Ověření vlastností betonů s obsahem recyklovaného betonového kameniva z dvoufázové recyklace
Využití betonového odpadu jako kameniva nebo příměsi do betonu se stává jedním z nejefektivnějších přístupů k recyklaci stavebních a demoličních odpadů. Hlavním cílem výzkumu bylo nalezení betonové směsi s RBK, která bude mít srovnatelné vlastnosti s běžně využívanou směsí pro výrobu panelů pro dopravní stavby.
1. Úvod
Beton, který je zcela závislý na přírodních surovinách, je vzhledem ke svým vlastnostem nejpoužívanějším stavebním materiálem, jehož produkce se ročně pohybuje kolem 10 miliard tun [1]. Tyto skutečnosti vedou k nadměrnému čerpání přírodních zdrojů a zároveň k velkým objemům odpadního betonu, který tvoří kolem 40 % stavebních a demoličních odpadů [2]. Využití betonového odpadu jako kameniva nebo příměsi do betonu se tímto stává jedním z nejefektivnějších přístupů k recyklaci stavebních a demoličních odpadů.
Požadavky na vlastnosti recyklovaného betonového kameniva (RBK) a možnosti náhrady hrubé frakce přírodního kameniva (PK) v betonech recyklovaným jsou stanoveny v českých normách [3, 4]. Tyto normy zohledňují zkušenosti z mnohaletých výzkumů vlastností RBK a jeho vlivu na vlastnosti betonu. Využití hrubé frakce betonového recyklovaného kameniva většinou vede ke zhoršení všech vlastností betonu, bylo tak stanoveno, že maximální možná náhrada je 30 % [5, 6] nebo 50 % [5, 7] v závislosti na kvalitě betonového recyklovaného kameniva a expoziční třídě betonu.
Přestože norma umožňuje maximálně 50% náhradu hrubého kameniva, existují studie, kde se nahrazuje 100 % hrubé frakce betonovým recyklovaným kamenivem [8–10]. Jak již bylo zmíněno, při vyšší náhradě hrubého přírodního kameniva betonovým recyklovaným kamenivem dochází ke zhoršení vlastností a tím nesplnění požadavků pro potřebnou třídu betonu. Řešením může být využití betonového prachu, který vzniká jako prach při drcení betonu, jako příměsi do betonové směsi s recyklovaným kamenivem. Při využití betonového prachu do velikosti částic cca 1 mm jsou lépe vyplněny póry mezi hrubým kamenivem, což zaručuje hutnější beton, a tím jeho lepší vlastnosti [11]. Dále se mohou v této nejjemnější frakci vyskytovat částečky nezhydratovaného cementu, což je další aspekt, který může pozitivně ovlivnit vlastnosti betonů s betonovým recyklovaným kamenivem.
Hlavním cílem tohoto výzkumu bylo nalezení betonové směsi s RBK, která bude mít srovnatelné vlastnosti s běžně využívanou směsí pro výrobu panelů pro dopravní stavby. Všechny směsi byly vyrobeny v betonárně. Byly testovány směsi s různými typy RBK, různými náhradovými poměry, množstvím cementu a vodním součinitelem pro nalezení optimální receptury pro výrobu panelů.
2. Materiály a metody
Vlastnosti betonových směsí byly vyvíjeny ke konkrétnímu využití, a to je železobetonový panel pro využití v dopravním stavitelství. Jako referenční směs (REF) byla zvolena směs provozovatele betonárny, ve které byly navržené směsi vyrobeny. Směsi obsahující RBK byly navrženy dle vlastností předchozích směsí vyrobených v laboratoři a při návrhu směsí byly zohledněny vlastnosti RBK.
Pro laboratorní testování směsí s RBK byly použity dva typy RBK z dvoufázové recyklace, označené jako RBK 1 a RBK 2. Laboratorní zkoušky ukázaly horší vlastnosti RBK v porovnání s přírodním kamenivem, složení materiálů odpovídá recyklovanému kamenivu typ A, které je možné v omezené míře použít do betonu. Více o vlastnostech použitých RBK pojednává článek s názvem Ověření vlastností recyklovaného betonového kameniva z dvoufázové recyklace.
