Syntéza žárovzdorné forsterit-spinelové keramiky z různých vstupních surovin
Článek se zabývá procesem syntézy žárovzdorné forsterit-spinelové keramiky za použití různých vstupních surovin. Vstupní suroviny byly rozemlety, smíchány v různém poměru a vypáleny při 1500 °C po dobu 2 h. Vypálené zkušební vzorky byly charakterizovány pomocí RTG difrakční analýzy a rastrovacího elektronového mikroskopu. Rovněž byla zkoumána pórovitost, nasákavost, objemová hmotnost, žárovzdornost, únosnost v žáru a odolnost proti změnám teplot. Vliv různých surovinových směsí byl zkoumán v souladu s výslednými vlastnostmi a mikrostrukturou všech vypálených vzorků. Přítomnost spinelu ve vzorcích vedla ke zlepšení mikrostruktury, mechanických vlastností a odolnosti proti změnám teplot. Zejména směsi s 10–20 % spinelu měly nejslibnější výsledky.
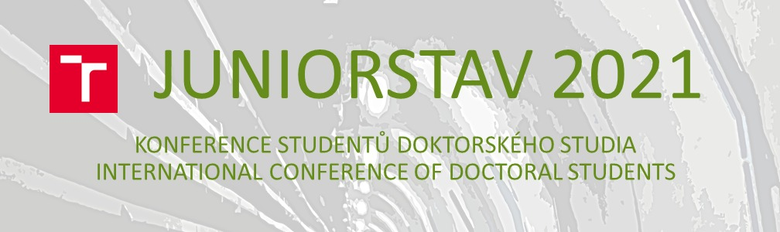
Článek byl vydán v rámci odborné konference doktorského studia Juniorstav 2021. Byl oceněn odbornou porotou konference a okomentován spolupracovníky redakce TZB Info.
1. Úvod
Žárovzdorná forsteritová keramika je důležitým typem materiálu, chemický vzorec forsteritu je 2MgOꞏSiO2 a forsterit se využívá především v metalurgickém a cementářském průmyslu jako vyzdívka metalurgických a rotačních pecí díky vysoké teplotě tání forsteritu až 1890 °C [1], [2], [3]. Forsterit je také využíván v elektrotechnickém průmyslu pro spojení keramiky s kovem, a to díky poměrně vysokému koeficientu délkové teplotní roztažnosti, který je podobný koeficientu kovů [4], [5]. Díky této vlastnosti vznikly také studie zabývající se výrobou forsteritových nanovláken pro výrobu tepelných izolantů [4], [5].
Kvůli vysokému koeficientu délkové teplotní roztažnosti má čistý forsterit poměrně malou odolnost proti náhlým změnám teplot. Tuto vlastnost lze vylepšit přidáním hořečnato-hlinitého spinelu (MA-spinel; spinel). Přidáním již malého množství (10–20 %) spinelu dochází ke zlepšení mikrostruktury, mechanických vlastností a zejména zvýšení odolnosti proti změnám teplot [6], [7]. Spinel lze syntetizovat z oxidu hlinitého a oxidu hořečnatého, jeho chemický vzorec je MgOꞏAl2O3.
Hlavním cílem tohoto příspěvku bylo stanovení vlivu různých surovinových směsí na výsledné vlastnosti forsterit-spinelové keramiky. Byly zkoumány zejména fyzikálně-mechanické vlastnosti jako jsou pórovitost, nasákavost, objemová hmotnost nebo pevnost v tahu za ohybu, fázové složení pomocí RTG difrakční analýzy, mikrostruktura pomocí rastrovacího elektronového mikroskopu a žárovzdorné vlastnosti.
