Možnost efektivního využití druhotných surovin v technologii výroby pískového pórobetonu
Použitím vhodných druhotných surovin je možné snížit objemovou hmotnost pórobetonu při zachování fyzikálně-mechanických vlastností, např. pevnosti. Díky tomu se sníží celková hmotnost konstrukce a je možné širší využití například při aplikacích materiálu za účelem snížení zatížení nenosných stěn nebo u nadstaveb domů. Zkoumáno bylo především využití 10%, 30% a 50% příměsi fluidních úletových i ložových popelovin a škváry, vzniklé při vysokoteplotním spalování v pórobetonu. Pórobeton s příměsí druhotných surovin byl ošetřován v hydrotermálních podmínkách autoklávu při 7hodinové izotermní výdrži na 190 °C. Výsledky ukázaly, že množství příměsi fluidního úletového a ložového popele i škváry má vliv na reologické vlastnosti. Výzkum ukázal, že 10% využití příměsi druhotných surovin výrazně neovlivní fyzikální vlastnosti vzorků.
1. Úvod
Pórobeton díky své pórové struktuře řadíme mezi lehké stavební materiály a je tedy vhodný například pro rekonstrukce bytových jednotek, nadstavby rodinných domů, pro vytváření protipožární ochrany. Konkurencenční prostředí velkých firem vytváří tlak na co nejnižší výrobní náklady při nezměněné kvalitě produktů. To vede v poslední době k tendencím částečně nahrazovat primární suroviny surovinami druhotnými, technologie a výrobní procesy přitom zůstávají zachovány. Ke snížení nákladů spojených s výrobou je také vhodné zkrácení doby autoklávování, které je po ekonomické stránce velmi nákladné. Pro efektivní využití druhotných surovin bylo vhodně využito spolupráce Vysokého učení technického v Brně s Vysokou školou Báňskou, konkrétně Ing. Majstríkovou při společném řešení studie využití druhotných surovin v cementové matrici.
Popílky jsou nejjemnější zbytky ze spalování uhlí, které jsou zachycovány v odlučovačích. Dosahují zrnitosti 0,001–1 mm. [1] Popílek je heterogenní směs částic jenž se liší tvarem, velikostí a chemickým složením. [3][4] Při klasickém vysokoteplotním spalování vzniká vedle popílku také škvára. Škvára je hrubší frakce a podle dosavadních studií při náhradě křemičitého písku škvárou dochází k vytváření většího množství tobermoritu, díky pucolánové aktivitě. [2][5]
Fluidní ohniště spalují drcené palivo vnášené vzestupným proudem spalovacího vzduchu a vznikajících spalin tak, že zrna paliva se vyhoříváním postupně zmenšují. Vznikající popílek je vynášen do určité výšky, kdy vlivem rozšiřujícího se průřezu ohniště poklesne rychlost nosného média na hodnotu rychlosti vznosu. Částice neustále víří kolem své rovnovážné polohy. Tuhé zbytky po spálení se nesmí spékat, to znamená, že musí mít maximální teplotu nižší než je teplota měknutí popelovin. Spalování probíhá při teplotách okolo 850 °C. Ve fluidním ohništi vznikají fluidní popílky, které se dělí podle jemnosti na úletový popílek a ložový popel. U fluidního popílku nedochází k protavování popílkových částic, zrna zůstávají porézní, mají vrstevnatou strukturu, velký měrný povrch. Fluidní popílky obsahují větší množství SO3, který je zejména ve formě anhydritu. Ten má podobné vlastnosti jako sádrovec a z toho důvodu teoreticky není potřeba do pórobetonu s fluidním popílkem sádrovec přidávat. Oxid vápenatý obsažený v popílku je v reaktivní podobě CaO a v nereaktivní podobě CaSO4 ve vztahu k hydrotermální reakci. Obsahuje také reaktivní minerální fázi, což se může projevit pucolánovými vlastnostmi fluidních popílků. [2][6][7][8]
2. Materiály a metody
Mezi primární suroviny patří vápno, cement a písek. Pro přípravu vzorků byl použit cement CEM I 52,5 N. Je to portlandský cement s obsahem slínku 95–100 % a obsahem doplňujících složek 0–5 %. Použité vápno je označeno podle ČSN EN 459-1 „Stavební pálené vápno“ CL 90-Q (R5, P1). Křemičitý písek má dle chemického složení vyšší podíl alkálií, ale dostatečné množství oxidu křemičitého (92,91 % hmot.). Fluidní úletový popílek vzniká v teplárně při fluidním spalování a obsahuje vysoký obsah oxidu hlinitého, oxidu železitého a oxidu vápenatého.
