Kotle – 2. část
Příspěvek se zabývá obecným popisem kotlů a jejich základním členěním na základě využívaných paliv a hlavních konstrukčních rozdílů. Pro jednotlivé skupiny kotlů jsou zde uvedeny obecné popisy a vlastnosti, největší důraz je kladen na vodotrubnaté kotle pro spalování tuhých paliv a popis roštových systémů.
4 Kotle na tuhá paliva
4.1 Roštové kotle
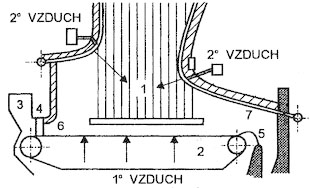
Obr. 4 Základní částí roštového ohniště (1)
Slouží ke spalování kusových paliv v pevné vrstvě. Používají se v průmyslu i domácím vytápění. V současné době se nové roštové kotle na uhlí téměř nestaví, je jich však velké množství v provozu. Nové roštové kotle se staví zejména pro spalování zejména biomasy (dřevo, sláma) a dále na spalování komunálních a průmyslových odpadů.
Základní částí roštového ohniště jsou patrné na obr. 4. Ohniště (1) je ohraničeno roštem (2), přední a zadní klenbou (6) a (7) a stěnami ohniště. Palivo se na rošt dostává ze zásobníku (3) přes hradítko výšky paliva (4) na rošt. Pevný zbytek – škvára odchází přes škvárový jízek (5) do škvárové výsypky. Kotle se vyznačují poměrně velkým množstvím škváry, až 60–70 % všech tuhých zbytků.
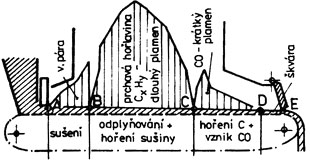
Obr. 5 Fáze spalování paliva na roštu (2)
Palivo na roštu prochází těmito charakteristickými fázemi:
- sušení – palivo se ohřívá na cca 120 °C a vypuzuje se z něho povrchová a hygroskopická voda,
- odplyňování – uvolňování prchavé hořlaviny, které probíhá intenzivně při ohřátí nad 250 °C,
- hoření prchavé hořlaviny a zápal vrstvy tuhé hořlaviny,
- dohořívání tuhé fáze a chladnutí tuhých zbytků.
Aby všechny fáze spalování na roštu dokonale proběhly, je třeba část tepla uvolněného spalováním vrátit do reakce a umožnit tak zapálení dalšího paliva. Tato část tepla se nazývá poměrné vzněcovací teplo.
Maximální teploty v ohništi roštových kotlů jsou pro uhlí cca 1350–1450 °C podle druhu uhlí, pro biomasu pak 1000–1300 °C.
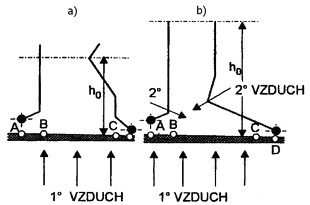
Obr. 6 Tvar ohniště roštového kotle
a) s jedním ohniskem hoření,
b) s dvěma ohnisky hoření (3)
Spalování u roštových ohnišť probíhá jednak ve vrstvě na roštu (tuhý uhlík), jednak v prostoru nad vrstvou paliva (uvolněná prchavá hořlavina). Podíl hoření nad vrstvou paliva je tím větší, čím vyšší je obsah prchavé hořlaviny v palivu. Z tohoto pohledu rozeznáváme dvě základní konstrukční koncepce, které jsou patrné z obr. 6:
- roštové ohniště s jedním ohniskem hoření – pro paliva s nízkým podílem prchavé hořlaviny,
- roštové ohniště s dvěma ohnisky hoření – pro paliva s vysokým obsahem prchavé hořlaviny.
