Experimentální ověření betonů s recyklovaným cihelným kamenivem
Tento článek pojednává o možnosti využití cihelného kameniva ze stavebního a demoličního odpadu. V článku jsou shrnuty vlastnosti betonů s laboratorně optimalizovanou recepturou s plnou náhradou přírodního kameniva recyklovaným cihelným kamenivem. Testování betonových vzorků probíhalo podle platných norem. Výsledkem je směs s optimalizovanými vlastnostmi pro výrobu konstrukčních dílců.
1. Úvod
Tento příspěvek se zabývá experimentálním ověřením vlastností betonů s obsahem recyklovaného cihelného kameniva (RCK) ze stavebního a demoličního odpadu (SDO). Využívané RCK je tvořeno převážně cihelnými a keramickými bloky, které pro frakci 4–8 mm tvoří nejméně 58 % a pro frakci 8–16 mm přibližně 50 %. Dalšími zastoupenými materiály jsou beton a malta (12–30 %) a nestmelené přírodní kamenivo (12–32 %). Vlastnosti RCK z roku 2019, podrobně uvedené v předchozím článku s názvem Experimentální ověření vlastností RCK jsou shrnuty v tabulce (Tabulka 1). Se zjištěnými vlastnostmi RCK je počítáno při návrhu receptur betonů s RCK.
RCK 04/2019 | RCK 07/2019 | |||
---|---|---|---|---|
4–8 mm | 8–16 mm | 4–8 mm | 8–16 mm | |
Obsah jemných částic [%] | 1,2 % | 0,5 % | 1,2 % | 0,6 % |
Objemová hmotnost [kg/m3] | 2015 | 2020 | 2000 | 2110 |
Nasákavost [%] | 12,42 | 11,00 | 11,47 | 9,91 |
Mrazuvzdornost [%] | 1,9 | 8,3 | – | – |
Ze studií [1–3] vyplývá, že při náhradě přírodního kameniva (PK) do 15 % nedochází ke ztrátě mechanických vlastností, ty byly patrné až při náhradě vyšší než 30 % [1]. Při náhradě 20 % dojde k poklesu pevnosti v tlaku o 11 % a při 50% náhradě už jsou vlastnosti na 50 % v porovnání s běžným betonem [3]. Oproti tomu v jiné studii byla míra náhrady 100 %. Pro tyto vzorky byl naměřen pokles pevnosti v tlaku v porovnání s běžným betonem o 35 % a pokles modulu pružnosti byl až 50 % [2]. Obdobná studie ukázala pokles pevnosti v tlaku při 100% náhradě PK o 20–30 % a pokles modulu pružnosti o 30–40 %. Všeobecně lze říci, že největší rozdíl mezi běžným betonem a betonem s recyklovaným kamenivem (RK) je u modulu pružnosti.
Z další studie [4] vyplývá, že při nahrazení PK v betonové směsi RCK dochází ke ztrátě odolnosti vůči zmrazování a rozmrazování. Obecně se dá říci, že mrazuvzdornost betonu závisí na typu kameniva, pórovitosti a obsahu vody. U betonů s RK je ovlivněna i náhradovým poměrem PK. Stejně jako u betonů s PK, platí pro betony s RK, že odolnost vůči mrazu se u betonu snižuje s rostoucím vodním součinitelem [5, 6]. Nejčastěji se vyhodnocuje ztráta hmotnosti, dynamický modul pružnosti a ztráta pevnosti. Tím, že má RCK několikanásobně vyšší nasákavost než PK, zůstává v kamenivu voda, která může přispívat ke snížení mrazuvzdornosti betonů s RCK. Další studie [7] ukazuje vliv cementové pasty na povrchu recyklovaného betonového kameniva (RBK), jejích vlastností a množství, na odolnost vůči zmrazování a rozmrazování. Existuje však několik studií, které ukázaly, že v určitých případech můžou betony s recyklovaným kamenivem v daných lokalitách splňovat nastavené podmínky, ve většině případů jde o RBK. Studie [8] ukázala, že při obsahu vzduchu ve směsi do 5 % a vodním součiniteli 0,5 může být mrazuvzdornost betonů v suchém prostředí uspokojivá. Další studie [9, 10] ukazují, že pokud jsou betony navrženy v pevnostních třídách 30 až 50 MPa, splňují požadavek mrazuvzdornosti definovaný v britské normě (BS 5328 Part 1–1991). Mrazuvzdornost betonů s RK je dále možné zlepšit přidáním minerálních příměsí jako je metakaolin nebo popílek [11–13]. Naopak ve studii [6] nebyl prokázán dostatečně pozitivní vliv přidáním mikrosiliky. Všechny zde uvedené studie uvádějí vliv RBK na mrazuvzdornost betonů, v žádné z těchto studií nebylo uvažováno s využitím RCK, nicméně se předpokládá, že vlastnosti kameniva a jeho pórovitost budou mít stejný vliv.
