Generativní design jako spojenec s tradiční výrobou těžké strojírenské techniky
Německá společnost Claudius Peters už 113 let vyrábí těžké stroje pro zpracování sypkých materiálů – a teď prochází digitalizací, aby obstála i v 21. století. Generativní navrhování je pro ni zcela průlomové, umožňuje totiž úplně jinak přistupovat k navrhování i optimalizaci.
Generativní design bývá spojovaný s 3D tiskem, Claudius Peters ho ale využívá v tradiční výrobě – a dodává díky němu levnější produkty na trh, který je na cenu velice citlivý. Nový způsob navrhování firmě pomáhá snižovat spotřebu materiálu i energií a rychleji realizovat zakázky. Claudius Peters tak mnohem lépe obstojí v konkurenci, což se teď, když se celý obor rychle proměňuje, hodí dvojnásob.
Firma Claudius Peters je učebnicovým příkladem výrobce těžké strojírenské techniky. Dodává velké průmyslové stroje a technologie do závodů na zpracování cementu, oceli, sádry nebo hliníku. Už přes 100 let vyrábí obrovské a drahé průmyslové stroje – například dopravníky, sila či drtiče. „Jsme specialisti na manipulaci se sypkými materiály,“ říká Thomas Nagel, provozní ředitel společnosti. Ta sídlí nedaleko Hamburku a má 12 regionálních poboček v Severní i Jižní Americe, Evropě a Asii.
Thomas Nagel, který zastává pozici ředitele pro digitální technologie, se ale k věhlasné historii firmy nijak neupíná. Naopak hledí do budoucnosti a usiluje o to, aby byl Claudius Peters známý jako globální lídr na poli digitálních inovací. Vstříc inovacím se firma vydala v roce 2014 a za cíl si dala snížit náklady, zlepšit kvalitu, zkrátit dodací lhůty a zvýšit spokojenost zákazníků. Brzy se ale ukázalo, že pokud chce obstát v konkurenci uprostřed 21. století, nebude jí stačit jen zavést nový software. V roce 2018 navíc začala procházet transformací v agilní podnik a potřebuje nové digitální dovednosti i firemní kulturu zaměřenou na kreativní řešení problémů, experimentování a iterace.
Zefektivnění výroby pomocí vhodného softwaru
Při zavádění inovací byla pro Claudius Peters klíčová spolupráce s technologickými partnery, jako je Autodesk. Pro propojení vývoje, konstrukce, výroby, montáže, prodeje a všech procesů s nimi spojených firma zavedla nové nástroje, včetně aplikace Autodesk BIM 360. Výrobu také zjednodušila a zefektivnila pomocí programu Autodesk Inventor a zavedením analýz metodou konečných prvků (MKP). Při instalaci strojů začala používat 3D skenování – pomocí nástrojů Autodesk ReCap a Autodesk Navisworks sbírá data u zákazníků a následně je co nejrychleji předává vývojářům a konstruktérům v Německu. „Můžeme tak zakázku zpracovat rychleji, kvalitněji a levněji a naši zákazníci jsou spokojenější,“ pochvaluje si změnu Nagel.
Jak dodává, tím ale společnost s inovacemi neskončila. Ukázka generativního navrhování v aplikaci Fusion 360 ho inspirovala k tomu, aby ve firmě o této přelomové technologii uspořádal čtyřhodinový workshop.
Software firmy Autodesk pro generativní design hledá nejlepší konstrukční řešení podle zadaných kritérií a cílů a velmi rychle generuje desítky možností, ze kterých lze následně vybírat. Firemní tým nejprve při workshopu experimentoval s několika generickými součástkami a poté se rozhodl zkusit zoptimalizovat díl, který patří do chladiče slínku – jednoho ze základních strojů, které firma dodává do cementáren.
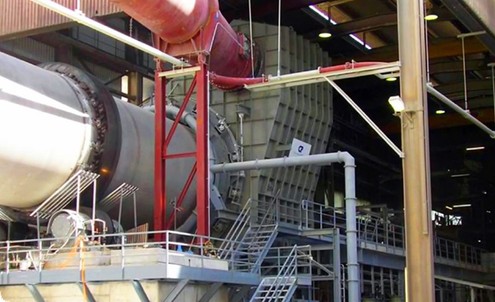
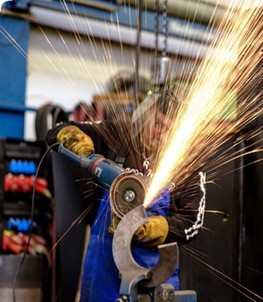
Právě cementárny jsou pro firmu Claudius Peters už od počátku její existence klíčovými odběrateli. V cementárnách se při výrobě cementu míchá kamenná drť a v rotační peci se při 1 450 °C vypaluje na malé zaoblené hrudky zvané slínek. Odtud se doruda rozpálený slínek odvádí do chladiče slínku – obrovského stroje o rozměrech 50 x 25 metrů. Tam se proudem studeného vzduchu prudce ochladí na zhruba 100 °C, posléze se nadrtí, smíchá s dalšími surovinami a vznikne cement.