Ohniště typu a) jsou vhodná pro pevná paliva s malým obsahem prchavé hořlaviny (antracit, černé uhlí). Ohniště mají menší výšku (h0) oproti typu b), který je vhodný pro paliva s větším obsahem prchavé hořlaviny (hnědé uhlí, rašelina, odpady, biomasa). Tato ohniště bývají seškrcená, aby při delším plamenu bylo zajištěno promísení prchavé hořlaviny se vzduchem. Tomu se napomáhá přivedením sekundárního, příp. terciárního vzduchu nad rošt. Jeho podíl je tím větší, čím vyšší je obsah prchavé hořlaviny.
4.1.1 Druhy roštů
Podle způsobu přemísťování paliva v roštovém ohništi rozeznáváme
- rošty s nehybnou vrstvou paliva (pevné rošty),
- rošty s občasným přemísťováním paliva (rošty stupňové a přesuvné),
- rošty s trvalým přemísťováním paliva (rošty pásové a řetězové).
Pevné rovinné rošty s nehybnou vrstvou paliva
Nejstarší typ roštů. V současné době se tento rošt zachoval u malých kotlů na lokální vytápění, event. u starších plamencových. Rošty jsou složeny z bezpropadových roštnic se spodním přívodem vzduchu. Palivo je přikládáno na žhavou vrstvu a je zapáleno spodním zápalem, sušení paliva, vypařování vody, odplyňování i hoření pevného uhlíku probíhá téměř současně. Nad rošt je třeba přivést sekundární vzduch pro dopálení uvolněné prchavé hořlaviny. Uvedené rošty mají velkou ztrátu mechanickým nedopalem ve škváře, úletu i propadu.
Rošty s občasným přemísťováním paliva
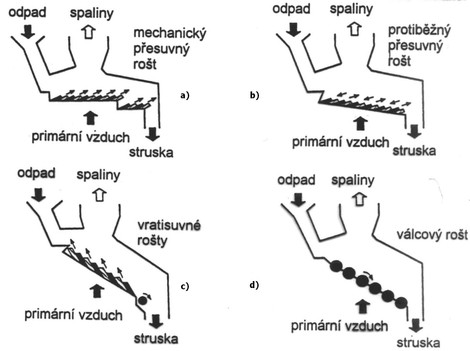
Obr. 7 Typy posuvných roštů: a) vodorovný posuvný rošt, b) šikmý rošt s přímým posunem,
c) šikmý rošt vratisuvný, d) rošt s válcovými roštnicemi
Rošty tohoto typu jsou tvořeny roštnicemi, kterými je možno pohybovat různými mechanismy. Patří sem rošty s výkyvnými roštnicemi, šikmé rošty s přímým posunem paliva, vratisuvné rošty a rošty s válcovými roštnicemi – obr. 7. Občasným, pravidelným či nepravidelným, pohybem roštnic dochází k rozrušování spečené vrstvy paliva, promíchávání paliva, posunu paliva a odvodu popele z ohniště.
Rošty s trvalým přemísťováním paliva
Jedná řetězové a pásové rošty tvořené nekonečným pásem, jehož horní plocha, na které spočívá vrstva paliva, tvoří rošt. Řetězový rošt je tvořen roštnicemi, které jsou články masivního Gallova řetězu. Pásový rošt má roštnice upevněny na příčných tyčích, které jsou unášeny dvěma postraními řetězy. V obou případech je rošt tepelně namáhán pouze v horní části, zatímco ve spodní části je chlazen. Z tohoto důvodu lze použít výhřevnější palivo, aniž by docházelo k opalu roštnic.
V současné době se nové roštové kotle staví především na spalování biomasy a různých druhů odpadů.