2. Literární přehled/popis současného stavu
Doposud byly provedeny různorodé studie týkající se využití forsteritu jako krystalu v kruhových laserech [8], jako slibného biomateriálu pro transplantaci kostí v biomedicíně [9], [10] nebo také jako materiálu pro kompozitní nanomateriály [11], [12]. Jak již bylo zmíněno, primární využití nachází forsterit jako vyzdívka rotačních a metalurgických pecí díky vysoké teplotě tavení až 1890 °C a vysoké žárovzdornosti 1850 °C nebo v elektrotechnice pro spojení keramiky s kovem při výrobě různých součástek jako jsou například rezistory díky podobnému koeficientu teplotní roztažnosti, jaký mají kovy se stoupající teplotou.
Vysokoteplotní popílek, jenž je produkován jako druhotná surovina z elektráren spalující uhlí, lze využít jako levný zdroj oxidů hlinitého a křemičitého. Využitím i minoritního množství druhotné suroviny jako vstupní je velmi přínosné pro ekologii a má také pozitivní enviromentální vliv na udržitelný rozvoj v budoucnosti. Oxid křemičitý a hlinitý lze využít právě při slinování žárovzdorné keramiky. Elektrárenský popílek byl využitý v mnoha vědeckých studiích s dobrými výslednými vlastnostmi [13], [14]. Spinelová keramika se společně s magnezitem především využívá také jako vyzdívka rotačních pecí pro výrobu cementu a vápna díky velmi vysokému bodu tání 2135 °C, nízké teplotní roztažnosti v porovnání s forsteritovou keramikou a také dobrou odolností proti náhlým změnám teplot a korozní odolností [6], [7], [11]. Navzdory využití popílku pro syntézu žárovzdorné hlinito-křemičitanové keramiky bylo provedeno jen nemnoho výzkumů zabývajících se využití elektrárenského popílku pro syntézu jiných žárovzdorných materiálů obsahujících oxidy křemíku anebo hliníku, jako je například forsterit-spinelová keramika. To byl také podnět pro tento výzkum, jenž je zaměřen právě na málo probádanou oblast žárovzdorné keramiky s využitím popílku jako vstupní suroviny.
3. Metodika
Vstupní suroviny byly získány z několika různých lokalit. Kalcinovaný kaustický magnezit (CCM 85) ze Slovenských magnezitových závodů v Jelšavě, olivín od norské společnosti A/S Olivin, reaktivní oxid hlinitý CTC 22 od společnosti Almatis, Německo, vysokoteplotní popílek z elektrárny Mělník a kaolin Sedlec Ia od společnosti Sedlecký kaolin. Chemické složení vstupních surovin je zobrazeno v Tab. 1 a bylo stanoveno pomocí chemické analýzy a rentgenové fluorescence (XRF).
Vstupní suroviny | MgO [%] | SiO2 [%] | Al2O3 [%] | CaO [%] | Fe2O3 [%] | K2O + Na2O [%] | ZŽ * [%] |
---|---|---|---|---|---|---|---|
CCM 85 | 85,0 | 0,5 | 0,8 | 5,2 | 7,30 | 0,20 | 1,0 |
Olivín | 24,1 | 64,7 | 1,0 | 0,7 | 8,80 | 0,50 | 1,0 |
Reaktivní oxid hlinitý | 0,0 | 0,0 | 99,7 | 0,0 | 0,03 | 0,12 | 0,1 |
Popílek | 1,4 | 57,3 | 29,3 | 2,2 | 5,10 | 1,70 | 1,2 |
Kaolin Sedlec Ia | 0,5 | 46,8 | 36,6 | 0,7 | 0,85 | 1,20 | 13,2 |
* ztráta žíháním |
Celkem bylo navrženo 6 různých směsí, které byly rozděleny do dvou sad v závislosti na zdroji oxidu hlinitého pro syntézu spinelu. První sada tří různých směsí obsahovala jako zdroj oxidu hlinitého reaktivní oxid hlinitý CTC 22 (označeny ROH10–ROH30). Druhá sada tří různých směsí obsahovala jako zdroj oxidu hlinitého vysokoteplotní popílek (označeny VP10–VP30). Číslovka v názvu směsí označuje podíl popílku v množství 10 %, 20 % a 30 %. Z chemického složení bylo vypočítáno přesné množství oxidu hlinitého ve směsích s popílkem a v závislosti na něm bylo do směsí ROH přidáno poměrné množství reaktivního oxidu hlinitého, aby bylo dosaženo stejného molárního poměru. Surovinové složení všech navržených směsí je zobrazeno v Tab. 2.
