Drátky získané z kovového odpadu a vyřazených pneumatik pro výrobu betonu
1. Úvod
Výroba drátkobetonu (betonového kompozitu ztuženého náhodně rozptýlenými vlákny) a jeho aplikace ve stavebnictví jsou stále častější v nenáročných betonových konstrukcích, jako jsou podlahy průmyslových hal a různé betonové výrobky – roury, vodní vpusti apod. Důvodem k takto omezeným aplikacím drátkobetonu ve stavebnictví je stále cena drátků ve vztahu k hmotnostní dávce drátků na jednotku objemu potřebné pro výrobu konstrukčních betonů. Drátkobetony s vyššími hmotnostními koncentracemi drátků jsou stále pro investory finančně nezajímavé.
Příspěvek uvádí možnosti využití kovového odpadu k výrobě drátků, stále ještě vhodných k výrobě drátkobetonu, avšak s nižší cenou oproti známým typům drátků nabízených současnými výrobci.
2. Hmotnostní dávka drátků pro výrobu konstrukčního drátkobetonu
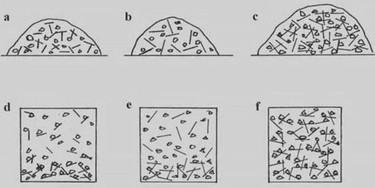
Obr. 1: Porovnání nesprávného a správného návrhu složení směsi. Čerstvě vyrobený vláknobeton s ocelovými vlákny – a) příliš krátká vlákna, b) nižší než minimální hmotnostní dávka, c) správný návrh směsi. Zpracovaný vláknobeton – d) a e) dochází k segregaci kameniva a drátků, f) vláknobeton je homogenní.
Jak již bylo řečeno, drátky ztužují strukturu drátkobetonu, což znamená, že užitá hmotnostní dávka drátků na jednotku objemu vyrobeného drátkobetonu je dostatečná, jak plyne z následujícího obrázku 1.
Dostatečnou hmotnostní dávkou drátků se rozumí, že drátky zajistí potřebné mechanické vlastnosti vláknobetonu a zejména přispějí k tvorbě homogenní struktury drátkobetonu. Jak plyne z uvedených obrázků, hmotnostní dávka nemůže být nikdy konstantní při širokém spektru vyráběných drátků a proměnnosti užitého kameniva. Vždy bude třeba přihlédnout k tvorbě struktury cementového kompozitu, a to zejména k množství a velikosti hrubé frakce kameniva a užité dávce drátků a její geometrii tak, aby drátky a hrubá frakce kameniva tvořily základní kostru struktury drátkobetonu, která je základem jeho homogenity.
Z uvedeného jednoznačně plyne, že každý drátkobeton má svoji recepturu provedenou separátním návrhem s cílem dosažení potřebných charakteristik ztvrdlého drátkobetonu se zárukou jeho homogenity.
Podle výsledků zkoušek se dlouhodobě ukazuje, že minimální hmotnostní dávka drátků, která je schopna ztužit strukturu drátkobetonu uvedeným způsobem je cca 40 kg/m3, to je cca 0,5 % objemového ztužení.
Z uvedeného též plyne, že hmotnostní dávky drátků v rozmezí kolem 20 kg/m3 současně užívané k výrobě drátkobetonu nejsou zárukou tvorby jeho homogenní struktury, obzvláště, jsou-li dávkovány do již navrženého čerstvého betonu jako další složka. Bez návrhu receptury, tj. úprav ve vztahu k užité hmotnostní dávce drátků a potřebné dávce hrubého kameniva se nedoporučuje drátkobeton vyrábět.
Příčina užití nízkých hmotnostních dávek drátků spočívá především v jejich jednotkové ceně drátků (Kč/kg) a navíc i v podceněné technologii výroby drátkobetonu obecně. Výsledkem je proto v současnosti užití drátkobetonu v nenáročných konstrukcích, jak je uvedeno v úvodu. Užití takto malých hmotnostních dávek drátků pro drátkobetony na nosné konstrukce není zárukou spolehlivosti konstrukcí.
Překlenout tyto skutečnosti mezi potřebnou hmotnostní dávkou drátků pro výrobu konstrukčního drátkobetonu a přijatelnou cenou drátků lze pouze snížením jednotkové ceny drátků (Kč/kg). Snížení současné ceny drátků je těžko uskutečnitelné, neboť drátkobeton je stále nosným konstrukčním materiálem vyráběný v malých objemech a tudíž konkurenční tlak vyvíjený na výrobu drátku je malý. Snížení ceny drátků vyráběných z odpadů, nebo lépe z druhotných surovin se však ukazuje jako možné.
