Zjišťování účinnosti teplovodních kotlů na pevná paliva podle vyhlášky č. 194/2013 Sb.
Stanovení účinnosti teplovodních kotlů na tuhá paliva podle stávající legislativy může být problematické. Na praktickém příkladu autor dokládá, že i velmi moderní a podle tabulkových hodnot velmi úsporný kotel může mít během provozu nižší než očekávanou účinnost. Vysvětlení je uvedeno v článku.
Úvod
Povinnost provádět pravidelné kontroly účinnosti tzv. „nelicencovaných“ kotlů od jmenovitého výkonu 20 kW energetickými specialisty je zavedena vyhláškou č. 194/2013 Sb. (dále jen vyhláška) [1]. Povinnost se nevztahuje na rodinné domy, byty a stavby pro rodinnou rekreaci. Velké „licencované“ zdroje si naopak mohou kontrolovat sami provozovatelé. Obecně je vžitá představa, že pevná paliva využívají především fyzické osoby k vytápění domácností nebo velká licencovaná energetická zařízení. Diskuze k provádění kontrol energetickými specialisty se tedy vedou především o kontrolách plynových kotlů či kotlů na topné oleje. U těchto zdrojů lze s jistou mírou tolerance říci, že k objektivnímu provedení kontroly účinnosti zdroje stačí změření komínové ztráty běžným analyzátorem spalin.
Ve skutečnosti jsou teplovodními kotli na pevná paliva vytápěny také desetitisíce drobných obchodů, penzionů a jiných provozoven, které je nutné ze zákona rovněž kontrolovat. Pokud má být kontrola provedena zcela v souladu s vyhláškou, narazíme na zásadní problém, kterým je její proveditelnost. Protože zvláště u moderních zdrojů se vliv komínové ztráty na jeho celkovou účinnost podstatně snižuje a zjištění ostatních ztrát je bez složitých laboratorních rozborů prakticky nemožné.
Problém použití normy ČSN 07 0305
Podle vyhlášky se při stanovení účinnosti kotlů vychází z měření a za podmínek určených v ČSN 07 0305 [2]. A zde nastává problém. Zmíněná norma byla vydána již v roce 1983, tedy v době, kdy byla kondenzační technika tzv. „v plenkách“ (to platí především pro plynná paliva) a teplota spalin zvláště u kotlů menších výkonů běžně vysoce překračovala 200 °C, takže rozhodující ztrátou byla ztráta citelným teplem spalin (komínová). V neposlední řadě tato norma prakticky „nezná“ pevná biopaliva, která se za posledních 20 let zvláště u kotlů menších výkonů značně rozšířila. Zásadní problém představuje skutečnost, že norma byla vypracována (a tudíž je platná) pouze pro horkovodní a parní kotle, tedy podstatně odlišné technologie oproti technologiím využívaným u teplovodních kotlů na pevná paliva. Obecná pravidla pro stanovení jednotlivých ztrát jsou sice pro všechny technologie shodná, ale rozdílné jsou faktory, které ovlivňují velikost těchto ztrát. Normu tedy nelze u teplovodních kotlů použít v případě, že je měřením stanovena komínová ztráta a ostatní ztráty se stanoví výpočtem s použitím tabulek z přílohové části. V praxi je v drtivé většině případů měřitelná pouze komínová ztráta.
Teplovodní kotle na pevná paliva jsou kotli menších výkonů. Požadavky na konstrukci, bezpečnostní výbavu a zkušební metody pro kotle o jmenovitém výkonu do 500 kW určuje ČSN EN 303-5 [3]. Pro teplovodní a nízkotlaké parní kotle pak platí norma ČSN 07 0240 [4], která byla do zavedení [3] platná také pro kotle do výkonu 500 kW. Oproti její evropské „kolegyni“ je v ní velice precizně zpracována teorie určování kotlových ztrát, proto se budu v následujícím textu na tuto normu několikrát odvolávat.