Označení směsi | CCM 85 [hm. %] | Olivín [hm. %] | Reaktivní oxid hlinitý [hm. %] | Vysokoteplotní popílek [hm. %] | Kaolin Sedlec Ia [hm. %] |
---|---|---|---|---|---|
VP10 | 43,2 | 41,8 | – | 10,0 | 5,0 |
ROH10 | 41,0 | 51,1 | 2,9 | – | 5,0 |
VP20 | 44,1 | 30,9 | – | 20,0 | 5,0 |
ROH20 | 39,8 | 49,4 | 5,8 | – | 5,0 |
VP30 | 45,0 | 20,0 | – | 30,0 | 5,0 |
ROH30 | 38,6 | 47,8 | 8,6 | – | 5,0 |
Všechny směsi byly připraveny rozemletím hrubších vstupních surovin tak, aby propadly sítem o velikosti oka 0,064 mm. Po smíchání vstupních surovin byly směsi homogenizovány v rotačním mechanickém homogenizátoru po dobu 24 hodin. Po smíchání s vodou bylo pomocí Pfefferkornova přístroje zhotoveno optimální plastické těsto a z něj byly poté formovány zkušební vzorky ve tvaru hranolu o rozměrech 20 × 25 × 100 mm a ve tvaru kužele o výšce 50 mm a průměru 50 mm. Ze stejného plastického těsta také zkušební žároměrky ve tvaru jehlanu dle ČSN EN 993-13. Zkušební vzorky byly poté vysušeny v laboratorní sušárně při teplotě 105 °C do konstantní hmotnosti. Po sušení následoval výpal zkušebních vzorků při teplotě 1500 °C s teplotním nárůstem 4 °C/min a dobou výdrže 2 hodiny při maximální teplotě.
Vypálené zkušební vzorky byly poté podrobeny několika experimentům. Zdánlivá pórovitost, nasákavost a objemová hmotnost byly stanoveny dle ČSN EN 993-1. Délkové změny výpalem dle ČSN EN 993-10. Žárovzdornost byla provedena dle ČSN EN 993-12 na zkušebních žároměrkách, které byly umístěny do pozorovací pece s fotoaparátem, jenž umožňuje pozorování v reálném čase. Únosnost v žáru dle ISO 1893 byla provedena na válcových vzorcích a byla sledována teplota při 0,5% deformaci (T0,5). Odolnost proti změnám teplot dle ČSN EN 993-11 metoda B, jejíž výsledkem je parametr reziduální pevnost v ohybu, který je definován jako poměr pevnosti v tahu za ohybu cyklovaných vzorků k pevnosti v tahu za ohybu necyklovaných vzorků. RTG difrakční analýza pro stanovení mineralogického složení se zdrojem záření CuKα, urychlovací napětí 45 kV a proud 40 mA. Mikrostruktura byla pozorována pomocí rastrovacího elektronového mikroskopu s prvkovou sondou.