Tento příspěvek prezentuje shrnutí dosavadních laboratorních výsledků experimentálního ověření betonů s RCK prověřených na laboratorně vyrobených betonových vzorcích, vlastnosti vybraných betonových směsí pro betonáž v praxi, a zejména experimentální ověření vzorků betonů s recyklovaným cihelným kamenivem vyráběných v praxi. Pro tyto účely byly vybrány směsi, jejichž složení vychází z předchozího testování laboratorně vyrobených vzorků. Přírodní kamenivo bylo plně nahrazeno jemnou a hrubou frakcí RCK. Směsi byly betonovány ve dvou etapách, takže obsahovaly dva typy RCK, měly různé množství cementu a různé vodní součinitele. Hlavním cílem bylo najít optimální recepturu s ohledem na zpracovatelnost, mechanické vlastnosti a mrazuvzdornost, aby byla vybrána receptura vhodná pro betonáž konstrukčních dílců. Konkrétně se jedná o prvek prefabrikovaných základů pro suchou výstavbu.
2. Materiály a metody
Tato kapitola popisuje zkoušený materiál, kterým byly betonové směsi s plnou náhradou přírodního kameniva RCK ze SDO. Kamenivo bylo vyrobeno a upraveno v recyklačním středisku (RS), kde byly také vybetonovány vzorky pro testování v laboratoři.
Dále tato kapitola shrnuje zkušební metody. Tyto postupy jsou uvedeny v normě ČSN EN 12620 + A1 Kamenivo do betonu [15]. Požadavky na možnosti použití jsou pak uvedeny v normě ČSN EN 206 Beton – Specifikace, vlastnosti, výroba a shoda [16].
2.1 Vlastnosti betonů s RCK
Nejprve byly v laboratorních podmínkách ověřeny vlastnosti betonů s RCK, které ve směsích nahradilo 100 % přírodního kameniva. V roce 2018 bylo ve směsích použito RCK 0–8 a 8–16 mm s 320 kg cementu na m3 a stejný efektivní vodní součinitel 0,5. V roce 2019 všechny směsi obsahovaly frakce 0–4, 4–8 a 8–16 mm a tři různá množství cementu a to 260, 280 a 300 kg/m3 s efektivním vodním součinitelem 0,5; 0,55; 0,60 a 0,65. Na závěr byly vybrány receptury, které byly zkušebně vybetonovány v betonárce RS, tyto směsi jsou v tabulce (Tabulka 2) zvýrazněny šedým podbarvením (a dále jsou označeny písmeny RS v názvu). Označení RECC znamená, že směsi obsahují recyklované cihelné kamenivo, číslice značí množství cementu v 1 m3 směsi a římská číslice odlišuje různé vodní součinitele. Barevně jsou odlišeny směsi s RCK 2018, RCK 04/2019 a RCK 07/2019.