Účinnost těchto kotlů ovlivňuje způsob, jakým je řízen spalovací proces, a hlavně jak je řízen přísun spalovacího vzduchu a paliva do ohniště. Rychlost rozvoje technologií spalování pevných paliv v malých teplovodních kotlích se zvyšovala úměrně s rychlostí zvyšování ceny energií a od roku 2012 také se zásadním navýšením legislativních požadavků na čistotu a efektivitu přeměny energií z pevných paliv na teplo. Prudký rozvoj nových technologií znamenal mimo jiné také změnu vlivu jednotlivých kotlových ztrát na celkovou účinnost zdroje.
U starých technologií s ruční dodávkou paliva a přirozeným přívodem spalovacího vzduchu, řízeným především komínovým tahem, probíhalo spalování za značného kolísání přebytku spalovacího vzduchu a s teplotami spalin běžně na hranici 300 °C. Rozhodující složkou celkových ztrát pak byla ztráta citelným teplem spalin, která se z 80 až 90 % podílela na celkové ztrátě. Nucený přívod spalovacího vzduchu elektronicky řízeným ventilátorem znamená snížení a stabilizaci jeho přebytku. To ve spojení s faktem, že se teplota spalin i při jmenovitém výkonu přiblížila k hranici 100 °C, přispělo k tomu, že se značně snížila komínová ztráta a její podíl na ztrátě celkové.
Samočinná dodávka paliva stabilizuje spalovací proces a má zásadní vliv na podstatné snížení emisí. V případě špatně seřízeného dávkování paliva do ohniště se však stává, že nově dodávané palivo z roštu vytlačuje palivo ještě nedokonale vyhořelé, což vede naopak ke zvýšenému podílu mechanického nedopalu na celkových ztrátách.
Moderní kotle se samočinnou dodávkou paliva musí být schopny provozu v rozsahu 30 až 100 % svého jmenovitého výkonu. Jak se dozvíme dále, velikost výkonu má vliv i na poměrné zastoupení jednotlivých ztrát na ztrátách celkových. Tj. celková účinnost může být při sníženém i jmenovitém výkonu podobná, ale mění se vzájemný poměr dílčích ztrát.
Další část textu je věnována analýze jednotlivých ztrát. U každé z popsaných ztrát se pokusím uvést také její typickou hodnotu, což je ale zvláště u malých teplovodních kotlů dosti ošemetné. I u tzv. automatických kotlů je totiž kvalita spalování, a tím i velikost jednotlivých ztrát, do značné míry závislá na množství vnějších faktorů, kvalitou paliva a obsluhy počínaje a funkčností spalinové cesty konče.
Ztráta hořlavinou v tuhých zbytcích
Tzv. ztráta mechanickým nedopalem je dle [4] u pevných paliv přímo úměrná podílu uhlíku v pevných zbytcích spalování, vztažených na jednotku paliva, a nepřímo úměrná příkonu zdroje. Zjišťování nespáleného uhlíku ve škváře, popílku a úletech je složité a lze je provést pouze laboratorně. U malých zdrojů, u kterých může docházet často ke změně provozních režimů a na jejichž provoz má do značné míry vliv obsluha i kvalita paliva, je prakticky nemožné nalézt nějaký jednoduchý algoritmus pro přibližné stanovení této ztráty, jak je tomu u velkých zdrojů dle [2]. Relativně nízké hodnoty této ztráty se vyskytují u kotlů s ručním přikládáním paliva, kde je palivo přiloženo jednorázově a relativně dlouho se drží na roštu před mechanickým proroštováním. Pokud je spalováno kvalitní palivo a kotel je ideálně napojen na akumulaci, lze počítat s velikostí ztráty hořlavinou v tuhých zbytcích na úrovni 2 %.
U kotlů se samočinnou dodávkou paliva je velice důležité seřízení dávkování paliva na rošt, přizpůsobené kvalitě (výhřevnosti) paliva. Zvláště při spalování uhlí v retortových hořácích, kdy nové palivo postupně z roštu vytlačuje nahořelou vrstvu, znamená příliš rychlé dávkování vytlačování ještě ideálně nevyhořelého paliva do popelníku. U dobře seřízeného hořáku především v laboratorních podmínkách zkušebny se mechanický nedopal při spalování uhlí pohybuje v řádech desetin procent. V reálném provozu to vlivem špatného seřízení dávkování může být 4 až 6 %.