4. Výsledky
Směs | VP10 | ROH10 | VP20 | ROH20 | VP30 | ROH30 |
---|---|---|---|---|---|---|
Smrštění výpalem [%] | 7,2 | 7,7 | 7,5 | 8,6 | 11,5 | 10,3 |
Zdánlivá pórovitost [%] | 31,1 | 22,8 | 35,2 | 20,6 | 20,3 | 18,6 |
Nasákavost [%] | 13,3 | 8,5 | 16,1 | 7,6 | 9,4 | 6,7 |
Objemová hmotnost [kgꞏm−3] | 2340 | 2670 | 2190 | 2720 | 2230 | 2760 |
Žárovzdornost [°C] | 1695 | 1730 | 1670 | 1715 | 1645 | 1700 |
Únosnost v žáru T0,5 [°C] | 1600 | 1645 | 1585 | 1645 | 1535 | 1660 |
Pevnost v tahu za ohybu [MPa] | 13,5 | 12,8 | 17,4 | 19,2 | 19,5 | 20,7 |
Reziduální pevnost v ohybu [%] | 5,9 | 20,3 | 16,7 | 19,8 | 21,9 | 26,9 |
5. Diskuse
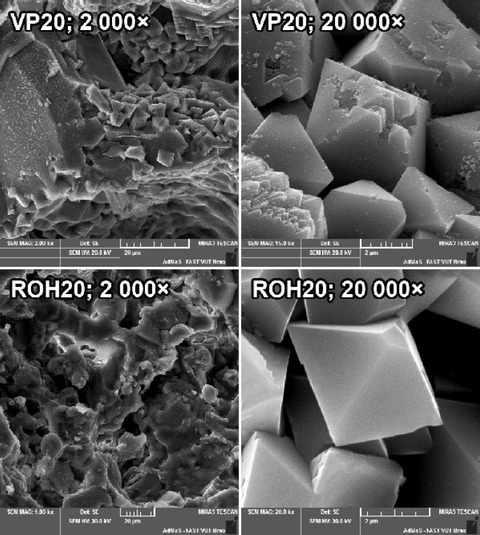
Obr. 2 Mikrofotografie z rastrovacího elektronového mikroskopu, směs s popílkem VP20 nahoře a směs s reaktivním oxidem hlinitým ROH20 dole
Výsledky navržených zkoušek jsou prezentovány v Tab. 3. S rostoucím podílem popílku ve směsi roste také smrštění výpalem těchto směsí v důsledku vyššího množství tavících oxidů jako jsou oxidy železa a alkálie. Na druhou stranu má však vyšší podíl tavících oxidů pozitivní vliv na rychlost slinování a zhutnění struktury, což vede ke snížené pórovitosti a nasákavosti za současném zvyšování objemové hmotnosti a pevnosti. Tavící oxidy mají však negativní vliv na žárovzdornost a únosnost v žáru. Žárovzdornost směsí s popílkem byla snížena o 4 % a únosnost v žáru T0,5 byla snížena o 6 %. Rozdíly mezi směsí s popílkem a reaktivním oxidem hlinitým tedy nebyly příliš výrazné.
S rostoucím podílem reaktivního oxidu hlinitého ve směsi roste také pevnost v tahu za ohybu. Pevnost se zvýšila z 12,8 MPa (směs ROH10) na 20,7 MPa (směs ROH30). Podobný trend sledovala také pevnost v tahu za ohybu u směsí s popílkem (VP10–VP30). S rostoucím podílem oxidu hlinitého ve směsi tedy vzrůstá podíl krystalů spinelu ve směsi, což vede ke zlepšení a zpevnění mikrostruktury a také pevností. Toto zlepšení je dokládáno přítomností spinelových krystalů na okrajích větších shluků forsteritových krystalů, jejich vzájemnému provázání a propojení krystalů spinelu zakotvených v amorfní skelné matrici, jak lze vidět na Obr. 2. Vylepšením mikrostruktury krystaly spinelu dochází také ke zlepšení odolnosti proti změnám teplot. Největší rozdíly jsou u směsí s popílkem, kdy reziduální pevnost v ohybu u směsi VP10 byla 5,9 % a ve směsi VP30 již 21,9 %.
Výsledky RTG difrakční analýzy jsou zobrazeny na Obr. 1. Všechny směsi obsahují majoritní krystalickou fázi forsterit a minoritní krystalické fáze spinel, periklas a monticellit. Rozdíly mezi množstvím přidaného popílku nebo reaktivního oxidu hlinitého jsou pouze v intenzitě peaků spinelu. Přítomnost oxidů železa je indikována šumem na pozadí, jenž je výraznější u směsí s vysokoteplotním popílkem VP10–VP30. Přítomnost amorfní skelné fáze je indikována zakřiveným pozadím při nízkých úhlech 2theta (5–25°).