Směs | RECC 320 | RECC 320 I* | RECC 260 | RECC 280 | RECC 260 I | RECC 280 I | RECC 300 I | RECC 260 II | RECC 280 II | RECC 300 II |
---|---|---|---|---|---|---|---|---|---|---|
Voda | 184 | 285 | 295 | 310 | 290 | 275 | 285 | 275 | 288 | 300 |
Cement | 320 | 320 | 260 | 280 | 260 | 280 | 300 | 260 | 280 | 300 |
RCK 0–4 | 529 | – | 792 | 772 | 736 | 717 | 697 | 736 | 717 | 697 |
RCK 4–8 | 188 | – | 92 | 97 | 235 | 241 | 247 | 235 | 241 | 247 |
RCK 0–8 | – | 1363 | – | – | – | – | – | – | – | – |
RCK 8–16 | 772 | – | 664 | 678 | 583 | 596 | 609 | 583 | 596 | 609 |
Efektivní vodní součinitel | 0,50 | 0,50 | 0,65 | 0,65 | 0,60 | 0,50 | 0,50 | 0,55 | 0,55 | 0,55 |
Vodní součinitel | 0,58 | 0,89 | 1,14 | 1,10 | 1,12 | 0,98 | 0,95 | 1,06 | 1,03 | 1,00 |
* Směs obsahuje pouze RCK frakce 0–8 mm |
Dle vybraných receptur byly se shodným složením směsi betonovány vzorky v RS. Článek se dále zabývá pouze těmito směsmi, neboť hlavním cílem bylo ověřit vlastnosti betonových směsí, které lze reálně vyrobit z RCK v praxi, nikoli v laboratoři.
2.2 Návrh receptury betonů s RCK
Všechny navržené směsi obsahovaly pouze RCK, cement a vodu. Návrh zastoupení jednotlivých frakcí RCK byl optimalizován podle Bolomeyovy referenční křivky. Vybrané směsi byly vybetonovány v recyklačním středisku a zkoušeny v laboratoři.
Na následujících fotografiích (Obrázek 1) jsou ukázány jednotlivé betonové směsi. RS značí směs betonovanou v recyklačním středisku, hvězdička směsi, které byly betonované dvakrát při zachování totožné receptury.
Směsi byly navrženy dle ČSN EN 206 se stejným typem, ale různým množstvím, cementu CEM I 42,5 R a různým efektivním vodním součinitelem. Vodní součinitel byl vypočítán jako poměr vody a cementu, kdy pro směsi obsahující RCK bylo počítáno s vodou potřebnou na přednasáknutí kameniva. Ta byla přidána do RCK na základě naměřené nasákavosti a na základě množství vody aktuálně obsažené v kamenivu. Tato voda byla k RCK přidána 10 minut před započetím vlastního míchání. Navržené receptury jednotlivých směsí jsou uvedeny v tabulce (Tabulka 2).
3. Výsledky a diskuse
Vzorky byly během tuhnutí a zrání uloženy a ošetřovány ve stálém prostředí a ve vodní lázni a po 28 dnech byly laboratorními zkouškami stanoveny fyzikální, mechanické, deformační a trvanlivostní vlastnosti.
3.1 Fyzikální vlastnosti
Objemová hmotnost
Objemová hmotnost vzorků skladovaných na vzduchu v prostředí s konstantní relativní vlhkostí a teplotou byla stanovena na krychlích o hraně 150 mm a trámcích 100×100×400 mm ve stáří 28 dní. Z výsledků vyplývá, že objemové hmotnosti všech směsí jsou totožné, rozdíly jsou do 10 %. V tabulce (Tabulka 3) je uvedena průměrná hodnota objemových hmotností 3 trámců a 5 krychlí o hraně 150 mm, včetně směrodatné odchylky.
Z výsledků objemové hmotnosti je patrné, že podmínku pro obyčejný beton (2000 kg/m3) splňuje pouze jedna směs (RECC 320 RS*), a proto je třeba směsi zatřídit jako lehké betony s objemovou hmotností ve vysušeném stavu mezi 600 kg/m3 a 2000 kg/m3, a to do třídy objemové hmotnosti D2,0.