2.1 Vlastnosti betonových směsí s recyklovaným betonovým kamenivem
Bylo navrženo celkem osm betonových směsí, z nichž jedna byla referenční a sedm směsí obsahovalo různé množství RBK. Ve dvou směsích byl jako minerální příměs využit betonový odprach vznikající při drcení betonu. Všechny směsi obsahovaly cement CEM I 42,5 R. Efektivní vodní součinitel nepočítá s vodou, která byla použita pro přednasáknutí recyklovaného kameniva. Množství této vody se stanoví z nasákavosti daného kameniva a aktuálního obsahu vody v kamenivu. Na směsích byly ověřeny fyzikální, mechanické vlastnosti a odolnost vůči zmrazovacím a rozmrazovacím cyklům. Pevnost v tlaku byla zkoušena na 5 krychlích o hraně 150 mm, moduly pružnosti a pevnost v tahu za ohybu byla zkoušena na 3 trámcích o rozměrech 100×100×400 mm. Mrazuvzdornost byla ověřena na 3 trámcích o rozměrech 100×100×400 mm, které byly umístěny do mrazícího zařízení s cyklováním. Na vzorcích byl měřen dynamický modul pružnosti po 0, 25, 50 a 100 cyklech a pevnost v tahu za ohybu po 100 cyklech. Kvůli ověření dosavadních poznatků o betonech s RBK v praxi byly všechny směsi vybetonovány ve spolupracujícím recyklačním středisku a betonárně. Zkoušené směsi jsou uvedeny v tabulce (Tabulka 1), kde rozdílné barvy značí různé množství cementu ve směsi.
Vyrobeny byly následující směsi. Navržené receptury jsou uvedeny v tabulce (Tabulka 1):
- Směs REF 350/0 – obsahovala pouze přírodní kamenivo frakcí 0–4 a 4–8 mm, 350 kg cementu, vodní součinitel této směsi byl 0,55.
- Směs REC 260/46 – obsahovala přírodní kamenivo frakce 0–4 mm a 50 % RBK frakce 4–8 a 8–16 mm, 260 kg cementu, vodní součinitel této směsi byl 0,65.
- Směs REC 300/27 – obsahovala přírodní kamenivo frakce 0–4 mm a 30 % RBK frakce 4–8 a 8–16 mm, 300 kg cementu, vodní součinitel této směsi byl 0,55.
- Směsi REC 350/72 F a REC 320/72 F – obsahovaly přírodní kamenivo frakce 0–4 mm a 100 % RBK frakce 4–8 a 8–16 mm a betonový odprach jako minerální příměs, 350 kg resp. 320 kg cementu, vodní součinitel byl 0,45 resp. 0,50.
- Směsi REC 320/60, REC 320/80, REC 320/100 – obsahovaly 100 % RBK, přírodní kamenivo 0–4 mm bylo nahrazeno jemným RBK 1, to v poměrech 0, 60 a 100 %, 320 kg cementu, vodní součinitel 0,5.
REF 350/0 | REC 260/46 | REC 300/27 | REC 350/72F | REC 320/72F | REC 320/60 | REC 320/80 | REC 320/100 | |
---|---|---|---|---|---|---|---|---|
Voda | 190 | 206 | 197 | 209 | 214 | 191 | 202 | 213 |
Cement | 350 | 260 | 300 | 350 | 320 | 320 | 320 | 320 |
PK (0–4 mm) | 882 | 611 | 597 | 492 | 485 | 725 | 354 | 0 |
PK (4–8 mm) | 773 | 0 | 0 | 0 | 0 | 0 | 0 | 0 |
PK (8–16 mm) | 0 | 311 | 691 | 0 | 0 | 0 | 0 | 0 |
RBK (0–4 mm) | 0 | 0 | 0 | 163 | 191 | 0 | 483 | 917 |
RBK (4–8 mm) | 0 | 506 | 485 | 450 | 454 | 398 | 261 | 165 |
RBK (8–16 mm) | 0 | 283 | 197 | 646 | 622 | 632 | 661 | 681 |
Vodní součinitel | 0,55 | 0,79 | 0,66 | 0,60 | 0,67 | 0,60 | 0,63 | 0,67 |
Efektivní vodní součinitel | 0,55 | 0,65 | 0,55 | 0,45 | 0,50 | 0,50 | 0,50 | 0,50 |
2.1.1 Fyzikální vlastnosti ztvrdlého betonu
Objemová hmotnost
Nejvyšší objemovou hmotnost má referenční beton (viz Tabulka 2). Maximální pokles objemové hmotnosti je 10 % pro směsi obsahující 100 % recyklovaného kameniva. Všechny směsi splňují požadavek pro hutné betony na minimální objemovou hmotnost 2000 kg/m3.