Morfologie a mikrostruktura byla sledována pomocí rastrovacího elektronového mikroskopu a mikrofotografie jsou vyobrazeny na Obr. 2. Krystaly spinelu vznikly ve shlucích jak ve směsích s elektrárenským popílkem, tak ve směsích s reaktivním oxidem hlinitým. Morfologicky se jednalo o rombické dipyramidy o velikosti 2–4 μm. Krystaly spinelu se nacházely na okrajích větších forsteritových zrn a také na jejich pomezí, spojující je dohromady. Krystaly spinelu, které byly syntetizovány ze směsí s reaktivním oxidem hořečnatým, byly rovnoměrnější s hladkým povrchem a bez trhlin či jiných nedokonalostí. Krystaly spinelu, které byly syntetizovány ze směsí s elektrárenským popílkem, měly trhliny s členitými a nepravidelnými hranami. Tento jev lze vysvětlit skutečností, že krystaly spinelu ze směsí s reaktivním oxidem hlinitým vznikají přímou syntézou tohoto oxidu s oxidem hořečnatým, zatímco krystaly spinelu ze směsi s popílkem vznikají nepřímo z rozkladu mullitu na oxid hlinitý a oxid křemičitý a následně pak reakcí mezi oxidem hlinitým a hořečnatým.
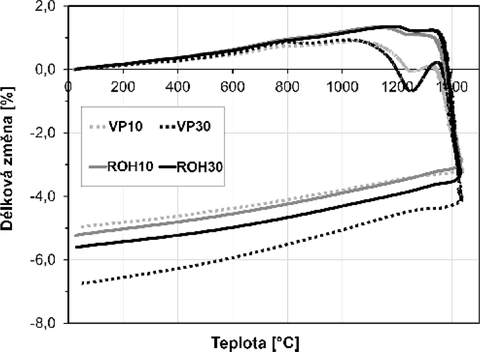
Obr. 3 Dilatačně-kontrakční termická analýza směsí s popílkem (tečkovaně) a reaktivním oxidem hlinitým (plně)
Dilatačně-kontrakční termická analýza směsí je prezentována na Obr. 3. Znatelné rozdíly mezi směsí s popílkem a reaktivním oxidem hlinitým byly pozorovány při teplotě nad 1000 °C. Zkušební vzorky ze směsí s popílkem měly při zkoušce čtyři rozdílné fáze. V první fázi došlo k lineární expanzi vstupních surovin, která byla pozorována až do 1000 °C, poté následovala fáze smršťování v teplotním intervalu 1000–1250 °C. Třetí pozorovaná fáze se vyznačovala expanzí v teplotním intervalu 1250–1350 °C, jenž byla způsobena růstem krystalů mullitu a jeho následným rozkladem a reakcí s oxidem hořečnatým za vzniku spinelu, což vedlo také ke tvorbě kapalné skelné fáze. Toto chování bylo také pozorováno v jiných pracích [15], [16] a předchozím výzkumu [17], [18]. Čtvrtá fáze nastala v teplotním intervalu nad 1350 °C a způsobila opětovné smršťování v důsledku působení tavících oxidů a kapalné skelné fáze na proces slinování.
6. Závěr
Žárovzdorná forsterit-spinelová keramika byla syntetizována ze směsí s elektrárenským popílkem nebo reaktivním oxidem hlinitým pro srovnání výsledných vlastností a účinků tavících oxidů obsažených ve vstupních surovinách a celkovému porovnání vlivu vstupních surovin na výsledné vlastnosti a mikrostrukturu. Krystaly spinelu vytvořené ze směsí s reaktivním oxidem hlinitým byly rovnoměrnější a bez prasklin či vad a výsledné vlastnosti jako je pevnost v tahu za ohybu a odolnost proti náhlým změnám teplot byly zlepšeny s rostoucím podílem oxidu hlinitého ve směsi, aniž by došlo ke zhoršení žárovzdorných vlastností.