3. Drátky z odpadových kovových pásků a vyřazených pneumatik
3.1 Drátky z odpadových kovových pásků
Rozhodující pro výrobu drátků z tohoto odpadového materiálu jsou tlakové a tahové pevnosti v rozmezí 350 MPa až 450 MPa. V každém případě vyrobené drátky jsou tak kvalitnějším materiálem, než je beton, a proto jejich vliv ve struktuře cementového kompozitu musí být přínosný. Tvrdost a poddajnost kovového odpadu, z něhož jsou drátky vyrobeny, vedly výrobce drátků k omezení na délku cca 30 mm z důvodů technologických, v případě jejich užití do struktury drátkobetonu. Následující obrázky ukazují základní materiál připravený pro výrobu drátků a vyrobené drátky včetně detailu jejich geometrických parametrů.
3.2 Drátky z vyřazených pneumatik
Kordová vlákna, která se nachází ve vyřazených pneumatikách, jsou velmi kvalitní s pevností v tahu kolem 2200 MPa. Technologickým problémem, avšak jak se ukázalo jako řešitelným, je jejich separace.
I zde, jako v případě vláken vyrobených z kovových pásků, se ukázalo, že z pohledu výroby technologie konstrukčního drátkobetonu je potřeba upravit jejich délku na cca 10 mm.
Na následujících obrázcích je vidět zdroj pro výrobu drátkobetonu – vyřazené pneumatiky (obr. 6) a výsledný produkt – drátky (obr. 7).
4. Závěr
Příspěvek by měl ukázat, že jako vždy lze nalézt cesty k řešení problému, v tomto případě ke zvýšení potřebné hmotnostní dávky drátků pro výrobu konstrukčních drátkobetonů snížením jejich ceny. Užitím těchto drátků by se neměla zvýšit cena drátkobetonu oproti současnosti, avšak měly by se zlepšit jejich charakteristiky – pevnosti, přetvárnost, hmogenita, což může být pro navrhovatele nosných konstrukcí zajímavé.
Uvedené příklady dvou typů drátků vyrobených z odpadových surovin, v tomto případě odpadových kovových pásků a vyřazených pneumatik, je třeba chápat jako cestu k částečnému řešení problému tj. ceny konstrukčního drátkobetonu.
Vyrobené drátky svými charakteristikami a parametry nemohou však pokrýt celé spektrum drátkobetonu, které je a bude možné využívat v betonovém stavitelství. V každém případě jejich přítomnost na trhu drátků vhodných pro výrobu drátkobetonu vytvoří tlak na ceny drátků současně nabízených.
Drátky současné výroby budou i nadále využívány pro výrobu drátkobetonu, protože drátkobetony svými charakteristikami by měly pokrýt potřebu při návrhu vytypovaných konstrukcí.
Užití těchto dvou typů drátků při výrobě drátkobetonu současně přispěje i k řešení jak smysluplně zpracovat a likvidovat kovový odpad ve prospěch životního prostředí.
Vliv uvedených dvou typů drátků na charakteristiky vyrobeného drátkobetonu není obsahem tohoto příspěvku.
Poděkování
Příspěvek vznikl za finanční podpory SGS13/040/OHK1/1T/11 a SGS13/120/OHK1/2T/11.
Článek se zabývá použitím kovových drátků v množství do 20 kg na 9 m3 hotového betonu a vláken z ojetých pneumatik do méně hodnotných betonů. Pro betony vyšších užitných vlastností je totiž nezbytné dávkovat min. 40 kg drátků na 1 m3 betonu, a to je již pro investory značná ekonomická zátěž. Navíc s nižším množstvím drátků nedochází většinou k rovnoměrnému rozmístění drátků v čerstvém betonu. V textu jsou vysvětleny zásady pro výrobu kvalitních drátkobetonů. V další části se pojednává o drátcích, vyrobených z odpadového kovového materiálu. Pevnost drátků závisí na kvalitě kovových pásků, z nichž jsou drátky vyráběny. Kordová vlákna z vyřezaných pneumatik jsou velmi kvalitní, pevnost v tahu až 2200 MPa. Problém je jejich separace od vláken gumových.
Odborné informace v textu článku ukazují cestu k řešení hlavního problému – ceny drátků. Nižší cena drátků z odpadních kovových pásků a vyřazených pneumatik umožním použít vyšší množství těchto drátků do betonu a tím zlepšit jejich využití v méně náročných konstrukcích. Současně je jejich používání příspěvkem ke smysluplnému zužitkování odpadů ve prospěch zlepšení životního prostředí.
Souhrnem lze říci, že jde o článek s velmi aktuální tématikou, zpracovaný týmem pracovníků, z nichž doc. Vodička je neúnavným propagátorem uplatnění drátkobetonu ve stavební praxi. Doporučuji článek otisknout beze změn.
Steel fiber reinforced concrete (SFRC) with higher concentrations of fibers are still unattractive for investors. The paper presents the possibility of using metal waste to produce of wires, still suitable for the production of SFRC, but with a lower price than the known types of wires offered by current producers.