Kapilární nasákavost
V grafu (Obrázek 1) je znázorněna kapilární nasákavost betonů. Výsledky ukazují závislost kapilární nasákavosti na náhradovém poměru, závislost není lineární, ale ukazuje vzrůstající trend se zvyšujícím se náhradovým poměrem. Směsi s RBK mají až dvounásobnou kapilární nasákavost než REF (Tabulka 2).
Směs | Objemová hmotnost [kg/m3] | Kapilární nasákavost [kg/m2] | Třída betonu | ||
---|---|---|---|---|---|
hodnota | σ | hodnota | σ | ||
REF 350/0 | 2264 | 6,01 | 5,18 | 0,04 | C16/20 |
REC 260/46 | 2135 | 28,33 | 5,22 | 0,38 | C12/15 |
REC 300/27 | 2180 | 29,95 | 2,43 | 0,14 | C16/20 |
REC 350/72F | 2117 | 9,52 | 7,32 | 0,53 | C12/15 |
REC 320/72F | 2109 | 10,87 | 10,39 | 0,19 | C8/10 |
REC 320/60 | 2137 | 24,82 | 9,88 | 0,98 | C12/15 |
REC 320/80 | 2083 | 13,76 | 6,23 | 0,18 | C16/20 |
REC 320/100 | 2044 | 11,53 | 7,76 | 1,37 | C8/10 |
2.1.2 Mechanické vlastnosti ztvrdlého betonu
Naměřené hodnoty ve stáří 28 dní jsou včetně směrodatných odchylek uvedeny v souhrnné tabulce (Tabulka 3).
Směs | Pevnost v tlaku [MPa] | Pevnost v tahu za ohybu [MPa] | Modul pružnosti v tlaku [GPa] | Třída betonu | ||||||
---|---|---|---|---|---|---|---|---|---|---|
statický | dynamický | Zmenšovací koeficient [–] | ||||||||
hodn. | σ | hodn. | σ | hodn. | σ | hodn. | σ | |||
REF 350/0 | 29,6 | 2,72 | 7,0 | 0,27 | 31,6 | 0,47 | 38,0 | 1,36 | 0,83 | C16/20 |
REC 260/46 | 19,5 | 0,93 | 3,8 | 0,06 | 26,2 | 1,25 | 29,8 | 2,85 | 0,88 | C12/15 |
REC 300/27 | 25,9 | 1,38 | 5,2 | 0,29 | 30,6 | 1,10 | 40,9 | 2,01 | 0,75 | C16/20 |
REC 350/72F | 18,9 | 0,77 | 4,6 | 0,40 | 19,7 | 0,34 | 23,9 | 1,17 | 0,82 | C12/15 |
REC 320/72F | 13,4 | 0,64 | 3,8 | 0,26 | 15,5 | 0,70 | 21,7 | 1,12 | 0,62 | C8/10 |
REC 320/60 | 19,3 | 1,07 | 4,0 | 0,64 | 24,3 | 3,88 | 26,2 | 1,73 | 0,93 | C12/15 |
REC 320/80 | 22,0 | 0,57 | 5,0 | 0,15 | 22,6 | 0,69 | 24,2 | 2,93 | 0,94 | C16/20 |
REC 320/100 | 15,4 | 0,4 | 4,3 | 0,25 | 16,4 | 0,36 | 22,3 | 1,72 | 0,73 | C8/10 |
Pevnost v tlaku
Pevnost v tlaku byla měřena na krychlích o hraně 150 mm (Obrázek 2). Výsledky ukazují největší pokles pevnosti v tlaku (65 %) v porovnání s referenční směsí pro beton, který obsahoval 100 % hrubé frakce RBK 1 a betonový odprach. Nejmenší pokles (13 %) byl pak pro směs s nejmenším obsahem RBK ve směsi (27 %).
Pevnost v tahu za ohybu
Pevnost v tahu za ohybu byla měřena na trámcích o rozměrech 100×100×400 mm a vykazuje podobný trend jako pevnost v tlaku. Maximální pokles pevnosti v tahu za ohybu je 46 % u směsi s nejnižším množstvím cementu.