Směs | Objemová hmotnost [kg/m3] | Kapilární nasákavost [kg/m3] | ||
---|---|---|---|---|
Průměr 28 dní | σ | Po 72 h | σ | |
RECC 320 RS* | 2046 | 12,32 | 2,913 | 0,91 |
RECC 320 I RS* | 1980 | 22,21 | 5,860 | 1,26 |
RECC 320 RS | 1965 | 17,23 | 8,007 | 0,96 |
RECC 320 I RS | 1867 | 23,19 | 13,213 | 0,88 |
RECC 300 II RS | 1996 | 9,19 | 4,633 | 0,29 |
RECC 280 II RS | 1960 | 17,87 | 1,187 | 1,84 |
RECC 280 RS | 1904 | 13,04 | 11,460 | 0,72 |
RECC 260 I RS | 1997 | 22,22 | 1,547 | 1,40 |
RECC 260 RS | 1844 | 29,92 | 15,647 | 0,42 |
Kapilární nasákavost
Kapilární nasákavost byla zkoušena na úlomcích trámců (trámce 100×100×400 mm) ve stáří 60 dní. Vzorky byly předtím skladovány na vzduchu v prostředí s konstantní relativní vlhkostí a teplotou. Výsledky měření jsou uvedeny v předchozí tabulce (Tabulka 3) a grafu (Graf 1).
Z výsledků vyplývá, že kapilární nasákavost směsí se pohybuje mezi 1,2 a 16,0 kg/m2, což ukazuje na vyšší rozdíly mezi jednotlivými betony s RCK. Kapilární nasákavost ukazuje závislost na typu použitého kameniva. Typ kameniva zároveň ovlivňuje i objemovou hmotnost, která je pro směsi s vyšší kapilární nasákavostí nižší.
3.2 Mechanické a deformační vlastnosti
Souhrnné výsledky z testování mechanických a deformačních vlastností jsou uvedeny v následující tabulce (Tabulka 4).
Směs | Pevnost v tlaku [MPa] | Pevnost v tahu za ohybu [MPa] | Modul pružnosti v tlaku [GPa] | Třída betonu | ||||||
---|---|---|---|---|---|---|---|---|---|---|
statický | dynamický | Zmenšovací koeficient Ec/Ed [–] | ||||||||
hodn. | σ | hodn. | σ | hodn. | σ | hodn. | σ | [–] | ||
RECC 320 RS* | 23,7 | 0,7 | 5,6 | 0,18 | 19,5 | 0,2 | 21,3 | 8,5 | 0,91 | C16/20 |
RECC 320 I RS* | 20,3 | 0,4 | 5,9 | 0,10 | 16,9 | 0,5 | 24,7 | 1,6 | 0,68 | LC16/18 |
RECC 320 RS | 15,6 | 0,6 | 3,4 | 0,10 | 14,7 | 0,5 | 20,1 | 1,6 | 0,73 | LC12/13 |
RECC 320 I RS | 11,6 | 0,6 | 3,2 | 0,35 | 12,4 | 0,6 | 16,6 | 0,7 | 0,75 | LC8/9 |
RECC 300 II RS | 18,2 | 1,0 | 3,9 | 0,21 | 16,2 | 0,5 | 21,7 | 1,4 | 0,75 | LC12/13 |
RECC 280 II RS | 17,8 | 1,1 | 4,6 | 0,21 | 15,4 | 0,0 | 23,1 | 1,3 | 0,67 | LC12/13 |
RECC 280 RS | 11,7 | 1,2 | 2,6 | 0,52 | 13,8 | 0,4 | 19,4 | 1,3 | 0,71 | – |
RECC 260 I RS | 15,9 | 1,5 | 4,3 | 0,21 | 15,1 | 0,3 | 24,3 | 1,4 | 0,62 | LC8/9 |
RECC 260 RS | 6,5 | 0,5 | 2,8 | 0,05 | N** | N** | 17,2 | 1,0 | – | – |
Pozn. N** – neměřitelné (příliš nízká hodnota mimo toleranci měřicího zařízení) |
Pevnost v tlaku
Zkouška byla prováděna na krychlích 150×150×150 mm ve 28 dnech (viz Tabulka 4 a Graf 2).