U peletových kotlů má fatální vliv na mechanický nedopal špatné seřízení ventilátoru a dávkování paliva, kdy se velice často stává, že velký tlak primárního vzduchu vyhazuje nespálené pelety z roštu do popelníku. Signálem, že není něco v pořádku, je popelník přeplněný „zuhelnatělými“ peletami. Paradoxně jsou v takovém režimu měřeny často ideální spaliny, protože hoří prakticky pouze prchavá hořlavina. Ideálně seřízený peletový hořák dosahuje ztráty do 0,5 %, avšak zvláště u vyšších výkonů se může díky výše popsanému problému ztráta navýšit na 4 až 8 %.
Ztráta hořlavinou ve spalinách
Méně problematické je stanovení tzv. plynného nedopalu, tedy ztráty vlivem odvedení nespálené plynné hořlaviny (CO, H2, CH4) spalinami. Indikátorem velikosti plynného nedopalu je při spalování pevných paliv do značné míry hodnota CO ve spalinách, což je běžným analyzátorem spalin měřitelné. Z toho také vyplývá, že čím modernější je zdroj, tím méně významný vliv má tato ztráta na jeho celkovou účinnost. Nízké emise CO (po přepočtu na referenční O2) znamenají kvalitní spalování a tím i nízké emise uhlovodíků. U moderních kotlů s emisemi CO do 1000 mg/m3 nepřekročí ztráta plynným nedopalem zpravidla 0,5 %. Pokud je alespoň přijatelně seřízen primární a sekundární spalovací vzduch u kotlů certifikovaných na třídu 3 (CO do 3000 mg/m3), pak by plynný nedopal neměl překročit 2 %. Pokud emise CO překročí hodnotu 5000 mg/m3, má již plynný nedopal značný vliv na celkovou účinnost. Pro přibližné stanovení ztráty hořlavinou ve spalinách lze v tomto případě orientačně využít přílohu 5 vyhlášky.
Ztráta fyzickým teplem tuhých zbytků po spalování
Ztráta teplem odváděným tuhými zbytky je typickou ztrátou pro kotle velkých výkonů, se kterou normy pro teplovodní kotle [3], [4] neuvažují. Zatímco u kotlů velkých výkonů dochází k odpopelňování plynule, a lze tedy předpokládat ztráty teplem tuhých zbytků v řádech desetin procenta, k odstraňování popele a škváry dochází v malých kotlích jednorázově (mechanicky nebo u moderních kotlů odpopelňovači v cyklech) poté, co popeloviny předaly značnou část tepla kotlovému tělesu a celková výše ztrát by tak neměla přesáhnout desetinu procenta.
Ztráta teplem chladicí vody
Podobně jako u předchozí ztráty je ztráta chladicí vodou typickou ztrátou pro velké zdroje, u kterých musí být některé technologické celky chlazeny vodou. U teplovodních kotlů je v případě potřeby jako chladicí voda použita voda otopná, tedy zde nedochází ke ztrátě, proto ani normy pro teplovodní kotle s touto ztrátou nepočítají.
Ztráta citelným teplem spalin
Ztráta teplem spalin odváděných z kotle byla ještě donedávna u teplovodních kotlů na pevná paliva brána jako ztráta rozhodující o celkové účinnosti zdroje. Je to prakticky jediná ztráta, která je měřitelná přímo u konkrétního zdroje běžným analyzátorem spalin. Ten vypočítává tzv. komínovou ztrátu podle Siegertova vztahu buď podle naměřené hodnoty O2, nebo přepočtené hodnoty CO2 ve spalinách
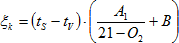
resp.
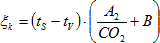
kde je
- ts
- teplota spalin na výstupu z kotle [°C],
- tv
- teplota prostředí (spalovacího vzduchu) [°C],
- O2
- naměřená koncentrace kyslíku ve spalinách [%],
- A1, A2 a B
- konstanty typické pro dané palivo.