Fluidní ložový popel a škvára mají zrna velikosti 0–8 mm. Z toho důvodu byly mlety v kulovém mlýně na požadovaný měrný povrch cca 300 m2/kg. Daný měrný povrch byl stanoven na základě jemnosti písku, používaného standardně při výrobě pórobetonu. Na surovinách bylo stanoveno chemické složení (viz Tab. 1), měrná hmotnost, měrný povrch a nasákavost (viz Tab. 2).
Druhotné suroviny | Chemické složení [%] | ||||
---|---|---|---|---|---|
SiO2 | CaO | Na2O | Al2O3 | SO3 | |
Fluidní úletový popílek | 38,05 | 17,76 | 0,30 | 24,67 | 5,44 |
Fluidní ložový popel | 38,40 | 12,99 | 0,39 | 24,60 | 5,40 |
Škvára | 51,00 | 4,37 | – | 22,44 | 1,11 |
Druhotné suroviny | Měrná hmotnost [kg/m3] | Měrný povrch [m2/kg] | Nasákavost [%] |
---|---|---|---|
Fluidní úletový popílek | 2 740 | 390 | 192,9 |
Fluidní ložový popel | 2 510 | 250 | 130,0 |
Škvára | 2 610 | 298 | 35,3 |
Referenční receptura kopíruje recepturu, používanou v současné době v reálné technologii výroby autoklávovaného pórobetonu. Tato receptura byla modifikována přídavkem 10 %, 30 % a 50 % příměsi druhotné suroviny. Vodní součinitel byl stanoven na základě požadované velikosti rozlití, tak aby spadala do třídy F1, konkrétně 250 mm.
Suroviny | Množství [kg/m3] |
---|---|
Vápno | 40 |
Cement | 60 |
Písek | 371 |
Sádrovec | 13 |
Hliníkový prášek | 0,450 |
Plastifikační přísada | 0,396 |
Příprava vzorků probíhala tak, že do předehřátého pískovo síranového kalu (40 ± 1) °C byla přidána plastifikační přísada a směs byla mísena po dobu 5 sekund. Předem zhomogenizované vápno, cement a druhotná surovina byly dávkovány do míchačky společně s kalem a byly míseny po dobu 45 sekund. Poté byly setřeny stěny míchačky a nadávkována hliníková suspenze. Směs byla dále mísena po dobu 60 sekund. Celé míchání netrvalo déle jak 120 sekund. Čerstvá surovinová směs byla dávkována do forem. Zrání vzorků probíhalo v laboratorní sušárně při 40 °C po dobu 24 hodin. Poté byly vzorky odformovány.
Autoklávování vzorků probíhalo v laboratorním autoklávu při 7hodinové izotermní výdrži 190 °C. Teplota rozpustnosti křemičitého písku při hydrotermálních podmínkách je 180 °C. Pro zaručení vhodných hydrotermálních podmínek i v jádru vzorku je zvolena teplota výdrže 190 °C. Tvorba tobermoritu a vytvrzení směsi je závislá kromě teploty také na době autoklávování. Zvolená 7hodinová doba se opírá o reálnou průmyslovou technologii výroby. Teplotní průběh celého autoklávovacího procesu je znázorněn na Obr. 1.