Pevnosti v tlaku ukazují závislost na typu RCK, množství cementu a vodním součiniteli. Směsi (RECC 320 RS, RECC 320 I RS, RECC 280 a RECC 260) obsahovaly jiné RCK než ostatní směsi, což je vidět na výsledcích pevnosti v tlaku, kdy všechny tyto směsi měly nižší pevnosti v tlaku v porovnání s ostatními 4 betony. Nejvyšší pevnosti v tlaku měly směsi s 320 kg cementu na m3, obě tyto směsi dosáhly hodnoty vyšší než 20 MPa. Obě tyto směsi je možné dle charakteristické hodnoty pevnosti v tlaku, kde byl zohledněn počet vzorků a směrodatná odchylka výsledných hodnot, zatřídit do pevnostní třídy lehkého betonu LC16/18. Další směsi ukazují závislost na množství cementu a vodním součiniteli. Nejnižší pevnosti měly směsi s prvním typem kameniva, 260 a 280 kg cementu na m3 a vodním součinitelem 0,65. Tyto směsi není možné dle charakteristické hodnoty pevnosti v tlaku zatřídit do pevnostní třídy lehkého betonu. Rozdíly pevnosti v tlaku mezi jednotlivými betony jsou až 75 %.
Pevnost v tahu za ohybu
Pevnost v tahu za ohybu byla zkoušena ve 28 dnech na trámcích o rozměrech 100×100×400 mm zatížených čtyřbodovým ohybem. Naměřené hodnoty jsou uvedeny v tabulce (Tabulka 4).
Pevnosti v tahu za ohybu jsou mezi 2,6 a 5,9 MPa, což znamená rozdíly do 55 %, a tedy nižší než pro pevnost v tlaku. Výsledky pevnosti v tahu za ohybu ukazují závislost na typu RCK a vykazují podobný trend jako pevnost v tlaku.
Statický a dynamický modul pružnosti
Statický a dynamický modul pružnosti byly testovány ve 28 dnech na zkušebních tělesech 100×100×400 mm. Naměřené hodnoty jsou uvedeny v tabulce (Tabulka 4) a v grafu (Graf 3). Moduly pružnosti ukazují, stejně jako pevnost v tlaku, závislost na typu kameniva, množství cementu a vodním součiniteli. Nejnižší statický modul pružnosti měla směs RECC 260 s nejnižším množstvím cementu a s vyšším vodním součinitelem. Tato hodnota byla tak nízká, že nebylo možné ji naměřit. Maximální rozdíl modulů pružnosti v tlaku mezi všemi betony je 45 %.
3.3 Trvanlivost
Mrazuvzdornost
Odolnost betonů vůči zmrazování a rozmrazování byla zkoušena na zkušebních tělesech 100×100×400 mm. Vzorky byly 28 dní ošetřovány ve vodní lázni a před vložením do zkušebního zařízení byly zváženy a UTZ metodou byl stanoven dynamický modul pružnosti. Vzorky byly zkoušeny celkově na 100 zmrazovacích a rozmrazovacích cyklů. Po každých 25 cyklech bylo vážení a stanovení dynamického modulu pružnosti z výsledků UTZ měření opakováno až do celkových 100 cyklů (Tabulka 5). Poté byla na vzorcích, které zatěžování vydržely, ověřena pevnost v tahu za ohybu. Vzorky porušené zmrazovacími a rozmrazovacími cykly jsou ukázány na obrázcích (Obrázek 2). Vzhledem k výsledkům mechanických a deformačních zkoušek pro směs RECC 260 RS bylo rozhodnuto, že na vzorcích této směsi již nebudou měřeny trvanlivostní vlastnosti.
