Ultrazvuk jako možný nástroj inspekce ocelových prvků stavebních konstrukcí
V oblasti diagnostiky stavebních konstrukcí se používají nedestruktivní a destruktivní metody hodnocení vybraných vlastností stavebních hmot. Rovněž jsou posuzovány konstrukční prvky, ale i vybrané části. Ultrazvuková metoda, která patří k metodám nedestruktivního testování, se používá již řadu let pro diagnostiku betonových a ocelových konstrukcí. Článek představuje možnosti provádění kontrol vybraných prvků ocelových konstrukcí.
1. Úvod
V posledních letech došlo k velkému rozvoji v oblasti nedestruktivního testování stavebních konstrukcí díky nezadržitelnému vývoji elektrotechniky a elektroniky. Na trhu jsou k dispozici nejrůznější měřicí zařízení a přístroje, pomocí kterých je možné hodnotit vybrané parametry konstrukcí a konstrukčních prvků z různých stavebních materiálů. Ve stavební praxi jsou diagnostické metody založené na nedestruktivním principu zkoušení velmi vítány, jelikož během měření nedochází k porušení konstrukčního prvku a také především pro možnost opakovatelnosti a reprodukovatelnosti zkoušek. Mezi jednu z nejvyužívanějších diagnostických metod patří metoda ultrazvuková, o jejichž počátcích je možné zaslechnout již ve třicátých letech 20. století. Široká nabídka nejrůznějších ultrazvukových přístrojů vyráběných a stále modernizovaných dle potřeb uživatelů umožňuje pracovníkům provádějících diagnostiku konstrukcí výběr vhodného ultrazvukového přístroje. Pomocí ultrazvukové defektoskopie je možné charakterizovat především vnitřní strukturu konstrukčního prvku či konstrukce a na základě vyhodnocení provedených zkoušek lze v poměrně krátké době získat informace o vybraných parametrech zkoušeného materiálu. Tato metoda je vhodná pro hodnocení betonových i ocelových konstrukcí. Předmětem článku je prezentovat vybrané ukázky využití ultrazvukové metody při inspekci ocelových prvků stavebních konstrukcí in-situ [1, 2].
2. Ultrazvuková metoda
Ve stavebnictví jsou nejčastěji používány dvě základní ultrazvukové metody. Nejstarší a nejjednodušší je metoda průchodová, jejímž hlavním znakem je měření procházejícího akustického tlaku nebo zjišťování doby průchodu ultrazvukových vln vyšetřovaným prostředím. Dvě sondy, z nichž jedna vysílá a druhá přijímá ultrazvukový impuls, jsou umístěny nejlépe souose na protilehlých stranách vyšetřovaného prostředí. Jejím omezením je nutnost použití dvou sond, což při diagnostice stavebních konstrukcí může být občas problematické. Další metodou je metoda impulsová odrazová, jejíž princip spočívá ve vysílání impulsů, které jsou zachycovány a zobrazeny pomocí tzv. A-skenu, Obr. č. 1.
Odražené impulsy se vracejí buď do téhož elektroakustického měniče, nebo do přijímacího měniče. Elektrické signály vzniklé dopadem ultrazvukových impulsů se zesílí v zesilovači a přivedou se na vertikální vychylovací systém obrazovky buď přímo, nebo až po usměrnění a filtraci. Filtrací se získá jasnější a přehlednější zobrazení na stínítku obrazovky, avšak ztrácejí se i některé podrobnosti. Tato metoda dává informaci o velikosti odrazové plochy, a to podle výšky odraženého impulsu (echa). Kromě toho podle doby průchodu echa lze stanovit hloubku odrazové plochy nebo rychlost šíření ultrazvukových vln a podle tvaru přijímaného echa lze usuzovat na charakter odrazové plochy. Metoda je vhodná kupř. pro měření ocelových prvků zabudovaných do betonu, kdy je umožněn přístup pouze z jedné strany. Celkový souhrn metod ultrazvukové defektoskopie je uveden v Tabulce č. 1 včetně informací, které lze při správné volbě UZ přístroje, sond a vhodném nastavení získat [3, 4, 5].