4. Výsledky a diskuze
Reologie
Na základě dosažených výsledků je možné říci, že největší spotřebu záměsové vody má směs s obsahem fluidního úletového popílku, což je způsobeno jeho vysokou nasákavostí a velkým obsahem volného oxidu vápenatého.
Přídavek ložového popele má podobný vliv na konzistenci směsi jako přídavek fluidního úletového popílku. Je to dáno jejich podobnou mírou nasákavosti, která má u těchto surovin hodnotu přes 100 %. Podle předpokladu bylo ověřeno, že s rostoucím množstvím příměsi (při zachovaném množství záměsové vody) klesá hodnota rozlití směsi.
Ukázalo se, že přídavek škváry nemá prokazatelný vliv na reologii směsi. S rostoucím množstvím příměsi zůstává spotřeba záměsové vody stejná. Je to způsobeno nízkou nasákavostí škváry, která má uzavřenou, nepórovitou strukturu.
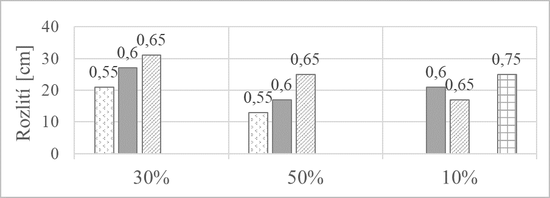
Obr. 2: Závislost rozlití pórobetonové směsi s příměsí fluidního úletového popílku na vodním součiniteli
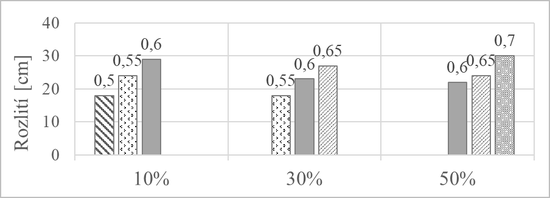
Obr. 3: Závislost rozlití pórobetonové směsi s příměsí fluidního ložového popele na vodním součiniteli
Z výsledků lze říci, že výslednou konzistenci směsi neovlivňuje pouze množství záměsové vody, ale je závislá i na měrném povrchu, nasákavosti a chemickém složení použité příměsi. Při vyšším obsahu oxidu vápenatého dochází k tomu, že část vody vstupuje do procesu hydratace, přitom dochází k nárůstu teplot směsi, což má na konzistenci také patrný vliv.
Pevnosti
Na Obr. 3 jsou znázorněny hodnoty pevností v tlaku a koeficient konstruktivnosti vzorků s 10 %, 30 % a 50 % obsahem druhotných surovin. Pevnost v tlaku byla stanovována podle normy ČSN 73 1350 „Zkoušení pórobetonu“. Koeficient konstruktivnosti vyjadřuje poměr mezi pevností v tlaku (fc) a objemovou hmotností (OH) vzorků. Koeficient je značen Kk a je vypočítán podle rovnice:
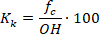
Vzorky s 10% příměsí fluidního úletového popílku dosahují o 13 % nižší koeficient konstruktivnosti a o 10 % nižší pevnosti v tlaku oproti referenčním vzorkům. S rostoucím podílem příměsi druhotné suroviny se pevnost v tlaku a koeficient konstruktivnosti snižuje. Při přídavku 30% příměsi se snižuje pevnost o 32 % a při 50% dávce příměsi klesne pevnost až o 70 %.
Při 7hodinovém autoklávování dosáhly vzorky s 10 % příměsi fluidního ložového popele srovnatelné pevnosti i koeficientu konstruktivnosti jako referenční vzorek. Koeficient konstruktivnosti je v tomto případě o 2 % nižší a pevnost v tlaku poklesla jen o 0,1 MPa u nejnižší, tzn. 10% příměsi ložového popele. Při dávce 30 % příměsi ložového popele je pevnost v tlaku nižší o 32 %. Vzorek s podílem 50 % příměsi ložového popele dosáhl o 75 % nižší pevnosti v tlaku.