Obrázek 2 Vzorky po zatěžování zmrazovacími a rozmrazovacími cykly
Směs | Dynamický modul pružnosti Ed [GPa] | Index mrazuvzdornosti z dynamického modulu pružnosti [%] | ||||||||||
---|---|---|---|---|---|---|---|---|---|---|---|---|
0 | 25 | 50 | 75 | 100 | 100R | 0 | 25 | 50 | 75 | 100 | Mrazuvzdornost | |
RECC 320 RS* | 28,8 | 14,1 | 12,4 | 10,8 | 9,1 | 26,4 | 100 | 49 | 43 | 37 | 32 | 0 cyklů |
RECC 320 I RS* | 24,4 | 18,9 | 18,4 | 19,5 | 21,6 | 22,9 | 100 | 78 | 76 | 80 | 88 | 100 cyklů |
RECC 320 RS | 19,8 | 10,7 | 8,0 | 1,8 | 0,0 | 24,9 | 100 | 54 | 40 | 9 | 0 | 0 cyklů |
RECC 320 I RS | 17,1 | 2,2 | 0,0 | 0,0 | 0,0 | 19,3 | 100 | 13 | 0 | 0 | 0 | 0 cyklů |
RECC 300 II RS | 20,6 | 21,4 | 19,8 | 19,8 | 20,2 | 20,3 | 100 | 104 | 96 | 96 | 98 | 100 cyklů |
RECC 280 II RS | 17,0 | 8,4 | 7,3 | 0,0 | 0,0 | 21,2 | 100 | 49 | 43 | 0 | 0 | 0 cyklů |
RECC 280 RS | 20,0 | 6,3 | 2,7 | 0,0 | 0,0 | 22,8 | 100 | 31 | 13 | 0 | 0 | 0 cyklů |
RECC 260 I RS | 22,4 | 6,3 | 4,5 | 0,0 | 0,0 | 24,9 | 100 | 28 | 20 | 0 | 0 | 0 cyklů |
RECC 260 RS | Nehodnoceno |
Výsledné hodnoty byly porovnány s referenčními hodnotami, které byly naměřeny na vzorcích po 28 dnech. Toto vyhodnocení je zde prezentováno jako index mrazuvzdornosti. V tabulce jsou uvedeny hodnoty dynamického modulu pružnosti po jednotlivých cyklech a pro referenční vzorky, které byly uloženy ve vodě. Výsledky dynamických modulů zkoušených v průběhu zmrazovacích a rozmrazovacích cyklů ukazují u většiny směsí výrazný pokles již po 25 cyklech. Pouze 3 směsi vydržely všech 100 zmrazovacích a rozmrazovacích cyklů (Graf 4). Z těchto pouze dvě směsi (RECC 320 I RS* a RECC 300 RS) splnily podmínku mrazuvzdornosti. Tedy, že dynamický modul pružnosti nepoklesl o více než 25 % oproti referenčnímu měření, které bylo provedeno na stejných vzorcích před vložením do zkušebního zařízení. Ostatní směsi nedosáhly dle této podmínky mrazuvzdornosti ani 25 cyklů.
Vyhodnocení bylo dále provedeno pro pevnost v tahu za ohybu po 0 a 100 cyklech (Graf 5). V tabulce (Tabulka 6) jsou uvedeny hodnoty pevnosti v tahu za ohybu po jednotlivých 100 cyklech a pro referenční vzorky, které byly uloženy ve vodě.