4.2 Kotle fluidní
Kotle pracující na principu spalování paliva ve fluidní vrstvě byly vyvinuty pro spalování paliva širokého rozsahu. Fluidizace je obecně děj, v němž je soubor pevných látek udržován ve vznosu proudem tekutiny. Fluidní vrstva tvoří disperzní systém, který se vytváří průtokem plynu vrstvou částic nasypaných pod pórovité dno – tzv. fluidní rošt. Náplň fluidní vrstvy tvoří palivo, odsiřovací aditivum (většinou vápenec) a aditivum pro stabilitu fluidní vrstvy (inertní materiál – např. písek).
Výhody fluidního spalování:
- Možnost dávkování vápence do kotle za účelem částečného odsíření spalin, účinnost odsíření je od 40 do 95 % podle typu kotle, kvality promísení paliva s aditivem a množství dávkovaného vápence, fluidní kotle tedy nevyžadují budování odsiřovacího zařízení za kotlem.
- Nízké teploty ve fluidní vrstvě a odstupňovaný přívod vzduchu do ohniště mají příznivý dopad na redukci NOx ve spalinách.
- Ve fluidních kotlích lze spalovat i méněhodnotná paliva a odpady s velmi nízkou výhřevností, v jiných typech kotlů nespalitelné.
- Spalování probíhá s vyšším zatížením roštové plochy oproti klasickým roštovým kotlům a rozměry roštu proto vycházejí nižší.
- Mají nižší komínovou ztrátu, neboť odsířené spaliny na konci kotle mohou mít v důsledku nižšího rosného bodu nižší teplotu. Účinnost kotlů bývá při jmenovitých parametrech 92–94 %.
Nevýhodou fluidního spalování je zvýšená citlivost na granulometrii paliva.
4.2.1 Atmosférické fluidní kotle se stacionární fluidní vrstvou (AFB)
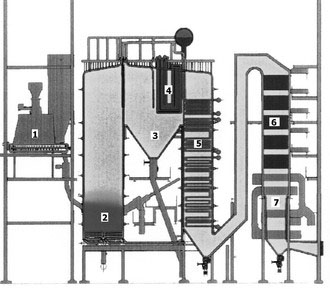
Obr. 8 Kotel s bublinkující fluidní vrstvou (4)
1 – zásobník paliva, 2 – fluidní vrstva, 3 – obratová komora,
4 a 5 – přehřívák, 6 – ekonomizér, 7 – LUVO
Charakteristickým rysem těchto kotlů je bublinkující (stacionární) fluidní vrstva se zřetelnou hladinou. Schéma kotle je na obr. 8. Palivo je přiváděno ze zásobníku paliva (1) do spalovací komory (2), kam je přiváděn i spalovací vzduch. Primární vzduch je veden skrze fluidní rošt a vytváří z paliva a aditiva fluidní vrstvu. Spaliny znečištěné popílkem pak odchází dohořívací komorou (kam bývá přiveden sekundární vzduch) do mezitahu (3), kde je odloučena velká část tuhého úletu. Dále spaliny prochází výhřevnými plochami parní části kotle (přehřívákem (5), ekonomizérem (6)) a ohřívákem vzduchu (7). Popílek je odveden na úložiště, u některých systémů je zaváděn zpět do fluidní vrstvy (2).
4.2.2 Atmosférické fluidní kotle s cirkulující fluidní vrstvou (ACFB)
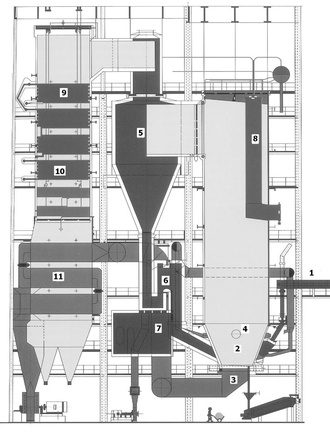
Obr. 9 Kotel s cirkulující fluidní vrstvou (4)
1 – přívod paliva, 2 – fluidní vrstva, 3 – primární vzduch,
4 – sekundární vzduch, 5 – cyklon, 6 – fluidní uzávěr (sifon),
7 – externí chladič popele, 8 a 9 – přehřívák, 10 – ekonomizér,
11 – LUVO
Principem kotlů s cirkulující fluidní vrstvou je cirkulace částic fluidní vrstvy (paliva i aditiva) mezi spalovací komorou a cyklonem, ze kterého jsou vraceny zpět do fluidního ohniště. Společným znakem těchto kotlů je prostup všech spalin z ohniště přes cyklony. Výhodou je delší pobyt částic ve spalovacím prostoru, který vede k lepšímu odsíření i vyhoření uhlíku (snížení ztráty mechanickým nedopalem). Tyto kotle se staví pro vyšší výkony než kotle s bublinkující (výkony 50–700 MWt).
