotinou do 50 µm, byly vyšší hodnoty studovaných parametrů pozorovány vždy u vzorků skla otryskaných pomocí Crushed glass. Tento fakt opět přisuzujeme tvaru částic tohoto abrazivního materiálu. Měření drsnosti povrchu bylo rovněž provedeno u skla C a D. Hodnoty Rt byly vyšší než u skel typu A a B.
Z grafu (Obr. 4) je patrné, že nejdrsnějším povrchem se vyznačovala skla typu A a B po otryskání balotinou o největší velikosti částic (200–300 µm). Zároveň je však také z hodnoty směrodatné odchylky patrné, že povrch nevykazoval stejnou drsnost po celém svém povrchu, a to z toho důvodu, že byl povrch otryskán nerovnoměrně.
Měření mikrotvrdosti
K výpočtu mikrotvrdosti podle Vickerse [9] je zapotřebí změření délky úhlopříčky vtisku. U skla typu A byla průměrná délka úhlopříčky přibližně 12,5 µm a u skla typu B měly úhlopříčky průměrnou délku asi 12 µm. Průměrná délka úhlopříčky vtisku u skla C činila přibližně 25 µm, zatímco u skla D dosahovala průměrná délka úhlopříčky jen cca 15 µm. Rozdíl v délce úhlopříček jednotlivých laboratorně utavených skel byl téměř dvojnásobný, což poukazuje na to, že draselno-vápenaté sklo (D) je tvrdší, než sklo olovnaté (C), a proto do něj hrot jehlanu při vtiskování nepronikl tak hluboko.
Jako sklo s nejvyšší tvrdostí podle Vickerse (Tab. 3) bylo vyhodnoceno sklo s označením B (HV100 = 128,75). Naopak, jako sklo s nejnižší tvrdostí (HV100 = 29,66) bylo stanoveno sklo C – olovnaté sklo. Nižší hodnota HV100 byla způsobena celkovým složením tohoto skla.
A | B | C | D | |
---|---|---|---|---|
HV100 | 118,66 | 128,75 | 29,66 | 82,40 |
Využití databáze SciGlass 6.7 pro hodnocení mikrotvrdosti skel
Tvrdost abrazivních materiálů byla hodnocena i na základě informací z databáze SciGlass 6.7 [10], ze které byly dohledány vzorky s podobným chemickým složením jako abrazivní materiály použité v této práci. Na základě informací z databáze SciGlass 6.7 bylo možné odhadnout tvrdost abrazivních materiálů na 5 GPa. Obdobné hodnoty lze předpokládat i u skla typu B (na základě srovnání chemického složení) a zřejmě i u skla A. Na základě těchto dat a výsledků z měření mikrotvrdosti usuzujeme, že použitá abraziva vykazují vyšší tvrdost než tryskaný materiál (vzorek C) a nelze je tak použít.
4. Závěr
Příspěvek byl zaměřen na testování vhodnosti použití různých abrazivních materiálů za účelem odstranění korozních produktů a očištění povrchu skla – skleněných mozaikových kostiček z období středověku, konkrétně 2. poloviny 14. století. Bylo zjištěno, že všechny používané abrazivní materiály povrch skla narušují. Korozní produkty sice mohou být tímto způsobem odstraněny, ovšem nelze spolehlivě zaručit, že nedojde i k úbytku hmoty samotného skla, popř. korozních/křemičitých vrstev, což je nežádoucí efekt této technologie.
Z výsledků měření mikrotvrdosti a porovnáním údajů z databáze SciGlass 6.7 je patrné, že všechny abrazivní materiály použité v této práci vykazují vyšší tvrdost než modelová skla, což způsobuje vysoké úbytky hmotnosti materiálu. Jak je obecně známo z literatury [6, 11], měl by vždy abrazivní materiál vykazovat nižší tvrdost než otryskávaný materiál. Při pravidelném otryskávání za účelem odstranění korozních produktů by takto sanovaný historicky cenný materiál pravděpodobně neustále ubýval. Všechny abrazivní materiály použité v této práci se tudíž jeví jako spíše nevhodné pro odstraňování korozních produktů z historických či archeologických skel.
Alternativou k abrazivním materiálům používaným v této práci by mohlo být využití suchého ledu či laseru pro odstraňování korozních produktů z historických skel. To je však podmíněno důkladnými zkouškami, neboť zde hrozí nebezpečí popraskání materiálu v důsledku teplotního šoku.
Poděkování
Práce vznikla v rámci projektu MK DF12P01OVV017 a s použitím prostředků VŠCHT Praha.
5. Literatura
- Matoušek, J. Anorganické nekovové materiály; Praha: VŠCHT Praha, 1992.
- Jurek, K.; Peřina, V. Příčiny koroze mozaiky „Poslední soud“ na chrámu Sv. Víta v Praze. Historické sklo. 2003, vol. 1, no. 5, p. 111–116.
- Bräutigam, U.; Bürger, H.; Völksch, G. Investigations into structure and composition of gel layers on medieval window glasses of the Katharinenkirche, Oppenheim (Germany), and the Cathedral St. Gatien, Tours (France). Glastech. Ber. Glass Sci. Technol. 1995, vol. 1, p. 29–33.
- Carmona, N.; Villegas, M. A.; Fernández Navarro, J. M. Study of glasses with grisailles from historic stained glass windows of the cathedral of Leo´n (Spain). Applied Surface Science. 2006, p. 5936–5945.
- Abd-Allah, R. Chemical cleaning of soiled deposits and encrustations on archaeological glass: A diagnostic and practical study. Journal of Cultural Heritage. 2013, no. 4, p. 97–108.
- Benešová, J.; et al. Konzervování a restaurování kovů. Ochrana předmětů kulturního dědictví z kovů a jejich slitin. Brno: Technické muzeum v Brně, 2011.
- http://www.crystalmarkinc.com/
- http://www.krampeharex.com/
- Fanderlik, I. Vlastnosti skel; Praha: Informatorium, 1996.
- http://www.sciglass.info/
- Gibson, B. M. The Use of the Airbrasive Process for Cleaning Ethnological Materials. Studies in Conservation. 1969, vol. 14, p. 155–164.
Glass as part of the building, modern and historic buildings as well, can be found in various forms, either as gaps fillings or as surface applications. Therefore, the presence of glass should be taken into account during remedial interventions. Mechanical methods of glass cleaning, specifically abrasive method are not very common in restoration work. Nevertheless, this method was used during the last intervention on the Last Judgement mosaic, the part of the St. Vitus Cathedral in Prague. The paper discusses pertinence of reusing of sandblasting technology for cleaning/removal of corrosion layers from the glass surface.