Směs | Mrazuvzdornost – pevnost v tahu za ohybu [MPa] | ||||||
---|---|---|---|---|---|---|---|
Pevnost v tahu za ohybu [MPa] | σ | Index mrazuvzdornosti z pevnosti v tahu za ohybu [%] | |||||
0 | 100 | 100R | 0 | 100 | 100R | ||
RECC 320 RS* | 5,6 | 2,1 | 5,2 | 0,2 | 0,3 | 0,4 | 37 % |
RECC 320 I RS* | 5,9 | 4,7 | 5,4 | 0,1 | 0,3 | 0,2 | 79 % |
RECC 320 RS | 3,4 | porušené | 5,0 | 0,1 | 0,0 | 0,2 | – |
RECC 320 I RS | 3,2 | porušené | 4,4 | 0,3 | 0,0 | 0,2 | – |
RECC 300 II RS | 3,9 | 3,8 | 5,8 | 0,2 | 0,3 | 0,2 | 97 % |
RECC 280 II RS | 2,6 | porušené | 5,2 | 0,5 | 0,0 | 0,1 | – |
RECC 280 RS | 4,6 | porušené | 4,9 | 0,2 | 0,0 | 0,1 | – |
RECC 260 I RS | 4,3 | porušené | 4,8 | 0,2 | 0,0 | 0,3 | – |
RECC 260 RS | Nehodnoceno |
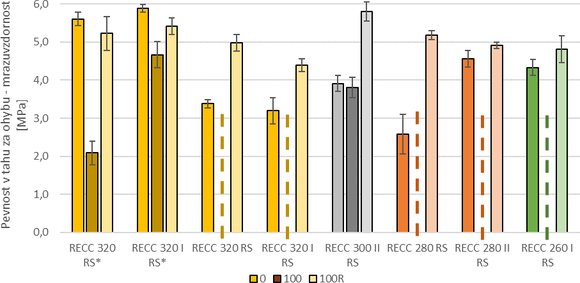
Graf 5 Pevnosti v tahu za ohybu pro vzorky ve stáří 28 dní (před zmrazováním), po 100 zmrazovacích a rozmrazovacích cyklech a referenční vzorky uložené ve vodě (stáří cca 60 dní). Přerušované čáry značí vzorky, na kterých již v důsledku porušení nebylo možné pevnost v tahu za ohybu zkoušet.
Výsledky pevnosti v tahu za ohybu pro vzorky ve stáří 28 dní (před zmrazováním), po 100 zmrazovacích a rozmrazovacích cyklech a referenční vzorky uložené ve vodě (stáří cca 60 dní) ukazují, že u většiny směsí nebylo po 100 cyklech možné pevnost v tahu za ohybu měřit. Pouze 3 směsi vydržely všech 100 zmrazovacích a rozmrazovacích cyklů, z čehož dvě směsi (RECC 320 I RS* a RECC 300 RS) splnily po 100 cyklech podmínku mrazuvzdornosti. Pevnost v tahu za ohybu nepoklesla o více než 25 % oproti referenčnímu měření, které bylo provedeno na stejných vzorcích před vložením do zkušebního zařízení. Tento výsledek plně koresponduje s výsledky měření dynamických modulů pružnosti. Referenční směsi, které byly po dobu zkoušení mrazuvzdornosti uloženy ve vodě (označení 100R) ukazují u většiny směsí nárůst pevnosti v tahu za ohybu. Stáří těchto vzorků byla přibližně 60 dní.
4. Závěr
Tento článek prezentoval vyhodnocení zkoušených vlastností betonů s využitím recyklovaného cihelného kameniva (RCK) pocházejících ze stavebního a demoličního odpadu. Bylo vybetonováno celkem 9 směsí, které obsahovaly pouze RCK. V příspěvku jsou publikovány vlastnosti, které byly podstatné pro výběr směsi, která je nejvhodnější pro konkrétní použití v praxi. Z fyzikálních vlastností byla zkoušena objemová hmotnost a nasákavost, z mechanických vlastností pevnost v tlaku a v tahu za ohybu a moduly pružnosti. Z trvanlivostních charakteristik byla ověřena mrazuvzdornost. Cílem bylo nalézt optimální variantu pro betonáž konstrukčních dílců pro pozemní stavby. Pro použití v praxi se jako nejvhodnější jeví směs RECC 300 II, která měla 300 kg cementu na m3 a efektivní vodní součinitel 0,55. Z této směsi byly v rámci spolupráce v betonárce RS vyrobeny konstrukční dílce s využitím jako prvky prefabrikovaného základu pro suché zdění. Dílce byly použity pro stavbu modelového rodinného domu nedaleko Plzně, na kterém probíhá monitoring odolnosti a trvanlivosti při reálném zatížení klimatickými vlivy.