Na rozdíl od kotlů AFB není u těchto kotlů zřetelná hladina fluidní vrstvy, která expanduje do prostoru ohniště. V důsledku cirkulace přes sifon se pevné částice vrací zpět do ohniště. Uvádí se, že průměrně velká částice paliva cirkuluje 10–15× než dojde k jejímu vyhoření. Základní schéma ACFB je na obr. 9. Drcené palivo je dodáváno spolu s mletým vápencem CaCO3 (1) do fluidní vrstvy (2). Roštem se přivádí primární vzduch (3) v podstechiometrickém množství, cca 70 % z celkového přiváděného vzduchu do kotle. Nad rošt se přivádí vzduch sekundární (4). Vlastní komora je vyložena membránovými stěnami. Rychlost spalin a popele ve výhřevných plochách je 4–8 m.s−1. Spaliny ze spalovací komory odchází do cyklonu (5), kde se odloučí 90 % prachových částic. Částice se vrací přes sifon (6) zpět do fluidní vrstvy (2). Kromě vracení popele je možná též cesta přes externí chladič popele (7), v němž jsou výhřevné plochy tlakového systému. Externí chladič tak zvyšuje regulovatelnost výkonu kotle a parametrů páry a lépe umožňuje přechod na jiná paliva.
4.2.3 Odsíření ve fluidní vrstvě
Výhodou fluidního spalování je možnost odsíření spalin přímo ve fluidní vrstvě. Děje se tak dodáváním vápence (příp. dolomitu) do spalovací komory. Při vstupu vápence do fluidního lože dochází vlivem teploty k rozkladu CaCO3 na CaO (viz rovnice (4) až (6)),

vzniklý CaO následně s SO2 a O2 sulfatizuje na CaSO4 reakcí


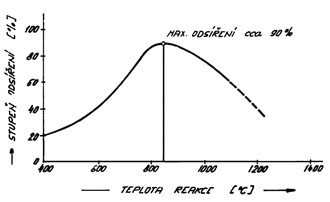
Obr. 10 Závislost odsíření na teplotě fluidního lože
Síran vápníku v podobě tuhých částic je potom zachycován v odlučovačích tuhých částic. Vzhledem k velmi jemné frakci tuhých částic je nutné k jejich zachycení použít textilních nebo elektrostatických odlučováků. Účinnost odsíření je závislá na teplotě ve fluidním loži, velikosti částic vápence, době zdržení v ohništi atd. Optimální teplota pro odsíření je 850–900 °C (viz obr. 10). Dávkování vápence se uskutečňuje na základě molového poměru Ca/S. U kotlů s cirkulující fluidní vrstvou se poměr dávkovaného Ca nebo přepočteného na CaO nebo CaCO3 ku obsahu síry v palivu S volí
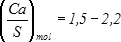
Zvýšením dávkování CaCO3 lze tedy zvýšit stupeň odsíření. Stupeň odsíření °S je definován vztahem
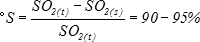
kde
- SO2(t)
- – teoretická koncentrace SO2 vypočtená z obsahu spalitelné síry [mg.m−3]
- SO2(s)
- – skutečně naměřená koncentrace SO2 [mg.m−3]
Praktické hodnoty °S:
- u stacionární fluidní vrstvy: 40–60 %,
- u cirkulující fluidní vrstvy: 90–98 %.