Krystaly spinelu vytvořené ze směsí s elektrárenským popílkem byly méně rovnoměrné a měly praskliny a nerovnoměrné hrany, avšak výsledné vlastnosti (pevnost v tahu za ohybu, odolnost proti náhlým změnám teplot) byly také zlepšeny ve směsích s 10 hm. % a 20 hm. % popílku při současném mírném zhoršení žárovzdorných vlastností v jednotkách procent.
Přítomnost tavících oxidů – oxidy železa a oxid sodný a draselný (alkálie) ve vstupních surovinách umožnily rozklad mullitu přítomného v popílku pod jeho běžnou teplotou tavení, což umožnilo krystalizaci spinelu a vytvoření kapalné skelné fáze, která podpořila dokonalejší slínání těchto směsí.
Závěrem lze říci, že přítomnost minoritního množství spinelu ve forsteritové keramice zlepšila mikrostrukturu, pevnost v tahu za ohybu a také odolnost proti náhlým změnám teplot. Oxid hlinitý pro syntézu spinelu lze nahradit elektrárenským popílkem jako vstupní surovinou v množství 10–20 hm. % popílku za současného dosažení pozitivních výsledných vlastností při syntéze forsterit-spinelové žárovzdorné keramiky.
Poděkování
Tento příspěvek byl podpořen v rámci řešení juniorského grantu specifického výzkumu pod interní grantovou agenturou Vysokého učení technického v Brně s číslem FAST-J-20-6196 a názvem: Vývoj žárovzdorných materiálů na bázi forsterit-spinel-magnezit s ohledem na odolnost proti korozi různými korozivními médii.
Použité zdroje
- BUDNIKOV, P. P. a kolektiv. Technologie keramiky a žárovzdorného zboží. Praha: Státní nakladatelství technické literatury, 1960, ISBN 9780262523776
- KINGERY, W. Introduction to ceramics. New York: Wiley, 1960, xvi, 781 s. ISBN 04-714-7883-0.
- ZHAO, Fei, Lixin ZHANG, Zhen REN, Jinxing GAO, Xiaoyu CHEN, Xinhong LIU a Tiezhu GE. A novel and green preparation of porous forsterite ceramics with excellent thermal isolation properties, Ceramics International, 2019, 45(3), 2953–2961, ISSN 02728842, https://doi.org/10.1016/j.ceramint.2018.09.296
- BOUHIFD, M. A., D. ANDRAULT, G. FIQUET a P. RICHET. Thermal expansion of forsterite up to the melting point, Geophysical research letters, 1996, 23(10), 1143–1146
- HEILMANN, F.; Rixecker, G.; Börner, F. D.; Lippmann, W.; Hurtado, A. Fe2O3-doped forsterite ceramics as a joining partner for ZrO2 in a laser brazing process. Journal of European Ceramics Society, 2009, 29, 2783–2789,
https://doi.org/10.1016/j.jeurceramsoc.2009.03.028. - MUSTAFA, E.; Khalil, N.; Gamal, A. Sintering and microstructure of spinel–forsterite bodies. Ceramics International 2002, 28, 663–667, https://doi.org/10.1016/S0272-8842(02)00025-1.
- EWAIS, E.M.M.; El-Amir, A.A.M.; Besisa, D.H.A.; Esmat, M.; El-Anadouli, B.E.H. Synthesis of nanocrystalline MgO/MgAl2O4 spinel powders from industrial wastes. Journal of Alloys and Compounds. 2017, 691, 822–833,
https://doi.org/10.1016/j.jallcom.2016.08.279. - AHMAD, H.B.; McKinnie, I.T. Chromium doped forsterite ring laser. Opt. Laser Technol. 1995, 27, 403–406,
https://doi.org/10.1016/0030-3992(95)00031-3. - KHARAZIHA, M.; Fathi, M.H. Synthesis and characterization of bioactive forsterite nanopowder. Ceram. Int. 2009, 35, 2449–2454, https://doi.org/10.1016/j.ceramint.2009.02.001.