Claudius Peters chladiče slínku vyrábí od počátku 50. let a zákazníkům jich od té doby dodal přes 700. Při výrobě slínku se ale spotřebuje ohromné množství energie a cementárenský průmysl je kvůli tomu jedním z největších producentů oxidu uhličitého na světě.
Po roce 2000 proto začal Claudius Peters vyvíjet novou generaci energeticky úspornějších chladičů slínku. Pojmenoval je ETA, podle řeckého písmene éta, kterým se energetická úspornost označuje. „Jednou z největších předností chladiče ETA je jeho skvělá tepelná účinnost. Související úspora energie má potenciál snížit negativní dopady výroby cementu na životní prostředí,“ vysvětluje Nagel. Ne nadarmo dnes většina zakázek firmy spočívá ve výměně starých chladičů slínku za nový model ETA, aby byly cementárny energeticky účinnější.
Při workshopu generativního designu se ve firmě Claudius Peters rozhodli zoptimalizovat právě díl z chladiče slínku ETA – šlo o těžký kovový díl, který firma nedávno předtím odlehčila pomocí tradičních konstruktérských postupů. V každém chladiči slínku je těchto dílů 50 až 60 a jsou sešroubovány dohromady na sestavě dopravníkových pásů, které roztavený slínek chladičem ETA posouvají. „Tento odlévaný díl jsme optimalizovali několikrát za sebou. Snažili jsme se ho odlehčit a ušetřit tak i náklady na materiál. Každé, byť sebemenší odlehčení, pro nás znamená obrovský užitek,“ vysvětlil Maximilian Lerch, který ve firmě pracuje jako konstruktér.
„S radostí jsem pozoroval, jak všichni konstruktéři obestoupili počítačovou obrazovku a sledovali, jak software pro generativní design vytváří optimalizovaný a pevný díl v podstatě na základě ničeho – stačilo jen pár zadaných kritérií. Software provede všechny iterace, které jsou potřeba k nalezení nejlepšího řešení,“ popisuje Lerch.
Po čtyřhodinovém školení generativního designu měl tým v ruce první výsledek: „Říkali jsme mu mimozemský díl. Překvapilo nás, jak moc se lišil od dílu, který už jsme sami zoptimalizovali. A navíc, jak mohl být o 30–40 % lehčí?“ říká Nagel.
Pokrok je ohromující
Firemní konstruktéři byli nejdřív k navrženému dílu skeptičtí a pečlivě propočítali a zanalyzovali jeho vlastnosti pomocí metody konečných prvků. Výsledky je ohromily – ukázalo se, že je díl mnohem úspornější než verze optimalizovaná klasickými postupy. Začalo pátrání po tom, jak navržený díl vyrobit. „Generativně navržené díly se obvykle vyrábějí aditivně, například pomocí 3D tisku. Pro náš obor je ale 3D tisk příliš drahý,“ vysvětlil Nagel.
Nakonec ale trvalo jen týden, než tým na základě poznatků z generativního navrhování i tradiční optimalizace zkonstruoval díl tak, aby ho šlo vyrobit běžnými metodami. Konstruktérský tým otestoval různá řešení ve firemní slévárně a vzal si na pomoc i aplikaci Autodesk Inventor a metodu konečných prvků. „Došli jsme k závěru, že díl nebudeme odlévat, ale vyrobíme ho svařením desek nařezaných laserem. Je tak levnější, o dalších 25 % lehčí a rychleji se vyrábí,“ popisuje Nagel. Tím ale optimalizace přepravního dílu nekončí, naopak – konstrukce hledá další možnosti, jak ho vylepšit a zlevnit. Brzy by měli ve firmě měli spustit jeho výrobu.
Generativně navržený přepravní díl může firmě Claudius Peters ušetřit na každém namontovaném chladiči slínku nezanedbatelnou částku. Při snížení hmotnosti dílu o zhruba 20 kg je očekávaná úspora asi 100 EUR za kus – a pro celý chladič slínku tuto částku můžeme vynásobit minimálně šedesáti. Nižší hmotnost s sebou nese i nižší náklady na dopravu. „Už při vytváření prvního prototypu jsme doufali, že nám generativní design pomůže snížit náklady na výrobu a zlepšit naši konkurenceschopnost,“ říká Nagel.
Generativní design přispívá i k udržitelnosti výroby. „Těžké díly odlévané v Indii nebo Turecku budeme moci nahradit lehčími, které se dají vyrábět přímo ve zdejším závodě. Šetříme tak materiálem a energií, zkracujeme dobu přepravy a zmírňujeme i další negativní dopady na životní prostředí,“ pochvaluje si Nagel.
Odteď bude ve firmě Claudius Peters generativní navrhování standardní součástí optimalizace stávajících dílů i navrhování dílů nových. „Chceme najít další díly, které můžeme v budoucnu zoptimalizovat a odlehčit. Postupně vyzkoušíme, jestli budeme mít s generativním designem u všech dílů stejně skvělé výsledky,“ plánuje Nagel.
Chcete se o nejvhodnějších softwarech pro generativní design dozvědět víc? Kontaktujte odborníka společnosti Autodesk ZDE.
Zdroj a foto: Autodesk