4.3 Kotle práškové
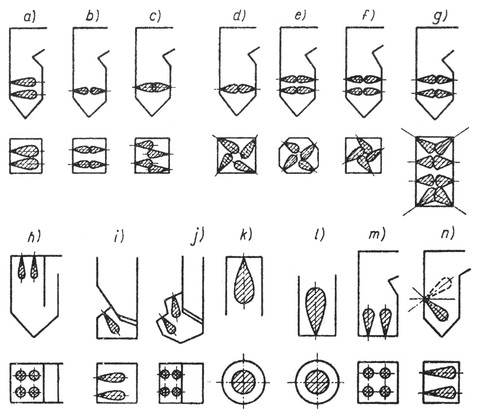
Obr. 11 Varianty hořáků v ohništích kotlů (3)
a – dvouřadé čelní, b – jednořadé protiběžné, c – jednořadé vystřídané, d – jednořadé rohové (tangenciální), e – dvouřadé rohové (tangenciální), f – dvouřadé rohové (tangenciální), g – dvouřadé kombinované, h, k – stropní, i, j – uspořádání v čelní stěně u výtavných ohnišť, l – naklápěcí
Práškové kotle spalují uhelný prášek, rozemletý na velikost zrn pod 1 mm, v hořácích. Rozemletím kusového uhlí na prášek dochází ke zvětšení měrného povrchu paliva 100násobně, a tím dochází i k intenzivnějšímu spalování. Práškové kotle také nemají rošt, který omezuje teplotu primárního vzduchu a zatížení ohniště. Proto jsou používány pro nejvyšší výkony. Prakticky největší kotel u nás má parní výkonnost 1678 tpáry.h−1 (elektrárna Ledvice), ve světě pak 4200 t.h−1. Práškové kotle se stavějí od cca 50 t.h−1.
Uhlí se na prášek mele v mlecích okruzích (používají se ventilátorové, tlukadlové, trubnaté a kladkové mlýny). V mlýnicích také dochází k vysušení paliva. Rozemletý prášek se ze zásobníku do ohniště přivádí pneumaticky nosným médiem, které nazýváme primární směs. Nosným médiem může být vzduch, spaliny nebo jejich směs. Směs nosného media a uhelného prášku (tzv. primární směs) a sekundární vzduch vstupuje do kotle práškovými hořáky. Různé varianty uspořádání hořáků jsou na obr. 11. V prostoru ohniště se směs mísí s další částí vzduchu – terciárním vzduchem. Doba spalování u práškových kotlů je 0,5–3 s, zatímco při spalování na roštu bývá v desítkách minut. Spalovací vzduch se předehřívá na 300–450 °C.
Mezi nevýhody práškových ohnišť patří zvýšení investičních nákladů na mlecí okruhy a snížení účinnosti celého zařízení díky vyšší vlastní spotřebě. Dalším dopadem používání práškových (zejména granulačních) ohnišť je vysoké znečištění spalin popílkem, které klade vyšší požadavky na následná odprašovací zařízení.
Rozeznáváme dva typy práškových kotlů:
- granulační se suchým odvodem tuhých zbytků z ohniště v podobě škváry,
- výtavné s tekutým odvodem tuhých zbytků z ohniště v podobě tekuté strusky tj. nad bodem tečení popele.
V našich práškových kotlích se téměř výhradně používá granulačních ohnišť, která jsou více vhodná pro spalování našich hnědých uhlí.