Metoda | Použití | Druh informace | Omezení |
---|---|---|---|
průchodová, spojitá a impulsová | tenké materiály, plechy, kontakty, dráty, spoje, látky s vysokým útlumem | přítomnost vady | malá citlivost a rozlišovací schopnost; nutné dva přístupné povrchy; silný vliv jakosti povrchu |
odrazová impulsová | všeobecné použití kromě tenkých předmětů | lokalizace, hloubka, velikost, popř. tvar vady, tloušťka předmětu | složitější vyhodnocení, mrtvé pásmo |
rezonanční | měření tloušťky a zjišťování vady spoje tenkých materiálů | rezonance s délkou vlny | pouze pro předměty s konstantní tloušťkou |
impedanční | měření tloušťky a zjišťování vady spoje tenkých materiálů | přítomnost vady | vliv jakosti povrchu |
akustická emise | vyšetřování stavu a průběhu namáhání součástí | četnost emitovaných impulsů a jejich spektrum | složité vyhodnocování významu indikací – zvláště při pozadí rušivých šumů |
Ústav stavebního zkušebnictví VUT v Brně disponuje několika ultrazvukovými přístroji a tloušťkoměry. Jak již bylo zmíněno, volba přístroje je velice podstatná a odvíjí se hlavně od parametrů zkoušeného prvku. Pro ověření spolehlivosti měření pomocí zmiňovaných přístrojů musí být provedeny laboratorní zkoušky, na základě kterých se určí maximální rozsah a citlivost měření. Lze konstatovat, že pro měření in-situ se jeví jako nejvhodnější ultrazvukový přístroj SONIC 1200 HR [4].
3. Inspekce ocelových prvků stavebních konstrukcí
3.1 Ultrazvuková kontrola spojovacích šroubů pláště ocelového zásobníku
Příklad provedené inspekce je provedení laboratorních zkoušek ocelových šroubů, které byly nainstalovány jako spojovací prvky ocelového zásobníku, Obr. č. 2. Dodané vzorky těchto spojovacích prvků byly použity pro kalibraci UZ přístroje SONIC 1200 HR od firmy STAVELEY INSTRUMENTS INC – USA a zároveň jako měřítko pro případné odchylky či změny ultrazvukového signálu v případě vnitřních nehomogenit zjišťovaných in-situ. V laboratoři byly zaznamenány echogramy pro dva druhy šroubů. Tyto výstupní laboratorní echogramy byly vzaty jako průchodová echa neporušených šroubů, viz Obr. č. 3.
Obr. č. 3: Echogram spojovacího šroubu č. 1. Ultrazvukový přístroj SONIC 1200 HR, přímá piezoelektrická sonda s frekvencí 10 MHz (vlevo). Provedení laboratorních zkoušek na dodaných šroubech, které byly instalovány ve stěně ocelového zásobníku (vpravo).
Měření bylo realizováno pomocí impulsové odrazové metody. Během měření byla věnována pozornost poruchám v oblasti závitu, kde je oslaben průřez spojovacího šroubu. V případě poruchy se na A-skenu UZ přístroje zobrazí odrazové echo, které vzniká při přechodu ultrazvukového signálu přes dvě odlišná rozhraní (ocel/vzduch). Celkem bylo testováno 50 spojovacích šroubů: po obvodu nádrže bylo vybráno 7 řezů, v každém řezu bylo zkoušeno 7 náhodně vybraných spojovacích šroubů dle rastru navrženého objednavatelem. Spojovací šrouby byly zkoušeny ve staticky nejvíce namáhaném pásu kruhové nádrže. Ultrazvuková kontrola neprokázala výrazné poškození předmětných šroubů, neboť byly porovnány laboratorní kalibrační echogramy a echogramy získané přímo na místě měřením na spojovacích šroubech a nebyla prokázána žádná vnitřní vada či trhlina. Závěrem bylo možno prohlásit, že celkem 50 testovaných spojovacích šroubů nebylo poškozeno vadami či trhlinami.
3.2 Ultrazvuková kontrola tloušťky patního plechu ocelových zásobníků na tekutá hnojiva
Další ukázkou diagnostického měření pomocí ultrazvukového přístroje SONIC 1200 HR je ověření tloušťky základových patních plechů ocelových zásobníků na tekutá hnojiva. Podezření ze zmenšení tloušťky plechu bylo vysloveno kvůli působení korozivních účinků okolního prostředí. Ultrazvukový přístroj byl z důvodu zvýšení přesnosti měření před hodnocením patních plechů kalibrován a nastaven v úzkém rozsahu měření tloušťky od 4 mm do 6 mm. Pečlivě byla zvolena zkušební místa, která musela být obroušena pro lepší akustickou vazbu ultrazvukového signálu. Výběr zkušebních míst byl zvolen tak, aby vždy jedno měření postihlo ¼ obvodu nádrže. V každé zkušební pozici byla provedena vždy tři platná měření tak, aby se jednotlivá měření nepřekrývala, viz Obr. 4.