Statický a dynamický modul pružnosti
Statický (Obrázek 3) a dynamický modul pružnosti byl měřen na trámcích o rozměrech 100×100×400 mm. Dynamický modul pružnosti byl stanoven ultrazvukovou metodou dle ČSN 73 1371 a ČSN EN 12504-4. Pokles modulu pružnosti směsí s RBK byl v porovnání s referenční směsí do 50 %. Dynamický modul pružnosti koresponduje více s výsledky pevností v tlaku a v tahu za ohybu.

Obrázek 3 Statický a dynamický modul pružnosti betonů s částečnou nebo plnou náhradou hrubé frakce RBK
2.1.3 Trvanlivost ztvrdlého betonu
Mrazuvzdornost
Odolnost betonů vůči zmrazování a rozmrazování byla zkoušena na zkušebních tělesech 100×100×400 mm. Vzorky byly 28 dní ošetřovány ve vodní lázni a před vložením do zkušebního zařízení byly zváženy a byl na nich ultrazvukovou metodou naměřen dynamický modul pružnosti. Na vzorcích bylo po každých 25 cyklech opakováno vážení a měření dynamického modulu pružnosti ultrazvukovou metodou až do celkových 100 cyklů, kde byla na vzorcích, které zatěžování vydržely, ověřena pevnost v tahu za ohybu. Z hodnot dynamického modulu pružnosti před a po zmrazovacích cyklech byl vyhodnocen koeficient mrazuvzdornosti, který se počítá jako poměr dynamického modulu pružnosti naměřeného po příslušném počtu zmrazovacích cyklů a před zmrazováním.
Směs | Dynamický modul pružnosti Ed [GPa] | Koeficient mrazuvzdornosti z dynamického modulu pružnosti [–] | |||||||
---|---|---|---|---|---|---|---|---|---|
0 | 25 | 50 | 75 | 100 | 25 | 50 | 75 | 100 | |
REF 350/0 | 38,0 | 19,2 | 12,0 | 4,3 | 0,0 | 0,50 | 0,32 | 0,11 | 0,00 |
REC 260/46 | 29,8 | 25,1 | 11,6 | 13,4 | 17,6 | 0,84 | 0,39 | 0,45 | 0,59 |
REC 300/27 | 40,9 | 31,0 | 27,2 | 16,9 | 16,0 | 0,76 | 0,66 | 0,41 | 0,39 |
REC 350/72F | 23,9 | 23,1 | 22,6 | 24,2 | 25,0 | 0,96 | 0,95 | 1,01 | 1,05 |
REC 320/72F | 21,7 | 21,9 | 20,0 | 19,2 | 20,9 | 1,01 | 0,92 | 0,88 | 0,96 |
REC 320/60 | 26,2 | 25,0 | 18,0 | 17,4 | 16,2 | 0,95 | 0,69 | 0,66 | 0,62 |
REC 320/80 | 24,2 | 25,0 | 23,2 | 20,8 | 22,3 | 1,03 | 0,96 | 0,86 | 0,92 |
REC 320/100 | 22,3 | 22,2 | 19,9 | 19,4 | 17,8 | 1,00 | 0,89 | 0,87 | 0,80 |
Vyhodnocení bylo provedeno pro dynamický modul pružnosti po 0, 25, 50, 75 a 100 cyklech (Tabulka 4). Výsledné hodnoty byly porovnány s referenčními hodnotami, které byly naměřeny na vzorcích po 28 dnech. Toto vyhodnocení je zde prezentováno jako koeficient mrazuvzdornosti a je stanovena mrazuvzdornost. V tabulce jsou uvedeny hodnoty dynamického modulu pružnosti po každých 25 cyklech až po 100 cyklů.
Výsledky dynamických modulů zkoušených v průběhu zmrazovacích a rozmrazovacích cyklů ukazují u většiny směsí pokles. Koeficient mrazuvzdornosti pro jednotlivé směsi je uveden v grafu (Obrázek 4). Všechny směsi vydržely všech 100 zmrazovacích a rozmrazovacích cyklů.