4.3.1 Granulační ohniště
Granulační ohniště je vhodné pro spalování méněhodnotných paliv. Spalování zde probíhá při relativně nízkých teplotách tak, aby nedošlo k překročení teploty tečení popele, což vyžaduje intenzivní chlazení spalovací komory. Částice popele jsou během spalování natavené, shlukují se a tvoří škváru. Škvára padá do spodní části ohniště, do výsypky, ze které je kontinuálně odváděna. Stupeň zachycení popele ve škváře je 8–20 % z celkového množství popeloviny obsažené v palivu. Zbytek odchází se spalinami, prochází všemi teplosměnnými plochami a je nutno jej zachytávat v odprašovacích zařízeních.
Teplota plamene v granulačním ohništi se pohybuje v závislosti na typu paliva mezi 1100 až 1500 °C. Aby teplota nepřekročila teplotu tečení popele, zavádí se následující opatření:
- Používá se paliva s nízkou výhřevností, vysokým podílem popelovin a vlhkosti.
- Uvolněné teplo se intenzivně odvádí stěnami spalovací komory. Stěny jsou tvořeny membránovými stěnami, tvořících plochu výparníku, v horní části mohou být vestavěny další teplosměnné plochy, např. sálavé přehříváky.
- Volí se nižší teplota předehřátí vzduchu, nebo vyšší přebytek vzduchu, nebo se do spalovací komory zavádí recirkulované spaliny.
4.3.2 Výtavné ohniště
Na rozdíl od granulačního ohniště, v ohništi výtavném záměrně překračujeme teplotu tečení popele, a takto vzniklou strusku odvádíme z kotle v tekutém stavu. Výtavné kotle se konstruují jako jednoprostorové nebo dvouprostorové, kde jsou výtavný a vychlazovací prostor odděleny struskovou mříží, nebo zúžením.
Výtavný prostor slouží ke spálení paliva a odvodu tekuté strusky, vychlazovací prostor zajišťuje vychlazení spalin pod teplotu měknutí popele, aby nedocházelo k nalepování popílku na teplosměnné plochy a stěny dalších tahů. Cílem zúžení nebo struskové mříže je udržení co nejvyšší teploty ve výtavné komoře. Stěny vychlazovacího prostoru jsou tvořeny membránovými stěnami. Dno výtavného ohniště je rovné nebo s malým sklonem a je opatřeno výtokovým otvorem. Pro usnadnění odtoku strusky s vysokou teplotou tavení popele je do paliva přidáváno tavidlo. Aby se zabránilo zatuhnutí strusky ve výtokovém otvoru je spalovací komora navržena tak, aby v oblasti výtoku byla nejvyšší teplota.
Vyšších teplot ve spalovací komoře se dosahuje:
- volbou vhodného paliva – výtavné kotle jsou vhodné především pro uhlí s vyšší spalovací teplotou, tj. pro kvalitní černá uhlí,
- nižším chlazením stěn spalovací komory – výtavné prostory kotlů jsou omazané keramickou hmotou, aby nedocházelo k intenzivnímu přestupu tepla,
- zvýšením jemnosti mletí,
- zvýšením teploty spalovacího vzduchu – až 450 °C,
- nižším přebytkem vzduchu,
- vhodným smísením paliva a vzduchu.
4.3.3 srovnání výtavných a granulačních ohnišť
- Výtavná ohniště mají vyšší stupeň zachycení popele v ohništi (40–70 %), což je výhodné, neboť struska odtéká z ohniště otvorem do vody, kde granuluje – tj. prudkým ochlazením a vnitřním tepelným pnutím se rozpadává na menší kusy. Takto v ohništi přímo zachycená struska se snadněji uskladňuje na složišti.
- Vyšší spalovací teploty u výtavných ohnišť, znamenající i vyšší uvolněné teplo, dovolují při konstruování těchto ohnišť vyšší měrné tepelné objemové zatížení ohniště, což má příznivý dopad na zmenšení velikosti ohniště i jeho obestavěný prostor.