- NI, S.; Chou, L.; Chang, J. Preparation and characterization of forsterite (Mg2SiO4) bioceramics. Ceram. Int. 2007, 33, 83–88, https://doi.org/10.1016/j.ceramint.2005.07.021.
- TAVANGARIAN, F.; Emadi, R. Synthesis of pure nanocrystalline magnesium silicate powder. Ceram. Silikat. 2010, 54, 122–127, ISSN 1804-5847.
- FATHI, M.H.; Kharaziha, M. Mechanically activated crystallization of phase pure nanocrystalline forsterite powders. Mater. Lett. 2008, 62, 4306–4309, https://doi.org/10.1016/j.matlet.2008.07.015.
- KUMAR, M.S.; Vanmathi, M.; Senguttuvan, G.; Mangalaraja, R.V.; Sakthivel, G. Fly Ash Constituent-Silica and Alumina Role in the Synthesis and Characterization of Cordierite Based Ceramics. Silicon 2018, 11, 2599–2611,
https://doi.org/10.1007/s12633-018-0049-0. - REN, Q.; Ren, Y.; Wu, X.; Bai, W.; Zheng, J.; Hai, O. Effect mechanism of spinel (MgAl2O4) reinforced corundum ceramics on microstructure and properties. J. All. Com. 2019, 793, 146–154,
https://doi.org/10.1016/j.jallcom.2019.04.151. - DONG, Y.; Hampshire, S.; Zhou, J.; Ji, Z.; Wang, J.; Meng, G. Sintering and characterization of fly ashbased mullite with MgO addition. J. Eur. Ceram. Soc. 2011, 31, 687–695, https://doi.org/10.1016/j.jeurceramsoc.2010.12.012.
- CAO, J.; Dong, X.; Li, L.; Dong, Y.; Hampshire, S. Recycling of waste fly ash for production of porous mullite ceramic membrane supports with increased porosity. J. Eur. Ceram. Soc. 2014, 34, 3181–3194
https://doi.org/10.1016/j.jeurceramsoc.2014.04.011. - NGUYEN, M.; Sokolář, R. Formation and Influence of Magnesium-Alumina Spinel on Properties of Refractory Forsterite-Spinel Ceramics. Materiali in Tehnologije, 2020, 54, 135–141, https://doi.org/10.17222/mit.2019.198.
- NGUYEN, Martin a Radomír SOKOLÁŘ. Impact of Fly Ash as a Raw Material on the Properties of Refractory Forsterite–Spinel Ceramics. Minerals. 2020, 10(9). ISSN 2075-163X. https://doi.org/10.3390/min10090835.
V roce 2015 získal doc. Ing. Radomír Sokolář, Ph.D. Cenu Silikátové společnosti ČR, oceněny byly i diplomové práce VUT v Brně. Těší nás, že ve své práci pokračuje a získává pro svůj obor i nové studenty. Přejeme jejich výzkumu žárovzdorných materiálů na bázi forsterit-spinel hodně úspěchů, výběr a použití vhodných vstupních surovin a optimalizace směsí z hlediska obsahu spinelu a forsteritu je pro obor jedním z klíčových témat.
This article examines the process for the synthesis of forsterite–spinel refractory ceramics from different raw materials. Raw materials were milled, mixed in different ratios and sintered at 1500 °C for 2 h. Sintered samples were characterized by XRD and SEM. Porosity, water absorption, bulk density, refractoriness, refractoriness under load and thermal shock resistance were also investigated. The impact of different raw material mixtures was investigated in accordance with the resulting properties and microstructure of all fired samples. Presence of spinel in fired samples led to improved microstructural and mechanical properties and thermal shock resistance. In particular, mixtures with 10–20 % of spinel had the most promising results.