Při 10% dávce příměsi ložového popele jsou pevnosti vzorků stejné jako u referenčního vzorku a u 10% přídavku příměsi úletového popílku klesly pouze o 10 %. Při vyšším množství příměsí tobermorit hůře krystalizuje, to je pravděpodobně způsobeno vyšší reaktivitou oxidu křemičitého, který nemá dostatek hydroxidu vápenatého pro reakci. S hůře vykrystalizovaným tobermoritem v těchto vzorcích souvisí nízké pevnosti vzorků, které se snížili až o 75 % oproti referenčnímu vzorku.
Vzorek s 10 % příměsi škváry dosáhl až o 9 % vyšší pevnosti v tlaku než referenční vzorek. Při vyšších dávkách příměsi již pevnost razantně klesá. Při 30% dávkování příměsi pevnost klesá o 37 % oproti referenčnímu vzorku a při 50% množství příměsi klesá o 53 %. Vzorek s příměsí škváry dosáhl vyšších pevností díky vysokému obsahu oxidu křemičitého. Na rozdíl od fluidních popelů vzniká škvára při teplotě nad 1000 °C a vznikají zrna slinutá a méně reaktivní. Nižší reaktivita způsobila nárůst pevností, protože měl vzorek vhodnější poměr oxidu křemičitého a hydroxidu vápenatého vstupujících do reakce.
Mineralogické složení
Mineralogické složení vzorků je zkoumáno prostřednictvím RTG difrakční analýzy (viz Tab. 4).
Vzorek | Intenzita difraktovaného záření nejintenzivnější linie minerálu tobermoritu [–] | ||
---|---|---|---|
REF | 9 700 | ||
Fluidní úletový popílek | 10 % | 9 900 | 10 100 |
30 % | 8 150 | 8 500 | |
50 % | 6 400 | 8 500 | |
Fluidní ložový popel | 10 % | 9 700 | 10 000 |
30 % | 8 000 | 8 800 | |
50 % | 7 150 | 8 100 | |
Škvára | 10 % | 8 150 | 8 500 |
30 % | 8 000 | 8 300 | |
50 % | 7 600 | 8 200 |
Ve vzorcích byla sledována intenzita difraktovaného záření nejintenzivnější linie minerálu tobermoritu. Vyšší intenzita svědčí o lepší krystalické struktuře minerálu. U vzorku s 10% příměsí fluidního úletového popílku dosahuje nejintenzivnější linie tobermoritu vyšší intenzity než u referenčního vzorku. S vyšší dávkou fluidního úletového popílku naopak intenzita klesá.
Vzorek s 10% podílem příměsi fluidního ložového popele dosáhl také vyšší intenzity nejintenzivnější linie tobermoritu než referenční vzorek. Stejně jako u fluidního úletového popílku s vyšší příměsí fluidního ložového popele intenzita píku tobermoritu výrazně klesá.
Z toho vyplývá, že použití fluidních úletových a ložových popelovin je výhodné v množství 10 %. Toto množství fluidního úletového a ložového popele má pozitivní vliv na vznik tobermoritu. Fluidní úletové a ložové popeloviny jsou tvořeny hlinitokřemičitými porézními zrny, která jsou amorfní. Díky tomu tyto popílky velmi dobře reagují s hydroxidem vápenatým při hydrotermálním ošetření za vzniku tobermoritu. Ve fluidních popílcích se také vyskytuje větší množství oxidu hlinitého, který také vznik tobermoritu podporuje.
Vzorek s příměsí škváry dosáhl nižší intenzity difraktovaného záření na nejintenzivnější linii minerálu tobermoritu než referenční vzorek. Na rozdíl od fluidních popílků ale intenzita nejintenzivnější linie tobermoritu s vyšší příměsí škváry klesá nepatrně. Jak již bylo řečeno, zrna popílku jsou méně reaktivní a proto při vyšší příměsi vzorek nevykazuje razantní zhoršení krystalizace tobermoritu, ale ani ji výrazně nezvyšuje.