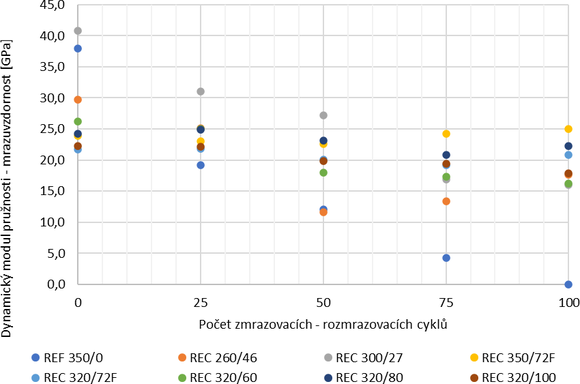
Obrázek 4 Dynamický modul pružnosti měřených na vzorcích v průběhu zmrazovacích a rozmrazovacích cyklů
Vyhodnocení bylo dále provedeno pro pevnost v tahu za ohybu po 0 a 100 cyklech (Tabulka 5). Výsledky pevnosti v tahu za ohybu pro vzorky bylo možné změřit pro všechny směsi, všechny vydržely všech 100 zmrazovacích a rozmrazovacích cyklů. Výsledky pevnosti v tahu za ohybu odpovídají výsledkům dynamických modulů pružnosti měřených v průběhu zmrazovacích a rozmrazovacích cyklů. Jediný rozdíl je u směsi REC 300/27, u které byl pokles dynamického modulu pružnosti o více než 60 %, ale pokles pevnosti v tlaku byl pouze 2 %, a směs je tak dle pevnosti v tahu za ohybu považovaná za mrazuvzdornou pro 10 cyklů. Podmínku mrazuvzdornosti dle ČSN 73 1322 [12] tedy splnilo 5 směsí, a tedy, že pevnost v tahu za ohybu nepoklesla o více než 25 % oproti referenčnímu měření, které bylo provedeno na vzorcích ve stáří 28 dní. U směsi s plnou náhradou hrubé frakce RBK a optimalizovaným poměrem přírodního písku a jemné frakce RBK dokonce došlo k nárůstu pevnosti. Směsi, které byly pro porovnání po dobu zkoušení mrazuvzdornosti uloženy ve vodě (označení 100R) ukazují u většiny směsí nárůst pevnosti v tahu za ohybu. Stáří těchto vzorků byla přibližně 60 dní.
Směs | Mrazuvzdornost – pevnost v tahu za ohybu [MPa] | ||||||
---|---|---|---|---|---|---|---|
Pevnost v tahu za ohybu [MPa] | σ | Koeficient mrazuvzdornosti z pevnosti v tahu za ohybu [%] | |||||
0 | 100 | 100R | 0 | 100 | 100R | ||
REF 350/0 | 7,0 | 0,3 | 7,6 | 0,3 | 0,4 | 0,3 | 4 % |
REC 260/46 | 3,8 | 2,1 | 5,1 | 0,1 | 0,3 | 0,1 | 55 % |
REC 300/27 | 5,2 | 5,1 | 0,0 | 0,3 | 1,1 | 0,0 | 98 % |
REC 350/72F | 4,6 | 4,5 | 5,5 | 0,4 | 0,1 | 0,1 | 98 % |
REC 320/72F | 3,8 | 3,3 | 5,0 | 0,3 | 1,0 | 0,3 | 86 % |
REC 320/60 | 4,0 | 2,6 | 6,0 | 0,6 | 0,8 | 0,1 | 66 % |
REC 320/80 | 5,0 | 6,2 | 5,3 | 0,2 | 0,3 | 0,3 | 124 % |
REC 320/100 | 4,3 | 4,3 | 4,7 | 0,2 | 0,2 | 0,0 | 100 % |
3. Závěr
Tento článek se věnuje možnostem využití recyklovaného betonového kameniva (RBK) jako náhrady přírodního kameniva v betonové směsi a přenesení poznatků z laboratoře do praxe.
V betonárně recyklačního centra byl ověřen technologický postup betonáže směsí s recyklovaným betonovým kamenivem. Byly vyrobeny dvě směsi s částečnou náhradou hrubé frakce recyklovaným betonovým kamenivem (REC 260/46 a REC 300/27), u těchto směsí došlo pouze k nepatrnému zhoršení vlastností oproti běžným betonům, kdy směs REC 300/27 vyhověla požadavku trvanlivosti na 100 zmrazovacích cyklů.
Dále byly vybetonovány dvě směsi, které obsahovaly pouze hrubé RBK a přírodní písek a dále byl použit jemný betonový odprach jako minerální příměs (REC 350/72F a REC 350/72F). U směsí s betonovým odprachem došlo k výraznému zhoršení mechanických vlastností oproti běžným betonům. Obě tyto směsi však vyhověly požadavkům na mrazuvzdornost 100 cyklů.