Z uvedeného vztahu je zřejmé, že v případě dobře seřízeného přebytku spalovacího vzduchu je pro velikost této ztráty rozhodující teplota spalin. U kotlů starší konstrukce je běžné, že teplota spalin dosahuje v běžném provozu i 300 °C, což podle druhu paliva představuje komínovou ztrátu 15 až 20 %. To ovšem platilo v dobách levných paliv, kdy byla rozhodující cena kotle, a nikoliv jeho účinnost. S postupem času vzrůstal tlak na zvyšování účinnosti. Vliv měla vzrůstající cena paliv, ale i nová legislativa. Se zavedením dotací na výměnu starých kotlů začal přímo hon na vysoké účinnosti. Dotace přilákaly na trh desítky nových výrobců a dovozců, zákazník má stále větší problém se orientovat v kotlích, které si jsou velice podobné. Rozhodujícím argumentem je tak dosažená účinnost.
Bohužel tento „hon na zákazníka“, a tedy i na stále vyšší účinnost, se zvrhl. Vysoké účinnosti lze docílit především radikálním snížením komínové ztráty, tedy snížením teploty spalin, řádově na hodnotu 140 až 160 °C. Někteří výrobci však snižují teplotu spalin podstatně více, a to až pod hranici 100 °C při jmenovitém výkonu. Tím dosáhnou teoreticky účinností i nad 95 %, ale speciálně u kotlů spalujících uhlí již uvádějí na trh kondenzační kotle se všemi s tím spojenými potenciálními provozními problémy. Navíc se stále více objevují problémy s funkčností spalinových cest, protože nízká teplota spalin znamená snížení tahu komína.
Se snižující se komínovou ztrátou se však také snižuje její podíl na účinnosti. Zatímco u běžných kotlů tvořila 70 až 80 % ztrát, u „superúčinných“ to v některých provozních režimech není ani 50 %.
K měření komínové ztráty mám jednu faktickou poznámku. V případě, že pro přepočet ztráty je analyzátorem používán vztah s CO2, musí být jeho hodnota přepočtena na základě správně zadaného CO2max (má vliv i na konstanty A, B). Osobně jsem se setkal s mnoha protokoly, kde byla uvedena extrémně nízká komínová ztráta, protože technik prostě zapomněl (?) v analyzátoru přepnout z referenčního paliva plyn na palivo pevné (uhlí, dřevo).
Ztráta sdílením tepla do okolí
Tato ztráta je v běžné praxi dosti opomíjená. Obecně se má za to, že u dobře zaizolovaného kotle je zanedbatelná. Je pravda, že započítávání tepla sáláním vnějšího povrchu kotle do ztrát například u kotle umístěného v technické místnosti v nepodsklepeném rodinném domě je diskutabilní. Ale legislativa to vyžaduje. Velikost této ztráty je závislá na celkové ploše sálavé plochy kotlového tělesa a příkonu zdroje podle zjednodušeného vztahu dle [4] (v reálném výpočtu jsou plochy a jejich součinitele přestupu rozděleny na horizontální a vertikální složku)
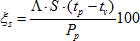
kde je
- Λ
- součinitel přestupu tepla z povrchu kotle do vnějšího prostředí,
- S
- plocha povrchu kotle,
- tp
- průměrná teplota povrchu kotle,
- Pp
- tepelný příkon kotle.
Při pohledu na vztah pro výpočet této ztráty je zřejmé, že její velikost je nepřímo úměrná příkonu kotle. Pokud kotel pracuje dlouhodobě v ustáleném provozním režimu, jsou celková sálavá plocha, součinitel přestupu tepla i teplota povrchu srovnatelné při jmenovitém i minimálním výkonu (většinu plochy tvoří izolovaná teplosměnná plocha, jejíž teplota závisí nikoliv na teplotě ve spalovacím prostoru, ale na teplotě otopné vody). Ovšem výrazně se mění jmenovatel ve vzorci, tedy příkon kotle. Se snižujícím se výkonem tak roste ztráta sáláním. A naopak, se snižujícím se výkonem klesá teplota spalin, tedy měla by se snižovat i komínová ztráta. V praxi to znamená, že se snižujícím se výkonem kotle narůstá podíl ztráty sáláním na celkových ztrátách kotle.
Pokud je kotel kvalitně zaizolovaný, jeho ztráta sdílením tepla do okolí se pohybuje v rozmezí 1–2 %. Pokud ale například u automatického kotle snížíme jeho výkon na 30 % výkonu jmenovitého, může se tato ztráta zvýšit na 3–5 %.