4. Závěr
Výzkum prokázal, že při výrobě pórobetonu je možné využití fluidních popelovin a škváry z vysokoteplotního spalování. Nejvyšší pevnosti dosáhl vzorek s 10% příměsí škváry. Vzorky s příměsí škváry dosáhly vyšších pevností než referenční vzorek při zachování objemových hmotností. Vzorky s 10% příměsí fluidních úletových a ložových popelovin dosáhly srovnatelných pevností s referenčním vzorkem. Míra krystalizace tobermoritu je u vzorku s 10% příměsí fluidních popelovin také srovnatelná s referenčním vzorkem.
Lze tedy říct, že je možné využití přídavku následujících druhotných surovin, aniž by došlo ke změně fyzikálních parametrů ve srovnání s referenčním vzorkem:
- 10% příměs fluidního úletového popílku,
- 10% příměs fluidního ložového popele,
- 10% příměs škváry.
Další experimentální vývoj bude směřovat ke zkoušení dalších nových druhů druhotných surovin a jejich kombinace pro dosažení maximální náhrady primárních surovin. Jedno z dalších zaměření budoucího výzkumu bude spočívat ve sledování vlivu reologických vlastností na makrostrukturu vzorků.
5. Poděkování
Článek byl vytvořen v rámci řešení projektu č. LO1408 „AdMaS UP – Pokročilé stavební materiály, konstrukce a technologie“ podporovaného Ministerstvem školství, mládeže a tělovýchovy v rámci účelové podpory programu „Národní program udržitelnosti I“ a současně byl podpořen z finančních prostředků státního rozpočtu prostřednictvím Ministerstva průmyslu a obchodu ČR v rámci projektu FV10284 s názvem „Pokročilá technologie pískového pórobetonu s podílem druhotných surovin a efektivnějším využitím přírodních zdrojů“.
6. Literatura
- DROCHYTKA, R. Pórobeton, VUTIUM Brno, 1999.
- FEČKO, P. Popílky, Vysoká škola báňská Technická univerzita Ostrava, 2003.
- BENSCHEIDT, N.; HELA, R. Příručka Popílek v betonu: základy výroby a použití, ČEZ Energetické produkty vydává pro ASVEP Hostivice, 2013.
- KURAMA, H. & kol. Properties of the autoclaved aerated concrete produced from coal bottom ash, Journal of Materials Processing Technology, 2009, DOI: 10.1016/j.jmatprotec.2008.02.044.
- MOSTAFA, N. Y. Influence of air-cooled slag on physicochemical properties of autoclaved aerated concrete, Cement and Concrete Research, 2005, DOI: 10.1016/j.cemconres.2004.10.011.
- KNĚZEK, J. Ekologické a ekonomické zpracování průmyslových odpadních materiálů, Výzkumný ústav stavebních hmot Brno, 2012.
- SONG, Y. & kol. Effect of autoclave curing on hydration of anhydrite in CFBC fly ash, Magazine of concrete research, 2015, DOI: 10.1680/macr.14.00117.
- SONG, Y. & kol. Effect of the Ca-to-Si ratio on the properties of autoclaved aerated concrete containing coal fly ash from circulating fluidized bed combustion boiler, Construction and Building Materials, 2015, DOI: 10.1016/j.conbuildmat.2015.02.077.
Using the appropriate secondary raw materials, it is possible to reduce the bulk density of AAC while preservation the physical-mechanical properties, e.g. strength. This reduces the total weight of the construction and allows for wider use, for example, in the application of material to reduce the load on non-load-bearing walls or to increase floor levels. Research is focused on the use of 10%, 30% and 50% admixture of fluidized bed combustion ashes and slag in the AAC. AAC was developed in the hydrothermal conditions of the autoclave at 7 hours of isothermal soak at 190 °C. The results showed the dependence of the rheological properties on the amount of admixture of fluidized bed combustion fly and bottom ash, slag. Research has shown that the use of 10% admixture of secondary raw materials will not significantly affect the physical properties of the samples.