Tři směsi vznikly pro ověření potenciálu využití drobného recyklovaného kameniva frakce 0–4 mm jako plné nebo částečné náhrady přírodního písku. Všechny směsi obsahovaly pouze hrubé RBK a byl nahrazen písek v 0, 60 a 100 % (REC 320/60, REC 320/80 a REC 320/100). Výsledky ukazují na pozitivní dopad drobného RBK na vlastnosti betonové směsi. Toto kamenivo obsahuje vysoký podíl jemných částic (částice menší než 0,063 mm), ale na rozdíl od jemného betonového prachu vznikají při druhé fázi drcení a neobsahují tak znehodnocující organické látky. Tyto jemné částice naopak pomáhají vylepšovat vlastnosti betonů s hrubým RBK.
Poděkování
Tato práce vznikla za finanční podpory MŠMT v rámci programu NPU I č. LO1605 a TAČR TH02030649 Environmentálně efektivní stavební a demoliční odpad do konstrukcí (EESDOK).
Reference
- BELL, Michael a Craig BUCKLEY. Solid States: Concrete in Transition. B.m.: Princeton Architectural Press, 2010. ISBN 978-1-56898-895-5.
- Produkce, využití a odstranění odpadů – 2016 | ČSÚ [online]. [vid. 2018-03-23]. Dostupné z:
https://www.czso.cz/csu/czso/produkce-vyuziti-a-odstraneni-odpadu - ČSN EN 12620+A1 Kamenivo do betonu. B.m.: CEN. 2008
- ČSN EN 206+A1 Beton – Specifikace, vlastnosti, výroba a shoda. B.m.: CEN. 2018
- VERIAN, Kho Pin, Warda ASHRAF a Yizheng CAO. Properties of recycled concrete aggregate and their influence in new concrete production. Resources, Conservation and Recycling [online]. 2018, 133, 30–49. ISSN 0921-3449. Dostupné z: doi:10.1016/j.resconrec.2018.02.005
- TAM, Vivian W. Y. a C. M. TAM. Assessment of durability of recycled aggregate concrete produced by two-stage mixing approach. Journal of Materials Science [online]. 2007, 42(10), 3592–3602. ISSN 0022-2461, 1573-4803. Dostupné z: doi:10.1007/s10853-006-0379-y
- KOU, Shi-cong, Chi-sun POON a Francisco AGRELA. Comparisons of natural and recycled aggregate concretes prepared with the addition of different mineral admixtures. Cement and Concrete Composites [online]. 2011, 33(8), 788–795. ISSN 0958-9465. Dostupné z: doi:10.1016/j.cemconcomp.2011.05.009
- ZAHARIEVA, Roumiana, François BUYLE-BODIN, Frédéric SKOCZYLAS a Eric WIRQUIN. Assessment of the surface permeation properties of recycled aggregate concrete. Cement and Concrete Composites [online]. 2003, 25(2), 223–232. ISSN 0958-9465. Dostupné z: doi:10.1016/S0958-9465(02)00010-0
- YANG, Jian, Qiang DU a Yiwang BAO. Concrete with recycled concrete aggregate and crushed clay bricks. Construction and Building Materials [online]. 2011, 25(4), 1935–1945. ISSN 0950-0618. Dostupné z: doi:10.1016/j.conbuildmat.2010.11.063
- MARINKOVIĆ, S.B. Life cycle assessment (LCA) aspects of concrete. In: Eco-Efficient Concrete [online]. B.m.: Elsevier, 2013 [vid. 2017-10-01], s. 45–80. ISBN 978-0-85709-424-7. Dostupné z: doi:10.1533/9780857098993.1.45
- KWAN, A. K. H., P. L. NG a K. Y. HUEN. Effects of fines content on packing density of fine aggregate in concrete. Construction and Building Materials [online]. 2014, 61, 270–277. ISSN 0950-0618. Dostupné z: doi:10.1016/j.conbuildmat.2014.03.022
- ČSN 73 1322- Stanovení mrazuvzdornosti betonu. B.m.: UNMZ Praha. 1969
This article deals with the verification of the properties of concrete mixtures with partial or full replacement of natural aggregate with recycled concrete aggregate (RCA) from two-phase recycling. 8 mixtures with different replacement ratios of natural aggregate with RCA were prepared. To verify previous research, test specimens were made at a recycling centre and then tested in the laboratory.