Praktický příklad
Ideální je demonstrovat výše napsané na konkrétním příkladu automatického kotle na dřevní pelety a hnědé uhlí s retortovým hořákem (viz tab. 1 a 2), tedy v současnosti nejprodávanějšího typu teplovodních kotlů moderní konstrukce. U jednotlivých ztrát je v závorce uveden podíl na celkových ztrátách.
Palivo: dřevní peleta | Jm. výkon | Min. výkon | |
---|---|---|---|
Teplota spalin | °C | 149 | 84 |
Ztráta citelným teplem (komínová) | % | 6,8 (70) | 4,5 (51) |
Ztráta plynným nedopalem | % | 0,1 (1) | 0,2 (2,3) |
Ztráta mech. nedopalem | % | 1,3 (13,4) | 0,4 (4,5) |
Ztráty ostatní (do okolí) | % | 1,6 (16,5) | 3,7 (42) |
Součet ztrát | % | 9,7 | 8,8 |
Palivo: hnědé uhlí | Jm. výkon | Min. výkon | |
---|---|---|---|
Teplota spalin | °C | 140 | 85 |
Ztráta citelným teplem (komínová) | % | 6,5 (57) | 5,3 (48,2) |
Ztráta plynným nedopalem | % | 0,2 (1,7) | 0,5 (4,5) |
Ztráta mech. nedopalem | % | 2,6 (22,8) | 1,4 (12,7) |
Ztráty ostatní (do okolí) | % | 2,1 (18,4) | 3,8 (34,5) |
Součet ztrát | % | 11,4 | 11 |
Z uvedených dat je zřejmé, že u moderních kotlů s relativně nízkou teplotou spalin hrají při stanovení celkové ztráty poměrně významnou roli vedle ztráty komínové také ztráty sáláním a u uhlí i mechanickým nedopalem. Velikost mechanického nedopalu se snižuje s poklesem výkonu, protože při stejně velké roštové ploše je při sníženém výkonu přidáváno na rošt méně paliva, které má tak více času na kvalitní dohoření před vytlačením do popelníku. To je významné právě při spalování uhlí, které má ve srovnání s dřevními peletami vysoký podíl pevné hořlaviny, která musí na roštu dohořet.
Patrný je naopak zvyšující se podíl ztráty sáláním se snižujícím se výkonem. Při spalování pelet se tato ztráta blíží ztrátě komínové.
Závěr
Pokud bychom při posuzování účinnosti teplovodních kotlů na pevná paliva postupovali striktně podle vyhlášky, museli bychom v případě nemožnosti využití přímé metody konstatovat, že účinnost nelze přesně stanovit, protože odhadnout celkovou účinnost pouze na základě naměřené komínové ztráty je prakticky nemožné a postup stanovení jednotlivých kotlových ztrát podle normy [2] je nepoužitelný. Řešením by určitě bylo, pokud by pro prokázání účinnosti zdroje bylo použito pouze hodnot naměřené komínové ztráty a zjištěná hodnota by byla porovnána s hodnotou referenční komínové ztráty citované ve vyhlášce. Referenční hodnoty by se stanovily podle roku výroby provozovaného zdroje, použité technologie spalování a používaného pevného paliva. Tento postup je již mnoho let například používán v Německu pro ověřování účinnosti kotlů na plyn a topné oleje.
Použité zdroje
- Vyhláška č. 194/2013 Sb. ze dne 28. června 2013 o kontrole kotlů a rozvodů tepelné energie.
- ČSN 07 0305 Hodnocení kotlových ztrát.
- ČSN EN 303-5:2012 Kotle pro ústřední vytápění – část 5: Kotle pro ústřední vytápění na pevná paliva, s ruční a samočinnou dodávkou, o jmenovitém tepelném výkonu nejvýše 500 kW – terminologie, požadavky, zkoušení a značení.
- ČSN 07 0240 Teplovodní a nízkotlaké parní kotle – Základní ustanovení.
The author draws attention to the question of determining efficiency of hot water solid fuel boilers according to the current legislation. The statements are supported with practical example.