Poděkování
Tato práce vznikla za finanční podpory MŠMT v rámci programu NPU I č. LO1605 a MPO TRIO FV 10397 – RENCO Recyklovaný environmentální beton pro stavební konstrukce.
Reference
- Cachim PB. Mechanical properties of brick aggregate concrete. Construction and Building Materials 2009; 23: 1292–1297.
- Debieb F, Kenai S. The use of coarse and fine crushed bricks as aggregate in concrete. Construction and Building Materials 2008; 22: 886–893.
- Yang J, Du Q, Bao Y. Concrete with recycled concrete aggregate and crushed clay bricks. Construction and Building Materials 2011; 25: 1935–1945.
- Guo H, Shi C, Guan X, et al. Durability of recycled aggregate concrete – A review. Cement and Concrete Composites 2018; 89: 251–259.
- Yildirim ST, Meyer C, Herfellner S. Effects of internal curing on the strength, drying shrinkage and freeze–thaw resistance of concrete containing recycled concrete aggregates. Construction and Building Materials 2015; 91: 288–296.
- Bogas JA, de Brito J, Ramos D. Freeze–thaw resistance of concrete produced with fine recycled concrete aggregates. Journal of Cleaner Production 2016; 115: 294–306.
- Gokce A, Nagataki S, Saeki T, et al. Freezing and thawing resistance of air-entrained concrete incorporating recycled coarse aggregate: The role of air content in demolished concrete. Cement and Concrete Research 2004; 34: 799–806.
- Salem RM, Burdette EG, Jackson NM. Resistance to Freezing and Thawing of Recycled Aggregate Concrete. MJ 2003; 100: 216–221.
- Limbachiya MC. Recycled aggregates: Production, properties and value-added sustainable applications. J Wuhan Univ Technol-Mat Sci Edit 2010; 25: 1011–1016.
- Limbachiya MC, Leelawat T, Dhir RK. Use of recycled concrete aggregate in high-strength concrete. Mat Struct 2000; 33: 574–580.
- Sun J-Y, Geng J. Effect of particle size and content of recycled fine aggregate on frost resistance of concrete. Jianzhu Cailiao Xuebao/Journal of Building Materials 2012; 15: 382–385.
- Liu Q, Cen G, Cai L, et al. Frost-resistant performance and mechanism of recycled concrete for airport pavement. Huazhong Keji Daxue Xuebao (Ziran Kexue Ban)/Journal of Huazhong University of Science and Technology (Natural Science Edition) 2011; 39: 128–132.
- Salem RM, Burdette EG. Role of chemical and mineral admixtures on physical properties and frost-resistance of recycled aggregate concrete. ACI Materials Journal 1998; 95: 558–563.
- Gokce A, Nagataki S, Saeki T, et al. Freezing and thawing resistance of air-entrained concrete incorporating recycled coarse aggregate: The role of air content in demolished concrete. Cement and Concrete Research 2004; 34: 799–806.
- ČSN EN 12620+A1 Kamenivo do betonu.
- ČSN EN 206+A1 Beton – Specifikace, vlastnosti, výroba a shoda.
This article deals with the possibility of using masonry aggregate from construction and demolition waste. The article summarizes the properties of concrete with a laboratory-optimized recipe with a full replacement of natural aggregate with recycled masonry aggregate. Testing of concrete samples was carried out according to valid standards. The result is a mixture with optimized properties for the production of construction parts.