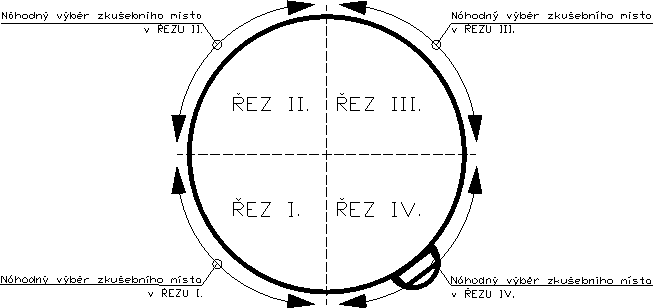
Obr. č. 4: Schéma rozdělení nádrže na čtyři řezy, v každém řezu byla vždy po obvodu nádrže náhodně zvolena zkušební pozice pro měření tloušťky patního plechu
Obr. č. 5: Provádění UZ kontroly tloušťky patního plechu pomocí přístroje SONIC 1200 HR (vlevo) a detailní pohled na zobrazované echo ultrazvukového impulsu (vpravo)
Byl zvolen trojúhelníkový systém měření tloušťky, aby se průměrnou hodnotou vypočtenou z těchto tří měření postihla tloušťka materiálu ve zvolené rovině. Výsledky měření neprokázaly výrazné snížení tloušťky. Rozdíly naměřených hodnot bylo možné přisuzovat výrobní toleranci či nerovnoměrnému vybroušení jednotlivých zkušebních míst, kdy při dané citlivosti UZ přístroje nebylo možné provést jejich stejnoměrné zbroušení. UZ přístroj SONIC 1200 HR umožňuje ve svém nastavení měřit tloušťku patního plechu s přesností na 0,001 mm, což je dostačující citlivost pro spolehlivé určení i malého úbytku materiálu vlivem koroze. Průměrná odchylka měření na všech ocelových zásobnících se pohybovala v řádu 0,025 mm.
4. Závěr
V prezentovaných příkladech inspekce kontroly kvality vybraných částí ocelových konstrukcí nebyly prokázány vady vzniklé při realizace staveb či během životnosti konstrukcí působením okolních vlivů. Byla prokázána vhodnost využití zvoleného ultrazvukového přístroje a to s více než dostatečnou přesností měření. V obou případech bylo doporučeno provádění kontroly kvality ocelových šroubů i tloušťky patních plechů ve vhodně zvolených časových intervalech z důvodu sledování možných změn.
5. Poděkování
Článek byl vytvořen v rámci řešení projektu č. LO1408 „AdMaS UP – Pokročilé stavební materiály, konstrukce a technologie“ podporovaného Ministerstvem školství, mládeže a tělovýchovy v rámci účelové podpory programu „Národní program udržitelnosti I“.
Reference
- KOPEC B. a spol.: Nedestruktivní zkoušení materiálů a konstrukcí, Akademické nakladatelství CERM, s.r.o, Brno 2008.
- OBRAZ J.: Zkoušení materiálu ultrazvukem, SNTL Nakladatelství technické literatury, Praha 1989.
- ČSN EN 14127, Nedestruktivní zkoušení – Měření tloušťky ultrazvukem, 2011.
- HOBST L.; VÍTEK L.; LÁNÍK J.; KOUDELKA M.: Posouzení možnosti použití ultrazvukových tloušťkoměrů pro stanovení délky ocelových kotev do betonu, Beton TKS, ISSN 1213-3116, Praha, 2011.
- HOBST, L.; VÍTEK, L.; KOUDELKA, M.; LÁNÍK, J. Využití ultrazvukové impulsní metody ve stavební praxi. In 6. seminár – Sanácia betónových konštrukcií. Materiály pro stavbu. Bratislava: SZSI, 2009. s. 55–59. ISBN: 978-80-227-3215-4.
- KOMÁRKOVÁ T., NDT kontrola zabudovaných kotev do betonu, Diplomová práce, VUT FAST, Brno 2012.
Diagnostics of building structures are used in non-destructive and destructive methods for evaluation of selected properties of building materials. Structural elements but also selected parts are assessed. Ultrasonic method, which is among the non-destructive testing methods, is being used for the diagnosis of concrete and steel structures for many years. The paper presents possibilities of carrying out inspections of selected elements of steel structures.