- Vyšší spalovací teploty mají rovněž dopad na vznik SO3 a následné nízkoteplotní koroze dodatkových ploch kotle, neboť rosný bod je v průměru o 20 °C nižší než u ohnišť granulačních. To umožňuje volit u kotlů s výtavným ohništěm nižší teplotu spalin za kotlem a tím i nižší komínovou ztrátu.
Za nevýhody výtavných ohnišť lze považovat:
- Nevhodnost těchto ohnišť zejména pro méněhodnotná hnědá uhlí s vysokým obsahem prchavého podílu. Ve výtavných ohništích lze ekonomicky spalovat pouze kvalitní uhlí s menším obsahem prchavého podílu – tj. především antracity a černá uhlí.
- Uvedená paliva se obtížně vzněcují i hůře vyhořívají, takže je nutné mletí na jemnější částice. To zvyšuje měrnou mlecí práci, a tím i vlastní provozní náklady.
- Vzhledem k nebezpečí tuhnutí strusky v okolí výtokového otvoru mají výtavná ohniště nižší regulační rozsah (u granulačních cca 30–100 %, u výtavných cca 60–100 %).
- V důsledku velmi vysokých teplot spalování dochází k odpařování části popelovin, které pak kondenzují na dodatkových plochách kotle a způsobují těžko odstranitelné nánosy.
5 Kotle na spalování kapalných a plynných paliv
Při návrhu konstrukce i provozování kotlů na kapalná a plynná paliva je nutné si uvědomit jejich rozdílnost proti kotlům na paliva tuhá. Rozdíl mezi nimi spočívá především ve vyšší výhřevnosti paliv, nižších ztrátách a nepatrném obsahu popelovin (není nutno odvádět tuhý zbytek). Díky vysoké výhřevnosti má svítivý plamen topných olejů teplotu kolem 1800 °C a je velmi sálavý. Proces spalování těchto paliv je díky jemnému rozprášení paliva velice rychlý. Vzhledem k tomu, že ve spalinách nejsou tuhé částice a není nebezpečí popílkového otěru, je možné volit vyšší rychlosti spalin (až 20 m.s−1), což má za následek lepší přestup tepla konvekcí. Vyšší účinnost je dána nižšími ztrátami – odpadá ztráta mechanickým nedopalem a ztráta citelným teplem tuhých zbytků a u bezsirnatých paliv (kapalných i plynných) je také nižší komínová ztráta díky nízkému rosnému bodu spalin. Kotle na kapalná paliva dosahují účinnosti 93–95 %, kotle na plynná paliva pak 96–97 %. Dále kotle na kapalná a plynná paliva mají jednodušší palivové hospodářství, snadno se najíždění a regulují a dosahují nižších investičních a provozních nákladů. Kotle na kapalná a plynná paliva se často stavějí jako přetlaková bez možnosti přisávání falešného vzduchu. U dobře pracujících hořáků lze použít nižšího přebytku vzduchu (α = 1,05–1,1).
Nevýhodou tepelných zdrojů s kapalnými a plynnými palivy je cenově nákladné palivo. Při spalování kapalných paliv je také nutné počítat se zvýšenou tvorbou NOx a SOx (pokud nepoužíváme nízkosirnaté LTO). Vysoký obsah síry (až 3 % u těžších topných olejů), mimo nutných investic do odsiřovacího zařízení, způsobuje vyšší rosný bod spalin, a tím vyšší teplotu spalin do komína – cca 180 °C, vyšší sklon k nízkoteplotním korozím (koroze ze strany spalin obsahující síru), ev. sklon k vysokoteplotním korozím nad 600 °C v důsledku oxidů vanadu (rovněž ze strany spalin). Vyšší spalovací teploty podporují tvorbu NOx.
Nízkoteplotní koroze vzniká podkročením rosného bodu spalin na stěnách spalinovodu nebo výměníků. Na stěnách pak kondenzuje nejen vodní pára, ale i kyselina sírová, které vzniká podle rovnic (9) až (11).

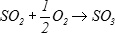

Hlavním opatřením proti vzniku nízkoteplotní koroze je udržení teplot teplosměnných ploch nad teplotou rosného bodu. Další opatření proti korozi se zavádějí:
- spalování s nízkými přebytky vzduchu (zamezení vzniku SO3),
- použití korozivzdorných materiálů,
- snižování obsahu síry – dávkování aditiv do spalovacího procesu,
- předehřev vzduchu vstupujícího do LUVO (většinou parou) na hodnoty 60–80 °C.
Vysokoteplotní koroze je způsobena oxidy vanadu (V2O5), které mají nízký bod tavení (nad 570 °C). Oxidy vanadu narušují ochrannou vrstvu trubek, ta je pak vystavena působení spalin a popílku. Množství vanadu v palivu se neměří, odhaduje se podle množství síry. Ochrana proti vysokoteplotní korozi je především nepřekračování teplot teplosměnných ploch nad teplotu tavení vanadu. Toto opatření však omezuje parametry vyráběné páry. Další možná, ale spíše podpůrná, opatření mohou být spalování s nízkým přebytkem vzduchu (aby se zamezilo tvorbě oxidů vanadu), případně přidáním inhibitorů (Mg).
6 Závěr
Tento příspěvek vznikl jako přepis přednášky z kurzu CŽV Udržitelná energetika, pořádaného Energetickým ústavem na Fakultě strojního inženýrství VUT v Brně. Zabývá se problematikou paliv a spalovacích zařízení. Jedná se však o velmi rozsáhlou oblast energetického oboru, že není ani zdaleka možné postihnout ji detailně článkem v rozsahu několika stran. Příspěvek proto přináší pouze základní informace o vlastnostech paliv, spalování a stručný přehled spalovacích zařízení s jejich základními charakteristikami. Detailnější informace k dané problematice je třeba hledat v odborné literatuře. Základní literární prameny uvádí v seznamu citací i tento příspěvek.
Literatura
- [1] Ochrana, L., Kadrnožka, J. Teplárenství. Brno : CERM, 2001. ISBN 80-7204-222-X.
- [2] Černý, V. Spalovací zařízení a výměníky tepla. Praha : ČVUT, 1988.
- [3] Černý, V., Janeba, B., Teyssler, J. Parní kotle. Praha : SNTL, 1983.
- [4] Šarbort, M. Kotle, Přehled rozvoje výroby kotlů. Brno : autor neznámý, 2000.
- [5] Vilimec, L. Stavba kotlů I. Ostrava : VŠB-TU Ostrava, 2006. ISBN 80-248-0076-4.
- [6] Černý, V. a kol. Parní kotle a spalovací zařízení. Praha : SNTL, 1975.
Příspěvek vznikl jako přepis přednášky z kurzu CŽV Udržitelná energetika, pořádaného Energetickým ústavem na Fakultě strojního inženýrství VUT v Brně. V celém rozsahu se příspěvek věnuje problematice spalovacích zařízení – kotlů. Příspěvek má přehledový charakter a představuje ucelený přehled problematiky energetických spalovacích zařízení. Silnou stránkou příspěvku je vysoká hustota informací, kdy každá věta je věnována novému pojmu nebo nové poznámce k problému.
Po odborné stránce je příspěvek z ruky fundovaného autora věnujícího se řadu let výuce spalovacích zařízení a výměníků tepla. Členění textu je voleno vhodně a umožňuje rychlou orientaci čtenáře v množství poskytnutých informací.
Informační hodnota článku je vysoká a článek představuje kvalitní přehled problematiky spalovacích zařízení. Doporučuji k publikování v předložené podobě.
The paper is focused on general description of boilers and their basic classification on the basis of using fuels and main design differences. There are mentioned general descriptions and parameters of particular sorts of boilers. There is put the most emphasis on water tube boilers for combustion of solid fuel and description of grate systems.